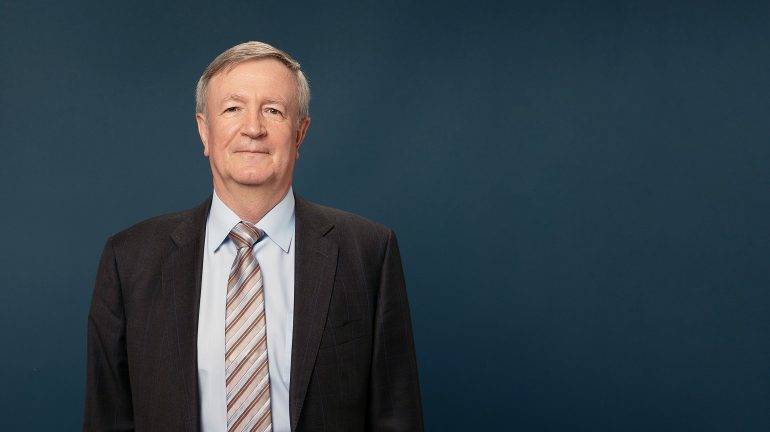
Зона широких возможностей
Перспективы производства и применения широкозонных полупроводников
Относительно новое и очень многообещающее направление в электронике — применение широкозонных полупроводников, отличающихся особым сочетанием электрофизических свойств, что ведет к качественному улучшению характеристик приборов на их основе. Виктор Федосеев, главный научный сотрудник АО «НИИ НПО «Луч», кандидат технических наук рассказывает об особенностях и возможностях этих материалов, а также о технологиях, необходимых для их производства.
Три поколения материалов
Типы полупроводниковых приборов
Дискретные приборы:
диоды
транзисторы
тиристоры
Силовые модули
Оптические приборы:
светодиоды
лазерные диоды
приемники-передатчики
фотодетекторы
Сенсоры
Интегральные схемы:
микропроцессоры
память
логические схемы
аналоговые схемы
Справка
Электроника — это крупнейшая отрасль мировой экономики, объем которой в 2022 году составил 1,5 трлн долларов США. В основе современной электроники лежат полупроводниковые материалы, первыми из которых были германий и кремний. Затем появились составные полупроводники из двух-трех элементов: арсенид индия-галлия, антимонид индия, теллурид кадмия и др. К третьему поколению материалов относятся так называемые широкозонные полупроводники с шириной запрещенной зоны более 3 эВ, например карбид кремния, нитрид галлия, оксид олова, сульфид или оксид цинка. Однако в настоящее время промышленным потенциалом обладают только первые два материала из этого списка.
Горизонты возможностей
Из полупроводников изготавливаются дискретные диоды и транзисторы, создаются интегральные микросхемы и собираются силовые модули. Ни одно предприятие госкорпорации «Росатом» не обходится без применения электроники, а некоторые из них выступают на отечественном рынке как крупные разработчики. Среди новых направлений разработок в области силовой электроники в госкорпорации следует отметить электротранспорт (в частности, участие в создании электромобиля «Атом»), электрозарядные станции, ветро- и солнечную энергетику, где применение широкозонных полупроводников является весьма перспективным.
Сферы применения различных материалов микроэлектроники проиллюстрированы на рисунке 1. Традиционные дискретные приборы на основе кремния работают при умеренных частотах и мощностях. Напряжение пробоя для них обычно не превышает 650 В. Карбид кремния применяют в мощных электронных преобразователях, в частности при напряжениях 1700 В и выше.
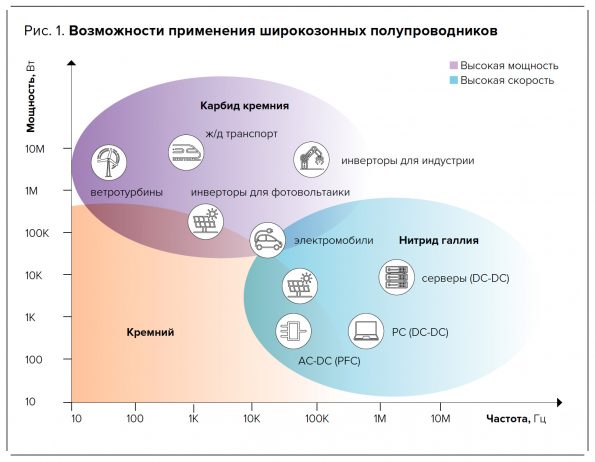
Приборы из нитрида галлия предназначены главным образом для высокочастотных устройств, например для работы в сетях мобильной связи 5G. Согласно журналу Compound Semiconductor (2022. Vol. 28, iss. 4. P. 43), нитрид галлия на подложке из карбида кремния является практически единственным вариантом создания мощной электроники на частотах свыше 6 ГГц. Транзисторы из кремния LDMOS, арсенида галлия, сплава кремний-германий и нитрида галлия на кремниевой подложке существенно уступают нитриду галлия на подложке из карбида кремния по мощности и (или) по частоте (рис. 2).
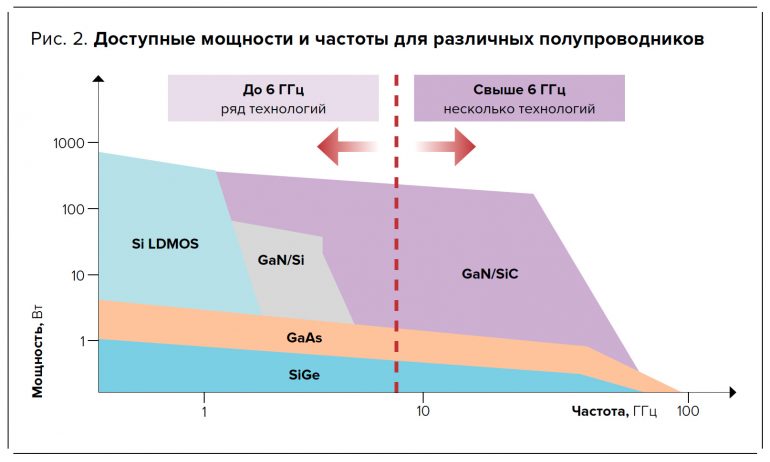
Ширина запрещенной зоны определяет способность полупроводника работать при высоких напряжениях, токах, частотах и температурах. Среди других особенностей карбида кремния — значительная величина электрического поля пробоя и высокая теплопроводность. В конечном счете эти свойства позволяют сделать электронные приборы более компактными и легкими, снизить потери, обеспечить работу при более высоких токах, напряжениях, мощностях, частотах, температурах и в неблагоприятных внешних условиях, а также упростить систему охлаждения. Например, применение карбида кремния (SiC) в электромобилях Tesla Model 3 позволило увеличить длину пробега от батареи на 10%, а при использовании блоков питания на основе нитрида галлия (GaN) фирмы Navitas втрое снизилось время зарядки и вдвое — объем зарядного устройства.
Таким образом, уже сейчас силовая электроника нового поколения применяется в легковых электромобилях. Далее возможно применение в таких областях, как грузовой электротранспорт, оборудование для возобновляемой энергетики, линии электропередач, приводы электромоторов с переменной частотой вращения, информационно-коммуникационная техника, центры обработки данных, железнодорожный транспорт. В чуть более отдаленной перспективе появятся полностью электрические самолеты и морские суда. Согласно прогнозу Power SiC 2022 Report компании Yole Developpement, мировой рынок силовой электроники в период 2021–2027 годов будет расти с темпом 34% ежегодно (рис. 3).
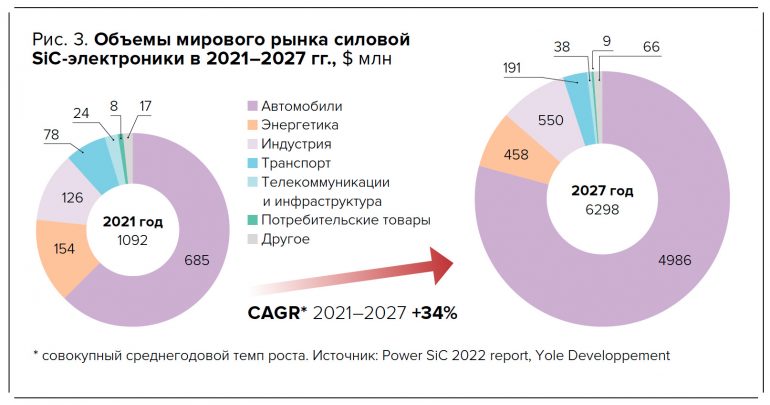
Что же мешает массовому внедрению широкозонных полупроводников? Прежде всего, это сложности технологии производства и, соответственно, высокая цена материалов. Безусловный мировой лидер в использовании карбида кремния и нитрида галлия для силовой электроники — США. Китай энергично пытается наверстать упущенное. Другие страны — Япония, Германия, Южная Корея — не обладают всем спектром технологий в этой области. Можно сказать, что наличие разработок в области широкозонных полупроводников является одним из показателей уровня научно-технологического развития страны.
Как это делается: от порошка до пластин
Рассмотрим цепочку производства электронных пластин из карбида кремния диаметром 150 мм. Дальнейшие переделы, связанные с формированием электронных транзисторов и микросхем, — нанесение фоторезиста, литография, имплантация примесей, нанесение тонких пленок, пассивация, металлизация, нарезка чипов, корпусирование, сборка силовых модулей, инспекция и метрология — во многом аналогичны уже имеющимся для кремниевых фабрик. Более того, рассматриваются варианты модернизации устаревших фабрик для кремниевых пластин диаметром 150 мм с целью перехода на пластины из карбида кремния.
Этап 1: исключительно чисто
Начинается все с производства ультрачистого порошка карбида кремния. Его чистота должна быть на уровне ~ 6N (то есть шесть девяток — 99,9999%). Соответственно, содержание примесей не должно превышать 1 ppm, или одну миллионную часть по весу. Гранулярный состав порошка должен быть субмиллиметрового диапазона.
Для получения абразивного карбида кремния с конца XIX века используется процесс Ачесона. При этом в большие печи засыпают смесь кварцевого песка, нефтяного кокса, древесных опилок, соли и нагревают с помощью графитового нагревателя до температуры примерно 2500 °C. По окончании процесса длительностью несколько суток кладку разбирают. Ближе к графитовому нагревателю получают более чистый (зеленый) карбид кремния. Примерно таким образом работает единственное в России предприятие по производству карбида кремния — Волжский абразивный завод.
Однако чистота такого продукта далека от электронного качества. Даже если использовать чистые кварц и порошок углерода, предел метода Ачесона по чистоте — 5N. Производства карбида кремния требуемой чистоты в России нет, и его нужно создавать. В лабораторных масштабах это относительно просто, но в промышленных, когда речь идет о тоннах продукции, — это непростая задача, к решению которой могло бы приступить АО «НИИ НПО «ЛУЧ».
Следует заметить, что попутно можно производить порошок карбида кремния для технической керамики с чистотой до 4N. Контроль порошка осуществляют по чистоте, содержанию примесей отдельных элементов, гранулярному составу и форме частиц порошка, а также фазовому составу.
Этап 2: вырастить правильный кристалл
Следующий этап — выращивание монокристаллов карбида кремния. Это возможно несколькими способами, но основным промышленным методом, ставшим мировым стандартом де-факто, является физический транспорт паров PVT (Physical Vapor Transport). Проблема в том, что при относительно невысоких температурах и давлениях карбид кремния не плавится. Поэтому методы роста кристалла из расплава типа метода Степанова здесь неприменимы. Выход был найден в 1978 году советскими учеными Ю. М. Таировым и В. Ф. Цветковым из Ленинградского электротехнического института (ЛЭТИ), которые, собственно, и разработали метод роста PVT на пластине-затравке. В этом процессе происходит сублимация порошка карбида кремния в виде паров Si2C, SiC2 и их конденсация-кристаллизация на затравке при температуре 2200–2400 °С в среде чистого аргона. Порошок засыпается в графитовый тигель, окруженный графитовой изоляцией. Вакуумная камера выполняется в виде кварцевой или металлической трубы. Нагрев производят с помощью индуктора или графитового нагревателя.
Градация порошков карбида кремния по качеству
— абразивы
— огнеупоры
— металлургического качества
— техническая керамика
— электронного качества
Справка
Появляется еще одна проблема — получение чистого (желательно изостатического) графита с зольностью на уровне 5 ppm, а также производство изделий из него — тиглей, нагревателей, войлочных изоляторов. Однако в госкорпорации «Росатом» есть специализированные организации, которым по силам эта задача. В целом в России разработаны и изготавливаются установки для роста кристаллов карбида кремния по методу PVT диаметром до 150 мм. Длина выращенной були (в западной литературе часто используется термин puck — «шайба») относительно небольшая — 15–50 мм.
Карбид кремния имеет свыше 200 политипов или кристаллических форм: с кубической, гексагональной, ромбической кристаллическими решетками. Для электроники наиболее подходящим политипом является 4H-SiC. Выращивание требуемого политипа достигается подбором поля температур и давления аргона применительно к конкретному порошку. После завершения роста требуется проведение контроля (характеризации) для определения уровня дефектов в кристаллической решетке.
Этап 3: обработать без потерь
Выращенная буля определенным образом ориентируется относительно кристаллографических осей и обрабатывается с получением цилиндрического слитка. С учетом исключительной твердости карбида кремния шлифовка осуществляется суспензией на основе алмазных порошков. При разделке слитка на подложки толщиной около 0,4 мм важно обеспечить минимальные потери материала. Поэтому разделка (slicing) ведется на многопроволочных станках. Применяется алмазированная проволока диаметром около 0,2 мм. Весь слиток разделывается на подложки за один раз, но процесс резки может занимать от 10 часов до нескольких суток. В России пока нет своих станков для многопроволочной резки. Однако Минпромторг РФ разработал техническое задание на такой станок, и есть надежда на появление соответствующей техники.
После разделки подложки шлифуются и полируются методами CMP (Chemical Mechanical Polishing — химико-механическая полировка) для получения пластин с заданными геометрическими размерами и шероховатостью. Помимо контроля геометрии осуществляется контроль количества дислокаций, микропор, макродефектов и политипной однородности. Методы контроля, например рентгеноструктурный анализ, весьма непросты и представляют собой сложную методическую и метрологическую задачу.
Этап 4: с микронной точностью
Последней из рассматриваемых операций является эпитаксия, под которой подразумевается выращивание тонкой кристаллической пленки поверх пластины из кристалла карбида кремния. Толщина пленки — от нескольких микрон до нескольких десятков микрон. В данном случае возможна гомоэпитаксия с нанесением карбида кремния или гетероэпитаксия с нанесением нитрида алюминия-галлия. Эпитаксия дает возможность нанести слой (слои) с требуемым типом проводимости или концентрацией носителей заряда, а также снизить число дефектов по сравнению с пластиной.
Основным методом для гомоэпитаксии в данном случае является высокотемпературное химическое осаждение из газовой фазы HTCVD (High Temperature Chemical Vapor Deposition), а для гетероэпитаксии — МОС-гидридная эпитаксия MOCVD (Metal Organic Chemical Vapor Deposition). В этих процессах применяются чистые газовые прекурсоры, например трихлорсилан SiHCl3 и пропан C3H8, легирующие газы и газы-носители — водород, аргон. Пластины размещаются на графитовом подложкодержателе с CVD-покрытием из карбида тантала или карбида кремния. Отечественных эпитаксиальных установок пока нет, но в нескольких организациях в Зеленограде накоплен определенный опыт эксплуатации западной техники. Имеются предпосылки к тому, что отечественные эпитаксиальные установки все-таки появятся.
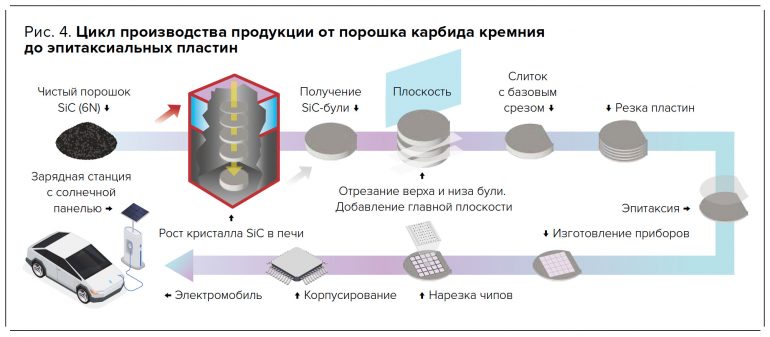
К технологической независимости
Согласно отчету американского министерства энергетики Critical Materials Assessment за 2023 год, доля кремния и карбида кремния в электронике в 2022 году составила 96% и 3% соответственно. Прогнозируемые цифры на 2028 год (80% и 17%) означают шестикратный рост доли карбида кремния.
На предприятиях госкорпорации «Росатом» за долгие годы заложен достаточно прочный фундамент по многим технологиям, необходимым для развития силовой электроники на основе карбида кремния в России. В частности, участие научного блока Росатома в таком проекте дало бы, помимо прямого эффекта в виде создания продуктовой линейки диодов, транзисторов, силовых модулей и других электронных изделий, качественный технологический скачок для отечественных продуктов более высокого передела. К примеру, это относится к чистым и высокотемпературным материалам, технологиям роста кристаллов и эпитаксии, метрологии и измерениям, к получению и очистке электронных газов, созданию изостатического графита, формированию CVD-покрытий и расчетным методам термодинамики (кинетики) реакции для сублимационного роста кристаллов, а также к компьютерному моделированию полупроводниковых гетероструктур класса TCAD (Technology Computer-Aided Design).