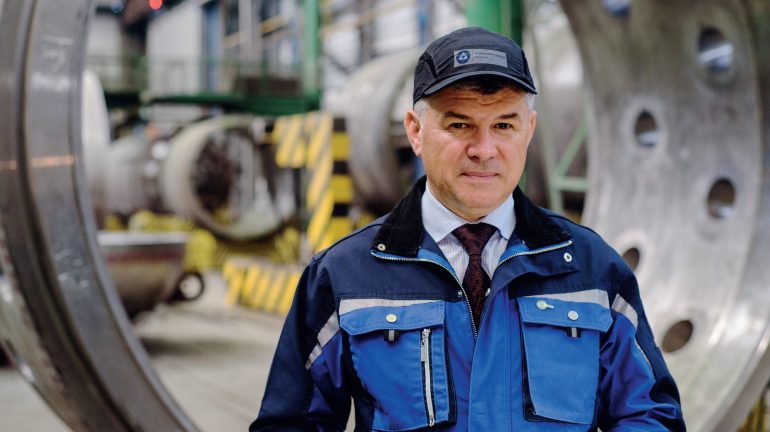
«Перед нами стоят серьезные задачи, и мы к ним готовы»
Генеральный директор «Атомэнергомаша» Андрей Никипелов — об эволюции компании, рекордных достижениях, кадровом вопросе и больших планах
— Андрей Владимирович, 15-летие дивизиона — хороший повод оценить пройденный путь. Все ли цели, поставленные при создании «Атомэнергомаша», достигнуты?
— 15 лет промелькнули очень быстро. «Атомэнергомаш» как компания создавался с нуля с главной целью: снять зависимость от внешних поставщиков основного оборудования для атомных станций. В 2006 году именно поставщики, исходя из собственных производственных возможностей, диктовали, какое количество станций и в какое время сможет строить Росатом. Точно так же диктовались и цены. Росатом, конечно, не мог себе позволить зависеть от внешних обстоятельств, поэтому «Атомэнергомаш» должен был, с одной стороны, снять риски — ценовые и срыва сроков, а с другой стороны, как гарантирующий поставщик — обеспечить необходимое количество оборудования для строительства АЭС. Все эти цели достигнуты.
— Насколько сложно это было? Какие «болезни роста» приходилось преодолевать?
— Работа была поэтапной. На первом этапе нужно было собрать активы. Часть отраслевых предприятий передавалась в управление «Атомэнергомаша», часть создавалась с нуля, часть покупалась — «ЗиО-Подольск», «Энергомашспецсталь», «Петрозаводскмаш» были первыми. В 2012 году наконец появилась возможность приобрести «Атоммаш». Дивизион получил его с долгами по зарплате и по налогам, со стоящим производством, с пустыми цехами. Мы остановили инвестпрограмму создания реакторного цеха на ПЗМ и за короткое время сделали программу по модернизации станочного парка и по всем вопросам организации производства на «Атоммаше». Это было необходимо, поскольку к тому времени волгодонское предприятие уже 20 лет не работало на атомном рынке. За нашими действиями наблюдало все профессиональное сообщество, оно было настроено достаточно скептически. Но уже в 2015 году на «Атоммаше» был готов первый корпус реактора. И в тот момент все окончательно убедились, что «Атомэнергомаш» — это серьезно и это надолго. Почему? Потому что стало понятно, что чуть раньше или чуть позже, но мы точно будем независимы от всех внешних факторов и сможем сами изготавливать все ключевое оборудование для реакторных установок и машзалов.
Дальше пришлось плотно заняться повышением эффективности производства. Нужно было убрать дублирующие функции: в то время были нередки случаи, когда три наши компании выходили на один конкурс, фактически соревнуясь друг с другом. Для всех входящих в АЭМ предприятий была введена своя специализация. Для кого-то процесс шел непросто, что называется, резали по живому: менялась номенклатура, контрактация, многое другое. Например, производство части насосов полностью — с документацией и с техническими разработками, вплоть до оснастки, — от ЦКБМ было передано ОКБМ, а ЗиО вообще лишился производства парогенераторов, хотя это тот продукт, из-за которого завод изначально покупался. Но в результате была выстроена четкая и понятная специализация по изделиям. Этот этап реконфигурации в основном завершился в 2016 году.
И параллельно шла работа над тем, чтобы стать ответственным поставщиком. Конечно, без качества, гарантирующего безопасность, нет продукта в нашем бизнесе, но мало уметь производить качественное оборудование, главное — ты должен его делать вовремя. Про «вовремя» это вообще был пунктик с начала моего появления в компании. Мы долго обсуждали простую для рынка истину, что сложно получить первый заказ, тяжело второй, а третий невозможно, если ты не выполняешь обязательства в срок. В начале нас действительно критиковали за сроки изготовления и поставок, но примерно к 2018 году по большей части номенклатуры и продукции к нам вопросов не стало. Более того, в определенный момент ситуация вообще перевернулась: для того, чтобы вовремя исполнить свои обязательства, мы стали требовать от заказчиков обеспечить отсутствие срывов и те сроки, которые нам нужны. Конечно, процесс совершенствования на этом не заканчивается.
— А как бы вы охарактеризовали этап, на котором дивизион находится сегодня?
— Сегодняшний этап — это развитие и расширение возможностей дивизиона на той мощной базе, которую мы создали. У нас в течение последних лет практически каждый год — рекордный, мы делаем больше, чем в предыдущем. В 2020-м мы достигли рекордных показателей за всю историю отечественного атомного машиностроения: в течение года выпустили 3 корпуса реактора с внутрикорпусными устройствами и 18 парогенераторов, а всего на предприятиях «Атомэнергомаша» в разной степени готовности находилось оборудование для 10 энергоблоков. По плану выручка в 2023–2024 годах должна вырасти почти вдвое по отношению к прошлому году и составить свыше 150 млрд рублей. Десятилетний портфель заказов АЭМ сейчас составляет 850 млрд рублей — это действительно огромные цифры. Пиковое производство приходится на 2023–2025 годы. Так ситуация выглядит сегодня, но «Атомэнергомаш», как и весь Росатом, работает на то, чтобы появились новые контракты. В атомном бизнесе мы стараемся взять на себя больше обязательств и расширить номенклатуру — не только поставкой оборудования, но и за счет сервиса и услуг. В неатомных бизнесах дивизион становится не просто поставщиком отдельных единиц оборудования, а идет гораздо более широким фронтом — с комплектными поставками. Одновременно с ростом валовых показателей мы работаем над повышением эффективности на всем цикле проектирования, изготовления и выпуска продукции.
— Возможно, следующий ядерный ренессанс во всем мире будет связан с атомными станциями малой мощности. Малые реакторы — это ваша тема, расскажите, как идет работа в этом направлении.
— Да, малые атомные реакторы — это то новое, что нас ждет впереди. Уже подписано соглашение с Якутией о строительстве АЭС мощностью 55 МВт. Это очень важный проект: станция не просто обеспечит энергией золоторудное месторождение Кючус и близлежащие поселки — это будет первая наземная АЭС малой мощности, которая должна стать прототипом для следующих. Для нее будет использоваться реактор РИТМ-200 (в наземной модификации). При его разработке был учтен предыдущий опыт эксплуатации малых реакторов на ледоколах, но это принципиально новое решение, не имеющее аналогов в мире: так называемая интегральная компоновка — с расположением парогенераторов внутри корпуса. Это делает РИТМ-200 легче и компактнее, но в то же время на 20 % мощнее предшественников. Головной ледокол нового поколения «Арктика» с такими реакторами с осени 2020 года работает на СМП, они же будут установлены на еще четырех строящихся ледоколах проекта 22220. Для новейших ледоколов проекта «Лидер», в рамках которого АЭМ впервые является поставщиком всего силового острова, разработаны еще более мощные реакторные установки РИТМ-400.
Так что у РИТМов большой потенциал — и на суше, и на воде. «Атомэнергомаш» отвечает за всю работу по продвижению плавучих атомных энергоблоков. И здесь мы рассчитываем на то, что получим контракт на поставку четырех плавэнергоблоков на базе реакторов РИТМ для энергообеспечения Баимской горнорудной зоны. У нас также есть проект «Оптимизированный плавучий энергоблок» (ОПЭБ): здесь уже по завершении эскизного проектирования стало очевидно, что ОПЭБ можно сделать значительно экономичнее, чем ПЭБ «Академик Ломоносов». У малой атомной энергетики однозначно большие перспективы, а у «Атомэнергомаша» есть все возможности, чтобы ее развивать.
— Какие направления на неатомных рынках вы считаете самыми важными?
— «Атомэнергомаш» всегда занимался не только атомным машиностроением — в силу специфики нашего производства. С самого начала было понимание, что деятельность дивизиона должна быть диверсифицирована, поэтому помимо освоения атомной номенклатуры АЭМ выполнял другие заказы. Постепенно эта работа становилась все более целенаправленной, мы стали заниматься ею системно и структурно, сформировались отдельные неатомные бизнес-направления и продолжают появляться новые.
АЭМ активно развивает производство оборудования для нефтегазовой отрасли, в том числе для технологий по сжижению природного газа. На ЗиО мы освоили производство уникальных кожухотрубчатых теплообменников для проекта «Ямал СПГ», заказчику их отгрузили в 2019-м. На ОКБМ осваивается целая линейка насосов, в 2020 году было успешно завершено испытание погружного насоса для перекачки СПГ — это первый крупнотоннажный криогенный насос российского производства. Сейчас насос уже в эксплуатации у крупнейшего российского производителя СПГ. Заказчик доволен, насос подтвердил все требования и характеристики. Вообще надо себе представить, что такое среда СПГ: это минус 160 градусов, насос должен там работать — и он работает. И наша следующая задача — производить больше такого уникального, наукоемкого, высокотехнологичного оборудования и иметь возможность его экспортировать.
Правительством России было принято решение о строительстве испытательного стенда для крупнотоннажного СПГ-оборудования в рамках выполнения поручения президента страны по локализации в России критически важных технологий. «Атомэнергомаш» взялся за эту задачу — в текущем году планируем ввести стенд в эксплуатацию. Это первый в Европе и третий в мире испытательный стенд такого типа. Наличие его в России даст возможность разным участникам рынка проводить именно у нас в стране испытания насосов и другого оборудования для СПГ-проектов, чтобы затем продавать и применять испытанное оборудование здесь или же поставлять его за рубеж.
Еще одно направление работы «Атомэнергомаша» — производство оборудования для мусоросжигания. АЭМ изготавливает оборудование по очень современной технологии, экологичность которой неоднократно подтверждали эксперты, в том числе зарубежные: проекты прошли 11 государственных российских экспертиз и 2 независимые международные. И эта технология не просто соответствует тем требованиям, которые есть на сегодняшний день, она превосходит их. Мы в мусоросжигание поверили — и как в бизнес, и как в хорошее и правильное дело. То, что с ним связано, точно лучше и эффективнее для экологии по сравнению с тем, что происходит сейчас, когда отходы хранятся на свалках, загрязняют грунтовые воды, выделяется свалочный газ, возникает опасность отравления им, опасность пожаров, в конце концов свалки просто занимают огромные площади. Люди часто сопротивляются чему-то новому, мусоросжигание для нашей страны — это новая тема. Есть много мифов вокруг атомной энергетики, сегодня есть столько же мифов и опасений и вокруг мусоросжигания, надо просто с этим работать.
Мы постоянно отслеживаем появление новых рыночных сегментов. Сейчас в машиностроительном дивизионе создается серьезная ресурсная база для изготовления пилотных образцов изделий методами аддитивных технологий — затем должны последовать аттестация и внедрение. Шестилетний опыт ЦНИИТМАШ по производству 3D-принтеров для металлических изделий позволяет рассчитывать на то, что мы будем иметь необходимые машины для выполнения наших задач.
— У вас каждый год рекордный и огромные планы на будущее. Как вам удается решать кадровые проблемы?
— Мы всегда, с первого этапа становления дивизиона, думали о том, как обеспечить наши предприятия лучшими кадрами. Поэтому АЭМ пережил несколько, можно сказать, волн миграции сотрудников. Например, когда с ЗиО передали парогенераторы на «Атоммаш», то вместе с парогенераторами поехали люди, которые понимали, как их делать, — и руководители подразделений и цехов, и сварщики, и сотрудники службы качества. А когда на ЗиО запустили производство реакторов РИТМ-200 — первых реакторов, которые мы делали внутри компании, — часть персонала ОКБМ (это разработчик и главный конструктор РИТМов) переместилась из Нижнего Новгорода в Подольск.
Россияне в целом, наверное, не настолько мобильны, как американцы или европейцы, для которых в порядке вещей каждые 5 лет перемещаться даже на другой конец света, неважно, руководитель ты или специалист. Для сотрудников АЭМ менять локации — нормальная практика. Я считаю, что это правильно, потому что перемещение вытаскивает человека из повседневной рутины и помещает его, хоть и не люблю это избитое выражение, за пределы зоны комфорта — заставляет его раскрыться, работать более эффективно, смотреть на привычные задачи другими глазами, решать проблемы по-другому. Мы постепенно приходим к тому, что у нас не только руководители, специалисты, инженерно-технический персонал, но и целые бригады сварщиков, монтажников, операторов станков тоже перемещаются, потому что на каких-то проектах в определенный период возникает дефицит ресурсов. В этом смысле у нас дивизион дружный, и мы всегда находим варианты, чтобы собрать нужное количество людей и переместить их в другое место для решения проблемы.
— Приходится ли доучивать или переучивать новых людей под свою специфику?
— В каждом регионе присутствия «Атомэнергомаша» мы взаимодействуем с техникумами, институтами и университетами — во многих городах есть подразделения НИЯУ МИФИ, который является базовым вузом для Росатома, в Петрозаводске мы активно работаем с ПетрГУ, в Нижнем Новгороде — с Политехническим университетом, в Волгодонске помимо филиала МИФИ сотрудничаем с Новочеркасским университетом.
У нас есть внутренняя программа по развитию кадров, причем на всех уровнях. Для специалистов и управленцев широко используем методы наставничества, считаю, что это правильно и полезно. На всех крупных предприятиях дивизиона организованы учебные центры, где мы как минимум проверяем уровень вновь пришедших, а после этого в рамках вхождения в профессию, в должность, они учатся, переподтверждают свою квалификацию уже в соответствии с нашими стандартами и повышают ее. Это касается практически всех рабочих специальностей. В учебных центрах сварщики учатся сварке, операторы станков работают на станках, это не просто какие-то симуляторы, это настоящие станки, они могут быть меньше по сравнению с теми размерами, с которыми потом нужно будет работать, зато у них та же операционная среда, та же самая система управления, и работник получает и отрабатывает те навыки, которые ему будут нужны.
— Какие ресурсы вы видите для повышения эффективности?
— Повышение эффективности — это многоуровневый процесс. Реконфигурация производств дивизиона, когда каждое наше предприятие получило свою специализацию, стала отправной точкой этого процесса. Следующая ступень — повышение эффективности на самих производствах на уровне работы над проектами. Здесь очень помогает широкое использование методов Производственной системы Росатома (ПСР). В ее основе лежат пять принципов, которые призывают сотрудников быть внимательными к требованиям заказчика (не только по отношению к конечному потребителю, но и к участку-потребителю, цеху-потребителю и даже последующему оператору); решать проблемы на месте их возникновения; встраивать качество в процесс, не производить брак; выявлять и устранять любые потери (излишние складские запасы, межоперационные заделы, время простоя, лишние перемещения и т. д.).
Об эффективности этой системы говорит тот факт, что, например, на «Атоммаше» благодаря ПСР удалось сократить срок изготовления реакторов с 760 дней до 574 и парогенераторов с 877 до 453. ОКБ «ГИДРОПРЕСС», которое в том числе производит шаговые электромагнитные приводы системы управления и защиты, предназначенные для регулирования мощности реактора, менее чем за 10 лет увеличило их выпуск почти в 2 раза. На ЦКБМ благодаря ПСР производство выемных частей удалось поднять в 3 раза. А ОКБМ увеличил выпуск парогенераторов для реакторных установок РИТМ почти в 9 раз! Во многом благодаря этим достижениям стали возможны те производственные рекорды, о которых я говорил ранее. Общий экономический эффект от внедрения ПСР в дивизионе за последние 10 лет (с 2010 по 2020) составляет более 4 млрд рублей.
Инвестиции в модернизацию производства дополнительно помогают «расшить» узкие места. Предприятия дивизиона обновляют станочный парк. В марте на ПЗМ приняли в эксплуатацию после модернизации самый большой токарно-карусельный станок сборочно-сварочного производства. Раньше станок управлялся вручную, теперь его оснастили системой ЧПУ. На «Атоммаше» ввели в эксплуатацию уникальный 3D-сканер: он оцифровывает поверхности крупногабаритных изделий, формируя облако из миллиона точек и отображая таким образом геометрические размеры изделий в реальном времени. Максимально точная оценка параметров изделий — ключевая операция в процессе контроля, необходимая для обеспечения безопасности при работе оборудования. И на это теперь затрачивается в 5 раз меньше времени!
Применение цифровых технологий — еще один путь для повышения эффективности. В прошлом году, когда закрылись границы, мы начали применять очки дополненной реальности, чтобы зарубежные заказчики могли проводить дистанционную приемку. На эту технологию мы возлагаем большие надежды. Создаем цифровые прототипы и цифровые модели ядерных установок — это сокращает сроки и стоимость проектов на всех этапах. Перечисление можно продолжать — мы идем в ногу с «цифрой».
— Если говорить о вашем дивизионе или Росатоме в целом, какие направления деятельности вы считаете самыми перспективными?
— Что мне самому очень интересно и хотелось бы, чтобы получило развитие как можно быстрее, — это, конечно, работа по замыканию ядерного топливного цикла, то, что может сделать атомную энергетику практически безотходной. Мы очень ждем решения по БН-1200, мы сделали эскизы и техпроект реакторной установки — все, что можно было сделать на стадии до проектирования атомной станции, и наши расчеты показывают, что по стоимости сооружения БН-1200 могут быть сопоставимы с реакторами ВВЭР. Сейчас «ОКБМ Африкантов» — разработчик реакторной установки и реакторного отделения БН-1200 — продолжает опытно-конструкторские работы с целью дальнейшего улучшения технико-экономических показателей. Мы верим, что проект получит развитие, и очень ждем, когда будет принято решение о строительстве таких блоков — это откроет новые перспективы для развития всей атомной энергетики.