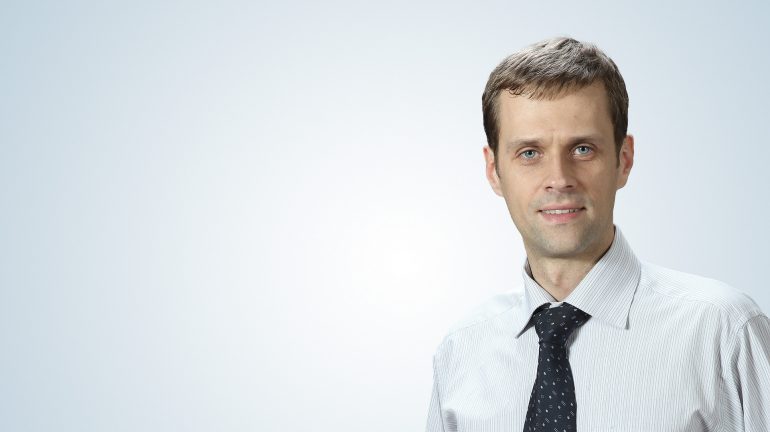
Как оцифровывалась сталь
Цифровизация производственных процессов в атомном машиностроении
Роман Токаренко, директор департамента информационных технологий АО «Атомэнергомаш», — о том, какие задачи в сфере цифровизации производства в энергомашиностроении предстоит решить и какие преимущества это даст клиентам, отрасли и дивизиону.
Информационный ландшафт
Вначале предлагаю разобраться с терминологией. Последовательность преобразований, связанная с ИКТ (информационно-коммуникационными технологиями), включает в себя уровень автоматизации, то есть дополнение традиционных бизнес-процессов возможностями ИКТ, их цифровизацию (локальные изменения процессов благодаря инновационным технологиям и инструментам, появляющимся в последнее время) и возможную цифровую трансформацию бизнеса и процессов — качественное изменение цепочек создания стоимости, создание принципиально новых продуктов, формирование новых рынков либо ниш в существующих.
Локальные процессы автоматизации на предприятиях машиностроительного комплекса атомной отрасли развивались параллельно с появлением очередных вычислительных технологий и информационных систем в стране, то есть уже несколько десятков лет. Это позволило ускорить и сделать более прозрачными многие процессы, но часто приводило к усложнению информационного ландшафта предприятий, и на текущий момент стоит задача необходимости выстраивания новых интеграционных цепочек между предприятиями дивизиона и отрасли — для обеспечения конкурентоспособности и предоставления новых ценностей нашим клиентам. Однако основа для цифровизации и, при целесообразности, для цифровой трансформации в отрасли уже сформирована.
Автоматизация, а в последнее время и цифровизация к настоящему времени затронули значительную часть основных процессов в цепочке создания стоимости в дивизионе: конструкторскую и технологическую подготовку, закупки, производство, систему управления качеством, процессы передачи продукции заказчику, поддержку на этапе эксплуатации. Кроме того, охвачены вспомогательные и поддерживающие процессы и функции.
Ключевое значение для нашего дивизиона, на мой взгляд, имеет цифровизация производственных процессов и дополнение цифровым «контентом» нашей продукции, передаваемой заказчикам. На этих направлениях мы и сосредоточились, разрабатывая в 2019 году программу цифровизации машиностроительного дивизиона и встраивая ее в единую цифровую стратегию Росатома.
Отличительная особенность задач, которые мы сейчас реализуем, — более глубокая степень интеграции процессов и данных, появление общего информационного пространства для обмена данными между подразделениями, предприятиями, дивизионами. Происходит виртуализация (создание электронных двойников) нашей продукции и процессов ее производства, мы приближаемся к уровню непрерывного управления данными об изделиях на протяжении их жизненного цикла.
Успех запланирован
Актуальная задача, которая реализуется в дивизионе с применением ИКТ, касается производственного планирования. Один из первых проектов по производственному планированию с использованием платформы 1С ERP был выполнен в АО «ЦКБМ», в разной стадии готовности — аналогичные решения для АО «ЗиО Подольск», АО «Атомтрубопроводмонтаж», филиала АО «АЭМ-технологии» в Петрозаводске. В силу исторических причин мы изначально выбрали российское платформенное решение, поэтому задача по достижению технологической независимости в планировании для нас уже в основном решена. Лишь на одной из площадок АО «АЭМ-технологии» проект производственного планирования был реализован на SAP ERP, и в настоящее время на замену готовится технологически независимое решение на платформе 1С.
Следует отметить, что для нас важен не только переход на технологически независимую платформу. Полученная унификация необходима для нового качества: получения системы планирования в масштабе дивизиона. Объединив всю совокупность задач наших производств, учитывая перспективы загрузки на годы, мы стремимся выйти на охват планирования работы всего дивизиона. При этом создаваемая метасистема напрямую интегрируется с системами планирования предприятий. Мы собираемся обеспечить долгосрочное планирование на весь объем отраслевого заказа, а также на среднесрочный (до года) и краткосрочный (до месяца) горизонты. В системах предприятий детализация планирования будет максимально глубокой, до смены (выдача, контроль выполнения посменных заданий и т. д.).
К ключевой задаче планирования, которая определяет «такт» работы производства, мы подстраиваем цифровизацию поддерживающих процессов. Так, закупочные службы, получая задания из производственного плана, должны обеспечить бесперебойное снабжение; конструкторы и технологи — выдавать вовремя затребованную проектную и рабочую документацию. Этот же принцип охватывает и другие процессы. Например, набор инженеров и рабочих планируется на годы вперед, и в этих планах HR-служба также опирается на единую для всего дивизиона основу. Имея достоверный прогноз загрузки, они могут заблаговременно подготовиться в том числе к экстенсивному развитию — проводить обучение новых работников, а также принять меры для повышения квалификации и производительности труда.
Двойник удваивает ценность
Перспектива цифровизации в конструкторско-технологическом направлении — развитие цифровых двойников продукции. Под цифровым двойником мы понимаем программную и информационную модель изделия, которая будет создаваться еще на этапе конструирования, до появления изделий в реальности. Цифровой двойник для нас актуален не столько как визуальный трехмерный образ, но как детальная база данных об изделии и набор алгоритмов (программ), позволяющих проводить моделирование свойств и режимов работы еще на этапе разработки. Опираясь на базу данных о свойствах материалов, конструкторы получат возможность расчетов для различных эксплуатационных и аварийных режимов.
Отметим, что моделирование не отменит, но дополнит систему натурных испытаний. Стендовая база на предприятиях дивизиона хорошо развита, и с учетом специфики отрасли и приоритета безопасности мы не откажемся от натурных испытаний. Но часть дорогостоящих, занимающих время тестов мы сможем заменить виртуальными расчетами. Например, даже не изготавливая опытный образец, мы с помощью программного обеспечения и цифрового двойника с актуальными параметрами сможем моделировать работу изделия. Это сократит сроки разработки изделий в целом, снизит вероятность ошибок. Основные проекты в области цифрового двойника и виртуализации испытаний нашей продукции реализуются в АО «ОКБМ Африкантов», АО «ОКБ ГИДРОПРЕСС» и АО «ЦКБМ». Мы ожидаем значительного эффекта от интеграции их идей и разработок с моделями материалов и технологий обработки, которые также разрабатываются в НПО «ЦНИИТМАШ».
Возможность виртуализировать испытания позволит нам лучше адаптироваться к требованиям внешнего рынка. Изделия для нужд атомной энергетики имеют запас, превышающий достаточные эксплуатационные требования в несколько раз; с высокой степенью документирования, проверок и т. д. строится весь процесс производства. Для неатомных рынков часто не требуется такой запас прочности, и если мы сохраняем наш подход к конструированию и изготовлению в привычном для нас «атомном» объеме, то можем проигрывать в цене, особенно на мировом рынке.
Следует отметить, что в атомной отрасли в настоящее время проводится разработка стандартов по созданию и наполнению цифрового двойника и информации, которую предприятия будут передавать друг другу и заказчику, формируя и поддерживая модель цифрового двойника. Этот вопрос необходимо решить для дальнейшей работы с двойниками, актуализации ключевых параметров на этапе эксплуатации (режимы, отклонения, дефекты, история ремонтов и т. д.) Эти данные должны не только накапливаться в эксплуатирующей организации, но и возвращаться к изготовителям и конструкторам для улучшения будущих изделий. Сегодня в основном обратную связь мы получаем лишь как рекламации, в случае инцидентов. Чтобы предотвратить проблемы, нам полезна информация о том, как нарастали признаки нештатной работы устройства, какие признаки предшествовали отказу.
Подобный пилотный проект по накоплению информации о работе оборудования и предиктивному анализу мы реализуем, например, для главного циркуляционного насосного агрегата (ГЦНА). Мы планируем передачу эксплуатирующей организации цифровых двойников вместе с готовым изделием для получения обратной связи в ходе эксплуатации (будем отслеживать порядка 400 параметров с одного изделия). Развивая такой подход, мы в перспективе можем выйти на новый вид услуги — предиктивную аналитику и поддержку оборудования на протяжении всего жизненного цикла, повышение КИУМ за счет увеличения межремонтных интервалов, проведение ТОиР на основании фактического состояния с учетом наработки и реального состояния оборудования. Если этот подход оправдает себя, в перспективе возможно развитие нашего сервиса до полного обслуживания, вплоть до того что эксплуатирующая организация начнет приобретать у нас не собственно ГЦНА, а «услугу циркуляции». Сегодня это звучит необычно, но именно таково, к примеру, развитие сервиса двигателей в авиации. Аналогичный подход будем тестировать и в отношении статического оборудования — корпусов реакторов, парогенераторов, САОЗ и других изделий. По всем этим изделиям существует задача увеличения срока эксплуатации, и мы оцениваем возможность добиться этого в том числе через технологию цифровых двойников.
Важную роль в подготовке полноценного цифрового двойника играет интеграция передаваемых элементов цифровой модели между предприятиями, в том числе из разных дивизионов. Первый проект такой интеграции мы выполнили совместно с предприятиями топливного дивизиона Росатома, где конструкторская документация разрабатывается также на платформе «Интермех»: наши площадки уже обмениваются элементами цифрового двойника. Подобные проекты планируем реализовать с электроэнергетическим и инжиниринговым дивизионами.
Улучшаем, ускоряем, контролируем
Цифровые технологии позволяют улучшить процессы организации производства. В первую очередь для нас актуален отказ от традиционных, бумажных носителей информации. Каждое изделие сопровождается большим комплектом документов: это конструкторская документация, паспорта качества, сменно-суточные задания и многое другое. В настоящее время мы находимся на промежуточном этапе, автоматизируем традиционные учетные процедуры с помощью штрих- или QR-кодов: используя сканер, можем оперативно зарегистрировать заготовку, зафиксировать переход на следующий этап. Развитие этого направления — переход к информационной поддержке всего производства, без дублирования в документах, когда прохождение заготовки (детали, изделия) по этапам начнет сопровождаться обновлением информации в единой базе данных, с процедурами контроля, аналитики и т. д. Этот подход мы уже оценили на практике в различных вариантах: нанесение специализированных кодов на изделие, RFID-метки, регистрация на терминалах и в приложениях мобильных устройств.
Наиболее активны в цифровизации таких процессов ОКБМ им. Африкантова и «АЭМ-технологии». На этих площадках также проходит тестирование инфостендов, больших мониторов в цехах, на которых рабочие могут изучить трехмерную модель изделия, зафиксировать этапы и параметры производственного процесса. На площадке АО «АЭМ-технологии» мы протестировали мобильное приложение, интегрированное с информационными системами предприятия, для изучения сменно-суточного задания, подачи заявок (подвезти инструмент, убрать мусор и т. д.) Готовим проект по оснащению части наших ключевых станков мониторами, с тем чтобы информация о модели, документах, фиксация событий были доступны непосредственно на рабочем месте.
Среди перспективных проектов цифровизации — система мониторинга производственного оборудования, СМПО. В 2021 году около 400 единиц ключевого оборудования на шести наших площадках были подключены к информационной системе, которая через ЧПУ станков или дополнительные датчики контролирует работу станков. Это позволяет накапливать актуальную статистику: определить простои, анализировать причины (поломка, отсутствие заготовки, инструмента, персонала и т. д.) Часть причин простоя фиксируется автоматически (неисправности), часть указывает работник на терминале. Так у нас появляется фактическая основа для аналитики, выявления проблем и лучших практик. Также мы получаем массивы данных для потенциального снижения рисков по срыву сроков и для влияния на качество готовой продукции. По некоторым параметрам можем оценивать состояние оборудования и предотвращать отказы (например, снимая показания датчиков вибрации). Изменение загрузки основного оборудования даже на 1 % при нашем объеме может дать эффект в сотни миллионов рублей.
Есть и другие проекты, позволяющие снизить производственные расходы. Например, управление потреблением энергоносителей (газ, тепло): установленные датчики сигнализируют о фактической потребности в ресурсе, информация накапливается, и режим расхода оптимизируется исходя из потребностей. Возможна оптимизация энергопотребления под тариф, например выстраивание режимов работы мощного оборудования.
Однако заметим, что одно из ограничений во внедрении современных информационных технологий, особенно для беспроводных носимых устройств, — требования к информационной безопасности на режимных объектах. Прямая интеграция с нашими информационными системами посредством беспроводной связи может быть реализована не везде. Мы ожидаем, что будет выработано отраслевое решение, позволяющее реализовать возможности мобильной связи.
Реальность дополнена виртуальностью
Актуальный опыт, полученный в условиях пандемии COVID-19, — дистанционная приемка. В это период мы закупили на ряд предприятий оборудование дополненной реальности и с его помощью, во-первых, осуществляли взаимную приемку между нашими площадками (проходили оценку на так называемых точках останова, когда представители заказчика убеждаются, что операция проведена корректно). С помощью дистанционной приемки мы создали эффект присутствия без приезда на предприятие. Находясь перед экраном компьютера, заказчик может осмотреть изделие глазами «аватара», по связи задать вопросы, изучить результат в подробностях. Можно использовать возможности дополненной реальности, накладывая в визуальный канал чертежи, документы, иной полезный контент. Транслируем такую модель и на общение с конечным заказчиком. Такой опыт взаимодействия сложился с китайскими, индийскими коллегами; налажена и дистанционная приемка в контуре Росатома. Развитие этого направления — на контроле руководителя дивизиона. Будут упрощены процедуры взаимодействия с представителями монтажных, ремонтных, эксплуатирующих организаций: они получат доступ к сервису (инвентаризация, консультации, удаленная диагностика и т. д.), не дожидаясь приезда наших представителей.
В помощь, но не на замену
В какой мере наше производство станет «безлюдным» с развитием цифровой трансформации? Мы не берем офисные процессы, которые могут быть роботизированы с применением технологий RPA. В массовом представлении о роботизированном производстве сегодня — вид безлюдного сборочного конвейера, где корпус автомобиля «набивают» оборудованием механические манипуляторы. Понятно, что отличия крупносерийного автомобильного производства и энергетического атомного машиностроения огромны и картины полной автоматизации мы, по всей вероятности, не увидим никогда. Но у нас есть ряд процессов, которые можно роботизировать. Сравнительно простой пример — тестирование на площадке «Петрозаводскмаша» так называемых коботов, «коллаборейшн роботов», которые дополняют человека и позволяют снять часть несложных операций. На участке мехобработки мы роботизировали погрузку и разгрузку заготовки, избавив квалифицированного оператора от тяжелой физической работы, ранее неотъемлемой части его труда. Однако много операций по сборке сложных изделий сегодня далеки от автоматизации. Так, на сборке коллекторов для теплоэнергетики сейчас много ручного труда, в котором задействованы десятки рабочих. Роботизация таких процессов должна быть связана с изменением технологических процессов, например с внедрением автоматической сварки, за которой не потребуется дорабатывать вручную.
Есть другие примеры: парогенератор содержит огромное количество труб; в настоящее время они визуально контролируются на предмет отсутствия дефектов. Мы предполагаем, что большой выигрыш в скорости проведения процедуры контроля даст использование машинного зрения, и готовим такой проект с коллегами в Волгодонске. Если проект оправдает себя, мы сможем автоматизировать операции, которые занимают в пересчете на изделие сотни человеко-часов. Также большие перспективы имеет замена машинным зрением процедур оценки рентгеновских снимков, ультразвуковых изображений и иных технологий неразрушающего контроля для изделий: этот проект, значимый в масштабе отрасли и с хорошим рыночным потенциалом, мы прорабатываем с ЧУ «Цифрум». Другое направление по достижению малолюдности на производстве — это обеспечение дистанционного контроля за работой станков с ЧПУ. В частности, интересен опыт АО «ЦКБМ»: оператор может обслуживать одновременно два и более (до пяти) станков; загрузив заготовку и запустив процесс обработки, он может дистанционно наблюдать за параметрами (в ключевых точках технологического процесса) на нескольких станках.
Добавим, что использование машинного зрения и искусственного интеллекта позволяет улучшить контроль соблюдения правил техники безопасности. Так, с помощью видеонаблюдения можно автоматически контролировать использование работниками средств индивидуальной защиты: каски или каскетки, защитных очков, перчаток и т. д. В настоящее время идет проработка функции, позволяющей персонально идентифицировать работника, допустившего нарушение, с уведомлением через смс. Другая система — отслеживание передвижения работников внутри цехов с помощью датчиков на касках, в том числе контроль захода в опасные или закрытые зоны. Пилотный проект реализован на площадках АО «АЭМ-технологии», планируется тираж решений на другие предприятия. Это позволит реализовывать сценарии вплоть до ограничений работы оборудования: если в опасной зоне обнаружен человек без допуска, оборудование может быть остановлено, установка обесточена и т. д. Подобные решения позволят, в частности, улучшить технику безопасности при проведении крановых работ, работу со стендовым оборудованием.
Импорт замещаем, а время не теряем
Для импортозамещения в нашем распоряжении есть российские решения, которые в целом удовлетворяют наши потребности. Так, платформа 1С позволяет разрабатывать практически весь спектр приложений для учета и планирования. Имеются и отечественные платформы для нужд конструирования и расчетов, но цифровизация и особенно импортозамещение в этом виде деятельности сложнее. Сегодня для замены зарубежных решений для проектно-конструкторской деятельности рассматриваются и внедряются отечественные системы, выполнение этой задачи контролируется на уровне высшего руководства отрасли. Наша задача — достижение к 2024 году технологической независимости от зарубежных средств проектирования, конструирования, расчетов. Лишь часть наших предприятий изначально опиралась на импортонезависимое решение наших белорусских партнеров Intermech Professional Solutions. Но значительная группа наших предприятий работает в зарубежных системах Autodesk, Siemens, PTC Inc. Мы тестируем некоторые из отечественных решений для замены импортных пакетов, и одна из сложностей — отставание российских разработок в поддержке 3D-проектирования. Есть и ограничения по поддержке крупных, масштабных моделей. Обычное для нас изделие, содержащее несколько сотен тысяч компонентов, обрабатывается в системах зарубежной разработки заметно быстрее. Тем не менее, ОКБМ им. Африкантова уже разрабатывает проект оптимизированного плавучего энергоблока в российской системе 3D-проектирования, поэтому сложности преодолимы.
Еще одно преимущество зарубежных систем конструирования — возможность конвертировать элементы, разработанные в 3D-модели, в инструкции для станков с ЧПУ. Фактически создана экосистема, позволяющая «бесшовно» и в сжатый срок проводить изделие от идеи до станка. Российских решений, способных на подобную интеграцию, нет; мы имеем дело с отдельными приложениями, данные нужно дорабатывать: в этом смысле мы располагаем лишь решениями, аналогичными мировому уровню 10–20-летней давности. Следует отметить, что свою экосистему наши зарубежные партнеры выстраивали через поглощение компаний, создававших те или иные элементы необходимого цикла, и эти элементы были интегрированы в единую разработку. По всей видимости, на российском рынке в среде IT-компаний должна произойти аналогичная работа, которая займет определенное время. При этом наша задача удержания технологического лидерства не отменяется — будем надеяться, что процессы создания отечественных средств конструирования пройдут быстрее, чем это происходило за рубежом. Также актуальная зона для развития — создание российских станков с ЧПУ; на рынке пока доминирует зарубежная техника.
Для прочностных расчетов наши конструкторы используют американский комплекс Ansys, но планируется его полное замещение на программный комплекс «ЛОГОС» разработки РФЯЦ-ВНИИЭФ; этот пакет используют уже на многих наших предприятиях. Для расчетов по теплообмену, прочностным расчетам и иным аспектам мы взаимодействуем с коллективом РФЯЦ-ВНИИЭФ, который корректирует и дорабатывает «ЛОГОС». Мы ожидаем, что на этой основе будет создана экосистема программ для выполнения расчетов, обмена данными, их выгрузки в наши конструкторско-технологические системы и в цифрового двойника.
Задачи по импортозамещению подталкивают нас к разработке собственных инструментов, и возможная перспектива этой работы — коммерциализация в формате цифровых продуктов. Так, разработка ОКБМ им. Африкантова КРИС и КРИС-монитор — цифровые продукты для оценки рисков, с моделированием вероятности отклонений в работе. Этот продукт используется на российских АЭС, мы планируем адаптировать и продвигать эту задачу для инозаказчиков и инфраструктурных объектов. Другой цифровой продукт — IVM-Электро, пакет, позволяющий моделировать работу электродвигателя. Есть планы по цифровой упаковке нашей системы мониторинга производственного оборудования (СМПО); на первом этапе она может быть предложена в отрасли, затем — и на внешних рынках. Хорошие перспективы мы видим и у проекта по «цифровому паспорту» ГЦНА, вместе с сервисной услугой