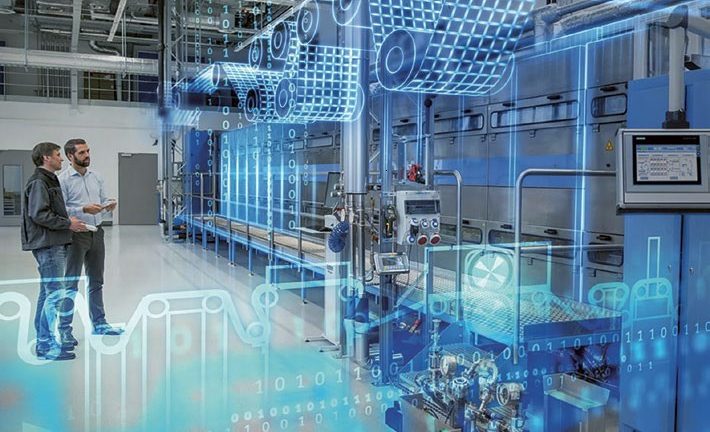
Эволюция лидера
Ступени бережливости
Базовая модель развития бережливых предприятий в Росатоме была сформирована еще в 2015 году, когда началось системное развертывание Производственной системы Росатома (ПСР). Тогда эта модель состояла из четырех ступеней. На первой находились предприятия с неразвитой производственной системой, на второй — достигшие ПСР-минимума и зачисленные в резерв. Системно выполняя требования базового уровня, можно перейти на третью ступень и стать ПСР-кандидатом. На четвертой ступени — лидеры ПСР. Основные критерии статуса: выполнение бизнес-показателей по снижению затрат, запасам и производительности труда, создание ПСР-образцов на уровне лучших мировых практик в области организации производства, реализация проекта по внедрению ПСР как минимум у одного поставщика и т. д.
Сотрудники предприятий-лидеров пользуются привилегиями, например ездят на российские и зарубежные заводы для обмена опытом, получают сертификаты на обучение в Академии Росатома.
Статус лидера ПСР присваивается предприятию на год, затем его нужно подтвердить. Сейчас в контур системного развития ПСР включены 36 предприятий, из них 33 — лидеры ПСР, они формируют более 80 % выручки в Росатоме.
В 2017 году ПСР-лидеры стали создавать ПСР-образцы в производстве на уровне лучших мировых практик — эталонные потоки и участки, где могут обучаться сотрудники других предприятий. Далее в течение 4 лет было создано более 100 ПСР-образцов в 19 типах производственных процессов. «Мы задумались: а куда наши лидеры должны двигаться дальше? Лучший способ сделать оптимизированные процессы еще эффективнее — цифровизация. Так появился новый уровень — Lean Smart Plant», — рассказывает директор проекта проектного офиса по программе развития производственных систем в отрасли Антон Широких.
Свои бережливые системы развивают и другие российские корпорации, однако до глубокой цифровизации процессов пока не дошел никто. А вот за рубежом примеры для подражания есть. «Мы на них и равняемся — в первую очередь на Boeing и Toyota. На Toyota оцифровано все производство. Везде применяют датчики, считыватели штрихкодов и QR-кодов, электронные табло, на которые выводится информация о ходе производства, качестве продукции и состоянии оборудования: где наладка, где аварийный простой и т. д. Применяется система сценарного планирования производственной программы, моделирования технологических процессов, вся конструкторская работа идет в 3D в специализированных системах CAD и CAE. У Boeing цифровая система производственного планирования и контроля позволяет отследить статусы заказов и работу заводов в цепочках поставок по всему миру», — рассказывает Антон Широких.
Lean Smart Plant — часть отраслевой стратегии «Lean Smart на 360 градусов», в рамках которой бережливые подходы и цифровизация внедряются не только на производствах и при сооружении АЭС, но также в государственном и муниципальном управлении, сфере социального обслуживания.
Алексей Лихачев, генеральный директор госкорпорации «Росатом»: «Одно из направлений, по которому я жду прорыва, — это цифровизация в ПСР. Росатом уже является лидером в области Lean, а теперь мы должны стать лидерами в теме «Lean Smart на 360 градусов» среди госкорпораций»
Сергей Обозов, заместитель гендиректора по развитию Производственной системы госкорпорации Росатом: «”Lean Smart на 360 градусов” — тема злободневная. Пришло время ускоренной цифровой трансформации. Нам надо оцифровать образцы в процессах обеспечения производств, сделать цифровые образцы в производстве, идти в цифровизацию потоков»
В цифровой волне
В 2019 году офис ПСР с департаментом информационных технологий и департаментом цифровой трансформации сформулировали общее направление развития Lean Smart Plant. Все процессы, которые планируется оптимизировать при помощи «цифры», разделили на четыре волны. В первую вошли самые важные для производства: производственное планирование и контроль, конструкторско-технологическая подготовка производства, контроль качества и управление лабораторными работами, техническое обслуживание и ремонт оборудования, материально-техническое обеспечение. «Результатом бережливой цифровизации должно стать сокращение времени протекания процессов и оборачиваемости запасов, повышение выхода в годное, производительности труда и эффективности использования оборудования. Выход предприятий на уровень Lean Smart Plant — задача ближайших двух лет», — объясняет Антон Широких.
Вначале улучшениями в рамках Lean Smart Plant в Росатоме занялись Машиностроительный завод, Чепецкий механический завод, Ковровский механический завод, ОКБМ им. Африкантова, Центральное конструкторское бюро машиностроения и «ЗиО-Подольск». Были сформулированы критерии оценки зрелости процессов, над которыми предприятия планировали работать. Считается, что цифровизировать можно только те процессы, зрелость которых превышает 80 %, то есть они уже оптимизированы и интегрированы в процессную модель.
С 2021 года предприятия приступили к оцифровке процессов, в первую очередь к доработке информационных систем. «В ходе производственного планирования важно иметь возможность моделировать сценарии выполнения производственной программы на основании фактов, собранных в режиме онлайн. В части конструкторско-технологической подготовки производства важным является моделирование технологического процесса до начала отработки технологии на опытных изделиях. Нужно обеспечить связь информационных систем и материальных потоков через считыватели штрихкодов и QR-кодов, машинное зрение. Производство должно получать обратную связь через информационные табло, инфокиоски и планшеты», — перечисляет Антон Широких. По итогам работы будет принято решение, какие процессы второй волны и на каких предприятиях запускать.
Евгений Абакумов, директор по ИТ Росатома:
«Под Lean Smart Plant мы понимаем предприятие, которое должно обеспечивать задачу по созданию продукции максимально быстро и при этом с минимальными затратами. Нам предстоит проделать огромную работу по разным направлениям — ПСР, цифровизация, стандартизация, методология в области управления производством. И все это должно быть синхронизировано на уровне отдельных цехов, участков, предприятий. И сейчас на самом старте особенно важно разработать форматы взаимодействия и убедиться, что мы одинаково видим конечную цель и участие в процессе каждого вовлеченного подразделения»
Исключить тяжелый труд
Перечень ключевых проектов Lean Smart Plant, запланированных к реализации на предприятиях Росатома в 2021 году, был представлен в декабре прошлого года на отраслевом совещании руководителями служб ПСР и ИТ. Там же было решено, что переход предприятий Росатома в статус Lean Smart Plant будет происходить в три этапа: оптимизация процессов, затем их автоматизация и, наконец, глубокая цифровизация — внедрение таких технологий, как цифровой двойник, искусственный интеллект, интернет вещей, суперкомпьютерный инжиниринг и пр. Конечная цель Lean Smart Plant — создание предприятия, конкурентоспособного на мировом рынке.
В рамках Lean Smart Plant предприятиями отрасли при поддержке проектного офиса ПСР, департамента информационных технологий и департамента цифровой трансформации разрабатывается дорожная карта создания цифровых ПСР-образцов на промышленных предприятиях атомной отрасли. К марту 2021 года развитием цифрового бережливого производства занималось уже 20 предприятий, входящих в контур Росатома.
Один из самых интересных образцов Lean Smart Plant планируется создать на «Петрозаводскмаше». Это будет комплексный образец, который соединит среднесрочное планирование модернизации мощностей и инвестиций, производственное планирование и контроль, а также конструкторскую и технологическую подготовку производства. «Все процессы оптимизируем и оцифровываем одновременно, используя цифровой двойник производства. В нем же проведем картирование, смоделируем оптимальные потоки. Фактически мы еще и оптимизируем собственную работу. Ведь одно дело, когда ты картируешь процессы на бумаге или при помощи элементарных офисных приложений, а совсем другое — когда обращаешься за помощью к специализированной информационной системе. Она поможет просчитать огромное количество вариантов оптимизации производства, а нам останется лишь выбрать наилучшее решение, управляя критериями оптимизации», — объясняет Антон Широких. Затем этот образец будет тиражироваться на другие предприятия отрасли. Следующий этап — внедрение и обучение искусственного интеллекта, который будет анализировать данные информационной системы и выбирать оптимальное решение самостоятельно. Эта работа будет проводиться уже в рамках глубокой цифровизации.
В идеале необходимо создать полностью автономное производство, исключающее тяжелый труд и пассивное наблюдение человека. «На такое производство человеку надо будет лишь завезти нужные материалы. Дальше с ними будут работать роботы, каракури, автоматическое оборудование, а на выходе мы получим готовое изделие. Думаю, со временем в автономном режиме получится изготавливать такие изделия, как корпус реактора. Если смотреть на производственный цикл, то уже сейчас от 20 % до 70 % операций при изготовлении корпуса реактора выполняется без участия человека, — объясняет Антон Широких. — А вот автономное изготовление мелкосерийных, единичных изделий большой номенклатуры (10000 и более наименований), можно считать вызовом для автоматизированных цифровых производств. Для этого потребуется гибкость, которую пока обеспечить сложно».
Lean Smart Plant: примеры успешного внедрения
Чем цифровизация помогает бережливости уже сейчас и какую работу отберут у человека цифровые инструменты в будущем
Илья Нетронин, заместитель гендиректора по операционной эффективности АО «ОКБМ Африкантов»:
В 2020 году в ОКБМ завершено создание двух ПСР-образцов, соответствующих критериям Lean Smart Plant: материально-техническое обеспечение (МТО) и конструкторско-технологическая подготовка производства (КТПП). Оптимизацией этих важнейших процессов мы занимаемся более 10 лет, успешно применяя в них информационные технологии и отдельные инструменты цифровизации.
Чего мы достигли к сегодняшнему дню? Разработка конструкторской документации осуществляется в формате 3D, обеспечивая возможность использования создаваемых 3D-моделей на всех этапах жизненного цикла наших изделий. В рамках КТПП согласование конструкторской и технологической документации происходит исключительно в электронном виде, участники процесса работают с электронными подлинниками технологической документации, пилотные участки производственных подразделений перешли на безбумажную технологию работы. В цехах мы установили информационные киоски, которые позволяют рабочим и мастерам получать доступ к конструкторской и технологической документации, включая 3D-модели изделий и 3D-технологические процессы. Это не только сокращает время протекания процесса, но и обеспечивает высокое качество изготавливаемой продукции, а также повышает прозрачность выполняемых операций. При этом все участники процесса, начиная от конструктора и заканчивая службой снабжения, работают в едином информационном пространстве.
В рамках усовершенствования процесса МТО мы обеспечили формирование и отслеживание в электронном виде графика обеспечения производства материалами, синхронизированного с графиком запуска изделий в производство. Важное достижение — использование системы, которая называется «светофор». В атомной отрасли зачастую используются особые материалы, которые поставщики не всегда могут поставить точно вовремя. Поэтому конструктор, выбирая материал для своего изделия, видит базу доступных материалов в режиме «светофора» — напротив каждого стоит специальная цветная метка. Если она зеленого цвета, то материал можно заказать без проблем, а значит — сократить цикл подготовки производства. Желтый цвет означает, что вероятны проблемы с заказом такого материала — например, долгий цикл изготовления поставщиком. Красный цвет сигнализирует о том, что материал купить практически невозможно и его следует выбирать только в том случае, если нет альтернативы. В ОКБМ активно используется система штрихкодирования, чтобы быстро идентифицировать материалы и выполняемые операции — вначале на складе, а потом на производстве. Штрихкод позволяет кладовщику получить всю необходимую информацию: что это за материал, по каким документам и под какой заказ он поступил, сколько его в наличии и в резерве.
Важнейший эффект работы созданных образцов — сокращение времени протекания процесса. Например, время разработки технологической документации на перегрузочную машину сократилось на 28 %, время от подачи заявок на перемещение с центрального склада в производство до ее выполнения сократилось на 12 %, время согласования различной документации при подготовке производства сократилось в 2–3 раза.
Цели 2020 года по развитию образцов МТО и КТПП достигнуты, но работа в этих направлениях будет продолжена — у нас еще есть резервы, которые могут быть использованы за счет применения цифровизации.
В 2021 году у нас должен появиться новый образец Lean Smart Plant для процесса «Техническое обслуживание и ремонт оборудования». У нас уже имеется неплохой задел в этом направлении, осталось применить инструменты мониторинга состояния наших станков, обеспечить использование аналитических инструментов. Результатом создания нового ПСР-образца станет сокращение времени простоя производственного оборудования.
Один из ключевых факторов достижения стратегических бизнес-целей предприятия на горизонте до 2030 года — цифровизация ключевых процессов. Мы уже начали тестировать и использовать новые цифровые технологии и инструменты. Например, применяем элементы машинного зрения при входном контроле приобретаемых материалов, используем программных роботов при проведении закупочных процедур и в работе с поставщиками, расширяем использование аддитивных технологий в производственных процессах, работаем с поставщиками решений в области дополненной и виртуальной реальности.
Бояться того, что цифровые инструменты отберут всю работу у человека, не стоит. Ведь даже искусственный интеллект необходимо будет обучать, и здесь у наших инженеров, конструкторов, технологов и рабочих останется обширное поле деятельности. Просто их работа станет более творческой и экспертной.
Комментарий
Григорий Удод, начальник отдела планирования, исследований и контроля производства Чепецкого механического завода:
С 2020 года в цехе трубного проката ЧМЗ развиваются два образца в рамках стратегии Lean Smart Plant. Первый — «Техническое обслуживание и ремонт оборудования (ТОиР)», второй — «Планирование производства».
За предыдущий период мы хорошо поработали над образцом ТОиР, все — планирование и контроль обслуживания, ремонт оборудования — происходит в одной операционной системе. Появилось много интересных аналитических решений. Например, для повышения точности планирования ремонтов, увеличения межремонтного интервала организованы сбор и обработка информации о применении комплектующих материалов за счет использования вибродиагностических комплексов на прокатных станах. Определение состояния конструктивно сложных узлов критического оборудования происходит в режиме реального времени. По показаниям приборов можно судить о степени износа узла и необходимости его ремонта или замены.
Еще одно интересное системное решение — оповещение руководителей о неисправности ключевого оборудования по цепочке помощи через SMS. В случае поломки станка оператор, пользуясь специальной функцией в MES-системе, отправляет сообщение ремонтной службе. Если за отведенное время сервисные службы не приступают к ремонту, то сообщение о неисправности автоматически пересылается руководителю ремонтной бригады, а через пару часов информация о простое важного для потока оборудования может дойти и до генерального директора предприятия. Понятно, что такая перспектива никого не вдохновляет, поэтому ремонт станков стартует незамедлительно.
В рамках развития второго образца — «Планирование производства» — мы совершенствуем долгосрочное, среднесрочное и оперативное планирование производства, выравниваем загрузку оборудования, сокращаем запасы и обеспечиваем поставку продукции точно в срок.
По итогам года время перепланировки — от корректировки заявки потребителя до выпуска измененной программы производства — сократилось в 2 раза, НЗП уменьшилось более чем на 41 тонну. Влияние проекта на бизнес-цель «Запасы» составило порядка 60 млн руб.
В 2021 году будем тиражировать работу обоих образцов в другие цехи и запустим третий образец Lean Smart Plant — «Контроль качества и управление лабораторными работами». Речь идет о совершенствовании лабораторных процессов, обслуживании лабораторного оборудования, онлайн-наблюдении за процессом и результатом исследований, автоматическом формировании отчетов. В рамках развития данного образца проработаем тему с внедрением в производство роботов-доставщиков. Эта тема, несмотря на свою простоту и очевидность, влечет за собой создание целой информационной и логистической инфраструктуры. Цель — снижение времени ожидания лабораторных исследований.
Сейчас перед нашей командой стоит задача разработки стратегии развития Lean Smart на ЧМЗ до 2030 года. В будущем мы обязаны всю физическую работу на производстве передать автоматическим системам и роботам, а потенциал человека сконцентрировать на интеллектуальном труде. Считаю, что участки, где люди работают в тяжелых условиях, необходимо автоматизировать и механизировать в первую очередь. Пока этого не произошло, мы постараемся облегчить работу людей настолько, насколько это возможно. Например, использовать экзоскелеты, снижающие нагрузку при физической работе. Как раз в ближайшие дни мы проводим первые испытания.