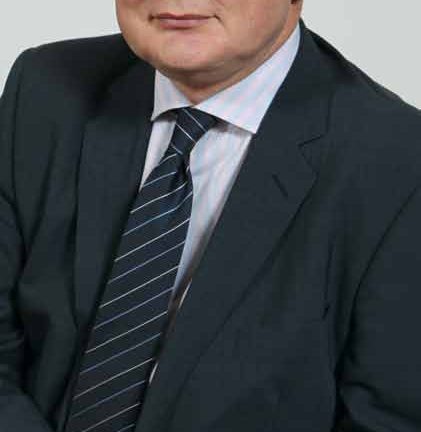
Атакуя клонами
Не секрет, что к проектной документации на строительных площадках всегда масса нареканий и претензий. Наладчики костерят проектировщиков на чем свет стоит, а последние, в свою очередь, всегда обвиняют техников в неумении понять схемы и цифры, расписанные на бумаге.
Возможно ли примирить эти два «клана» специалистов и как минимизировать ошибки, которые неизбежно возникают по причине разногласий? Будущее – за типовыми проектами и типовыми решениями, поскольку лишь построенный типовой проект, тиражируемый на других станциях, показывает хорошую слаженную работу, утверждает вице-президент НИАЭП Владимир Павлов.
Владимир Николаевич, давайте обозначим главную проблему – как избежать ошибок на стадии проектирования? Такое вообще возможно?
Сразу скажу, что есть люди, которые отвечают за проектирование, у которых может быть свой взгляд, свое понимание проблематики. Я выступаю как главный ответственный за работу с заказчиком. Часто слышу претензии: то язык не тот, то ошибок много. Согласитесь, было бы отлично иметь типовой, отработанный проект. А мы работаем на зарубежных объектах по индивидуальному проекту, когда каждый из них новый: выпускается новый проект, новая рабочая документация, и сроки везде сжатые.
Важно понимать, что для работы на мировом рынке и конкурентоспособности не существует сроков, которые можно было бы позволить себе отвести для спокойной отработки всех замечаний, устранения всех недоделок и доведения до идеала. Поэтому, когда мы делаем каждый раз новый проект, ошибки бывают. На мой взгляд, самое правильное решение для борьбы с многочисленными ошибками и жалобами – типовой проект и типовые решения. Именно к этому вся отрасль и идет. Проект ВВЭР-ТОИ является типовым, сделан в новых информационных технологиях. И вот надежда именно на типизацию, на типовой проект, который позволит избежать ошибок, человеческого фактора и погрешностей.
Зарубежные участники рынка, например китайцы, позиционируют себя как быстрые строители АЭ С. 5 лет для них нормальный срок, у нас же всегда закладывается 10. С чем это связано и как нам ускориться?
Да нет у них пяти лет! Надо эти цифры привести к одному пониманию. Давайте считать года строительства с даты первого бетона. Нашими конкурентами декларируется, что с первого бетона можно в три года построить станцию, но ведь никто не построил еще! А мы сейчас декларируем 4 года – это ВВЭР-ТОИ. Мы сегодня имеем практику сооружения 5 лет, а коллеги, которые декларируют 3 года, такой практики вообще не имеют. Поэтому, конечно, не всё правда, что они говорят, – это всего лишь декларация. И тезис о том, что у них 5 лет, а у нас 10, – в корне неправильный.
Далее, давайте коснемся вопроса подготовительного периода. Если строится типовой проект, да еще и на выбранной площадке, которая прошла все изыскания, то подготовительный период практически равен нулю.
А если строить новый проект на новой площадке, то это изыскания, это новая двухлетняя разработка проекта, это лицензирование проекта, его согласование, и все это время занимает. Так что «от первого бетона» наши цифры сильно не отличаются, и они конкурентоспособны. Отличаются они в основном декларациями.
Скажите мне, где реально станции таких мощностей и технологий построены за короткое время? Однако амбициозные задачи сооружения АЭС за 36 месяцев от первого бетона надо ставить перед собой, и мы такие задачи ставим, ибо это на сегодня одно из главных конкурентных преимуществ.
Система мотивации проектных организаций, предполагающая значительные премии в случае снижения стоимости проектов, увы, не заработала. В прошлом году на конференции по проектированию признали, что сотрудники либо не знают, как достичь экономии, либо не верят, что им заплатят. В чем, на ваш взгляд, здесь скрыта основная проблема?
На мой взгляд, дело в том, что задача выстраивания такой мотивации сама по себе очень сложная. Вообще возможна ли подобная мотивация? Так как я не занимался этим профессионально, могу поделиться лишь своим субъективным мнением: выстроить ее очень и очень непросто. Занято очень большое количество людей, как вы понимаете, не один человек сидит и проектирует. Специалист на своей системе сэкономил 1 тонну железа трубопроводов. Он сэкономил, а его смежник – строитель или электрик – увеличил в смежном чертеже на такую же стоимость. Поэтому рядовые работники, а это основные трудозатраты, просто не могут глобально охватить все взаимосвязи проекта и последствия. Это могут сделать руководители, которые в итоге контролируют общую стоимость блока. Они могут так сделать по конечным результатам разработки проекта, а это два-три года ждать! А для работника дорога ложка к обеду! А срок строительства ведь никто не отменял, и надо делать быстро, иначе теряем конкурентоспособность!
Поэтому само внедрение такой системы, как мне кажется, теоретически возможно, но это очень и очень сложный процесс. Это должны быть какие-то регламенты для всех уровней работников, какие-то постоянные семинары, совещания, которые позволят раз в месяц, раз в квартал подводить промежуточные итоги и как-то аккумулировать всю информацию. Одним словом, этот процесс очень сложно выстроить. И одним из главных вопросов в этой области является нормативная база. Именно нормативная база является главным ограничением по удешевлению проектов. Работа в этом направлении может принести положи- тельный результат.
Половина нарушений так или иначе связана с проектированием. Инженеры жалуются, что основная проблема – низкая проработка технических решений. Где здесь камень преткновения и какие основные проблемы при проектировании необходимо устранить в первую очередь?
Я это оцениваю следующим образом: коллеги на площадке, в основном это люди из эксплуатации и наладки, критикуют проектную работу. В львиной доле процентов это субъективный взгляд. Им так удобно. Тем людям, кто потом эксплуатирует и налаживает, им просто вот так вот удобно! Но ведь это далеко не значит, что это неправильно сделанное техническое решение в проекте. Уровень проектировщиков у нас высокий, квалификация у них очень высокая. Конечно, растут объемы и привлекается молодежь, которую надо обучить, но общий уровень у нас высокий.
Каждый проект практически новый, поэтому опять скажу, что решение лежит в типовом проекте. Построенный типовой проект, тиражируемый на других станциях, показывает хорошую работу. Это наша практика.
Скажем, 320-й проект – это Советский Союз. Это блоки Калининский, Ростовский и другие, все они сделаны по типовому проекту, там блоки строятся, налаживаются и пускаются. Конечно, со своими проблемами, но там отсутствуют проблемы головных блоков, где схемные решения отработаны. Вспоминаю слова очень опытного человека в нашей отрасли, Эдуарда Саакова, о том, что на Калининской станции результаты некоторых испытаний заведомо известны, и их проведение является формальной необходимостью. То есть это отработанные вещи, и все ошибки и проблемы давно исправлены. Справедливости ради надо сказать, что и на типовых блоках из-за оборудования разных поставщиков возникают проблемы, но это уже другая история.
Чем работы по проектированию зарубежных строек отличаются от внутренних, скажем, на примере Бушерской АЭ С? Есть ли принципиальные отличия по документации?
Знаете, здесь бы я выделил два отличия. Первое – это использование нормативной базы. Второе – это работа с заказчиком. По нормативной базе в России все понятно, используется наша нормативная база. На зарубежных стройках используется нормативная база страны пребывания, а также могут использоваться европейские нормы и американские. Это имеет существенное значение для процесса проектирования и лицензирования.
Что касается работы с заказчиком, то здесь заказчик известный, опытный, квалифицированный – это концерн Росэнергоатом, он единый. У них единые подходы, стандарты. С ним работать может быть сложно, тяжело, как и с любым заказчиком, но зато все понятно. И заказчик опытный, он знает свои функции.
На наших зарубежных объектах заказчик неопытный в основном, он свои функции до конца не понимает. Поэтому и времени на доказательства каких-либо его решений необходимо относительно больше. Он менее профессиональный, чем российский заказчик, из-за этого существует своя специфика. Практически у всех наших заказчиков стоит задача учиться. Им руководство откровенно ставит задачу учиться, поэтому они тратят огромное время на вопросы, расспросы, пояснения. Они так учатся.
Бушер – знаковый для Росатома долгострой по многим причинам. Какой позитивный опыт необходимо извлечь из этого долгостроя?
Я вообще считаю, что в этом проекте весь опыт позитивный. Главный позитив в том, что блок АЭС введен в эксплуатацию при строительстве в неимоверно сложных технических условиях, климатических условиях, с учетом, что и эвакуации были, и санкции… Тем не менее имидж России как партнера, который обязательно держит слово и выполняет работу, был непоколебим. Не только Иран восхищен тем, что мы достроили, хотя ведь тогда никто в мире не верил, что это возможно вообще и с технической, и с политической точки зрения. Думали, построят-построят и бросят.
Во-вторых, вы же знаете, что Бушер – это первая наша станция, которая начала сооружаться после длительного застоя в атомной отрасли. В России еще ничего не возобновилось, а тут вот – раз! – и началось. И этот объект позволил некоторым компаниям просто сохраниться, не умереть и не исчезнуть. Это и строительный комплекс, некоторые наши компании, которые сегодня работают на наших стройках, и промышленность в том числе. Еще бы немножко, и полностью потеряли бы промышленность, какие-то направления.
В-третьих, кадры. На многих объектах, которые мы строим, руководителями работают выходцы из Бушера, которые работали и прошли Бушер. Сегодня вообще трудно найти среднее звено и вторую линию руководителей на наших стройках, которые не были бы в Бушере. Так что кадры – это великое дело, это обученные люди, прошедшие и положительный, и отрицательный опыт.
И есть еще важный момент – это укомплектованность трудовыми ресурсами. Условия в Бушере очень сложные: там жарко, там влажность, другая культура, уклад жизни. При сооружении мы недооценили проблемы по укомплектованности трудовыми ресурсами этого объекта. Поэтому трудовые ресурсы за рубежом сейчас надо оценивать более трезво и более взвешенно.