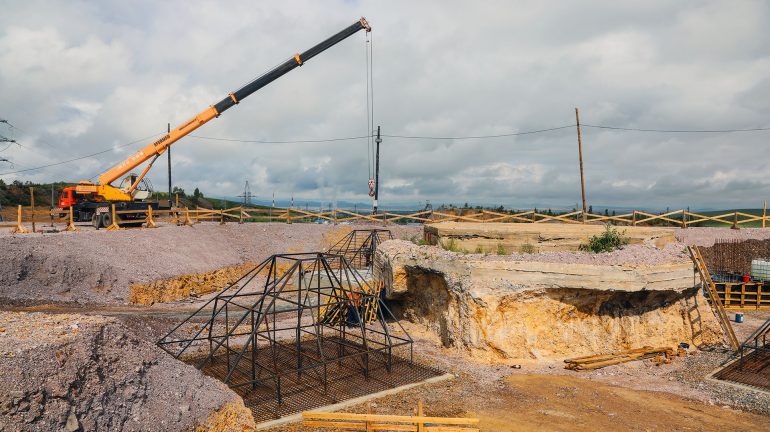
Добыча по максимуму
Предложения для максимального извлечения запасов урана
Задачи, которые решает Горнорудный дивизион «Росатома» (холдинг «Росатом Недра»), — максимизация извлечения полезного компонента на действующих урановых рудниках и на месторождениях Эльконского урановорудного района вкупе со снижением капитальных и операционных затрат. Для этого, в частности, планируют задействовать кучное выщелачивание и локальные сорбционные установки.
Кучное выщелачивание на ППГХО
Месторождения Стрельцовского рудного поля, которые в настоящее время отрабатывает Приаргунское производственное горно-химическое объединение (ППГХО) и запасы которых в обозримом будущем истощатся, сложены алюмосиликатными рудами. Руды с более высокими содержаниями урана перерабатывают на гидрометаллургическом заводе (ГМЗ), с более низкими — методом кучного выщелачивания, или, на горняцком сленге, на куче.
Рудник № 6 будет отрабатывать месторождения, сложенные карбонатными рудами, которые отличаются по свойствам от алюмосиликатных, поэтому для них построят новый ГМЗ. С учетом всех этих вводных ППГХО изучает возможность перейти на переработку оставшихся алюмосиликатных руд только на куче.
Кучное выщелачивание применяется на ППГХО с 1974 года для забалансовых (с параметрами, хуже балансовых, чья отработка экономически целесообразна) руд и с 1996 года — для бедных. Главное преимущество этого метода — более низкая, чем у гидрометаллургического, себестоимость. Недостатки — низкие скорость технологического процесса (один штабель перерабатывается порядка 2,5–3 лет) и извлечение (около 30% для забалансовых руд и не более 65% для бедных).
Как рассказал на VI международном симпозиуме «Уран: геология, ресурсы, производство» директор по науке, технологическому и инновационному развитию ППГХО Александр Морозов, чтобы улучшить технологические и экономические параметры извлечения урана на куче, специалисты ППГХО провели исследования по двум направлениям — для забалансовых и бедных руд.
Благодаря им выяснилось, что под влиянием естественных атмосферных процессов куски руды рассыпаются, уран переходит в мелкую фракцию и перемещается в нижнюю часть штабеля на складе забалансовых руд, так что в выдержанных (стоящих не первый год) штабелях можно извлекать порядка 85–90% металла. Чтобы отделить самые ценные компоненты, перед укладкой штабеля на кучу запустили рудосортировочный комплекс. Благодаря сортировке извлечение выросло с 30 до 70%. Также стали добавлять поверхностно-активные вещества, которые снижают натяжение жидкости, позволяя реагенту глубже проникать в рудные куски, и мешают глинистым частицам (они препятствуют выщелачиванию) загрязнять рудный материал.
Для снижения себестоимости в качестве реагента для закисления кучи использовали отработанные кислые растворы ГМЗ и отработанную серную кислоту одного из сибирских производителей сорбентов. Это позволило в десятки раз снизить расходы на реагенты.
К настоящему времени из 7,5 млн тонн забалансовых руд переработано 4,5 млн тонн, из них произведено 400 тонн урана с себестоимостью ниже, чем по гидрометаллургической технологии, в 2–2,5 раза. Совокупная выгода составила более 1,3 млрд рублей.
Для бедных руд проблема — более высокая плотность руд, из-за чего растворы не могут проникнуть вглубь и растворить уран. Как рассказал Александр Морозов, за год-полтора серная кислота проникает в кусок на глубину не более чем на 5–7 мм. Чтобы решить проблему, попробовали додрабливание и селекцию рудной массы с помощью рентгенорадиометрической установки на ГМЗ. После сортировки наиболее богатая фракция отправлялась на завод, пустая порода — в отвал, остальное — на кучу. Эти меры вкупе с использованием растворов ГМЗ и переводом транспортировки руды с автотранспорта на конвейеры позволили увеличить извлечение со средних 60 до 85–90%, а срок переработки штабеля с 2,5 лет до 1 года.
После выхода на полную проектную мощность рудника № 6 на кучу можно будет отправлять порядка 500–600 тыс. тонн руды в год и получать порядка 300 тонн урана в год. Это предпочтительный вариант переработки оставшихся алюмосиликатных руд, потому что действующий ГМЗ уже состарился, а его модернизация не имеет экономического смысла. Отказ от гидрометаллургии означает необходимость решить проблему очистки отработанной серной кислоты от примесей и отделить мелкую фракцию от других, перерабатывая ее в отдельных штабелях. Мелкая фракция разрушает тело штабеля и вызывает эффект кольматации (заиливания), поэтому необходимо ее агломерировать, и это следующая задача, которую предстоит решить. По оценкам, переход к кучному выщелачиванию позволит снизить себестоимость выпуска концентрата урана примерно в полтора раза.
Новый гидрометаллургический завод для карбонатных руд в настоящее время проектируется. Предполагается, что проект будет завершен и получит все разрешения в 2027 году, в 2028 году начнется строительство.
Кучное выщелачивание на Эльконе
Эльконский горно-металлургический комбинат (ЭГМК) начал отработку руд месторождения Северное кучным выщелачиванием. Но в штабелях вместе с золотом содержится и уран, оставлять который в штабеле нерационально. Как рассказал на симпозиуме начальник отдела технологий и оборудования ЭГМК Василий Кольцов, проведенный опыт показал, что извлекать уран после выщелачивания золота можно, поэтому специалисты ЭГМК, АО «ВНИПИпромтехнологии», Российского химико-технологического университета им. Д. И. Менделеева и Всероссийского института минерального сырья им. Н. М. Федоровского выполнили НИОКР по разработке технологии поэтапного кучного выщелачивания золота и урана из эльконских окисленных карбонатных руд бесцианидными реагентами. Технология предполагает, что уран будет извлекаться на тех же штабелях, что и золото, одновременно будет происходить доизвлечение золота.
Специалисты изучили руды, реагенты, выбрали из них самые эффективные, подобрали технологический регламент и провели испытания, которые показали возможность выщелачивания урана по карбонатной, то есть щелочной, а не кислотной, как обычно, схеме. Сравнив зарубежные и российские реагенты, специалисты пришли к выводу, что отечественные, скомпонованные на основе смеси карбонатов, бикарбонатов и перкарбонатов натрия, лучше зарубежных, так как при дальнейшей переработке показатели сорбции урана вшестеро выше. Кроме того, стабильность поставок российских реагентов выше.
Исследования показали, что коэффициент извлечения урана кучным выщелачиванием составил 65–70%, золота — 90%. Технологическая схема выщелачивания и сорбции предполагает замкнутый водооборот, что важно для экологической приемлемости проекта. Следующий этап — провести укрупненные испытания в циклических режимах.
Мобильные сорбционные установки
Предназначение мобильных сорбционных установок (МСУ) — отработка небольших залежей, где стационарные установки использовать нерентабельно из-за высоких капитальных расходов.
Изначально их разработали для извлечения скандия, который вместе с ураном содержится в рудах месторождений «Далура», затем идею решили применить для урана. В 2022 году специалисты «Далура» и «Русбурмаша» (инфраструктурная компания, входит в «Росатом Недра») разработали МСУ для урановых залежей «Хиагды». В 2023 году ее ввели в опытную эксплуатацию, и она стала стабильно извлекать уран: из продуктивных растворов он осаждается на ионообменную смолу, которую перерабатывают на центральной площадке.
МСУ состоит из модулей-контейнеров с сэндвич-панелями и теплоизоляцией. В контейнерах установлены мобильные сорбционные колонны, резервуары для свежего сорбента, продуктивных и возвратных растворов и серной кислоты и передвижная компрессорная установка. В комплект также входят контейнеры для электротехнического оборудования и операторов.
МСУ не нужны заглубленные фундаменты, поэтому их просто и недорого проектировать, согласовывать, устанавливать на площадке из бетонных плит на щебеночной подушке и демонтировать, а также рекультивировать территорию после завершения отработки. Конструкция простая и надежная: срок службы основного оборудования — 20 лет, модули оснащены освещением, отоплением, вентиляцией и автоматикой. Изготавливает, поставляет, выполняет шефмонтаж и пусконаладку и сдает объект одна организация, поэтому организационные неувязки тоже сведены к минимуму.
Продолжение концепции — мобильная сорбционно-десорбционная установка (МСДУ). Она понадобилась для одного из месторождений «Далура». Извлеченные продуктивные растворы отличаются высокой коррозионной активностью, поэтому их лучше перерабатывать отдельно от остальных. МСДУ уже разработана, идет подготовка площадки, летом начнутся строительно-монтажные работы.
МСДУ будет выпускать не насыщенную ионообменную смолу, как МСУ, а продукт следующего передела — товарный десорбат. Для МСДУ планируют использовать U-образные колонны и размещать не в отдельных модулях, а в утепленном облегченными материалами общем корпусе. Если первый пример окажется успешным, МСДУ будут использовать для отработки и следующих по очереди месторождений, не тратя ресурсы на капитальное строительство, а на стационарное предприятие привозить только товарный десорбат для сгущения, фильтрации и сушки.
Автомобильная сорбционная установка
На симпозиуме главный эксперт «Гиредмета» Валерий Головко предложил собрать МСУ на платформе грузовых автомобилей, установив сорбционные колонны в наклонном положении на прицепе. Это нетипично, обычно их устанавливают вертикально. Чтобы подтвердить реализуемость идеи, Валерий Головко и его команда провели лабораторные и опытно-промышленные работы, разработали технологию, определив технологические параметры, уточнив конструкционные особенности и получив данные о технологическом процессе.