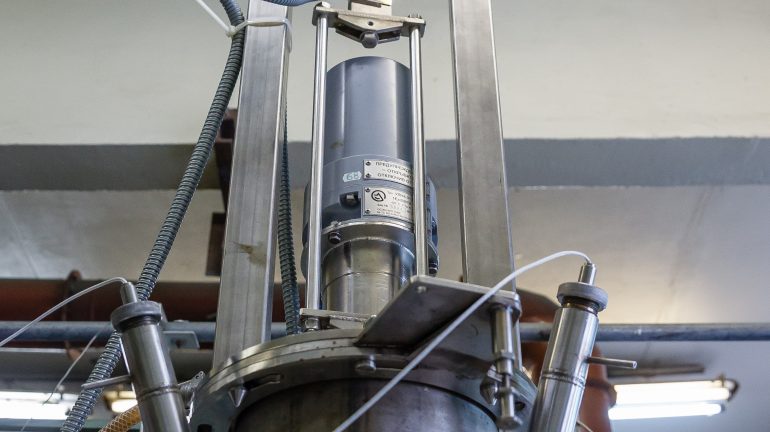
Легенда о тигле
Так получилось абсолютно случайно: в процессе подготовки статьи про остекловывание ВАО нам повстречался специалист удивительной судьбы. Он более 40 лет проработал во ВНИИНМ, занимал должность ведущего научного сотрудника, был участником ликвидации аварии на Чернобыльской АЭС, а позже стал лауреатом Государственной премии, присуждённой за разработку технологии и оборудования остекловывания жидких активных отходов на ПО «Маяк». Сегодня в нашей удивительно тёплой рубрике «Секреты величия» свой трудовой путь вспоминает Георг Борисов.
Вся моя творческая и трудовая деятельность неразрывно связана с ВНИИНМ. Я дважды уходил из ВНИИНМ и возвращался. Даже после ухода на пенсию в 2006 году я работал до 2011 года в должности генерального директора некоммерческой организации «Ассоциация технологии и материалы атомной науки и техники», расположенной на территории ВНИИНМ. Я учился в школе, в подмосковном городке Дзержинский, по окончании которой в 1953 году поступил в Московский институт цветных металлов и золота. Учащимся этого вуза выдавали красивую форму, и этот фактор стал решающим при выборе места учёбы, ведь я был ещё мальчишкой! Но по иронии судьбы в этом же году форму для студентов нашего факультета отменили.
После окончания института меня распределили в Подольск, но так как я жил в Дзержинском, то добираться до Подольска было крайне неудобно. Я объяснил эту ситуацию, и меня отпустили в «свободное плавание». Вот тогда я и пришёл устраиваться в НИИ-9 (будущий ВНИИНМ). В институте я изучал английский язык, память у меня была хорошая, я запоминал много слов, и, чтобы не тратить впустую 1,5 месяца, которые отводились на проверку перед принятием в НИИ-9, я начал посещать институт иностранной литературы, где читал журналы по моей специальности на английском языке. И через какое-то время я вдруг заметил, что начал думать на английском!
Я начал работать по тритиевой тематике в отделе Зинаиды Ершовой на установке У-14. Через два года я перешёл в только что созданную лабораторию, которая занималась разработкой пирохимического процесса регенерации отработавших твэлов с целью извлечения урана и плутония. В институте существовала также другая, более отработанная технология – экстракционная, созданная под руководством бывшего директора института Виктора Шевченко. Я помню, как мы, молодые специалисты, во главе с научным руководителем несколько раз ходили на заседания учёного совета докладывать о результатах работы. В то время мы считали, что пирохимическая технология по сравнению с экстракционной позволит решить большинство экологических проблем, так как при пирохимии не возникает больших объёмов жидких отходов. Я занимался первой стадией новой технологии, а именно – вскрытием твэлов. Было очень интересно, и работа нравилась. Однако после смерти моего научного руководителя я решил поступить в аспирантуру на кафедру металлургии радиоактивных металлов МИСиС. Тогда этот институт в шутку называли «институтом марксизма-ленинизма с металлургическим уклоном», так как было очень трудно сдать вступительный экзамен в аспирантуру по истории КПСС.
В 1966 году я успешно защитил кандидатскую диссертацию и снова вернулся во ВНИИНМ в лабораторию пирохимической регенерации твэлов. Был назначен руководителем группы по разработке и проверке в укрупнённом масштабе термического вскрытия сборок твэлов от реакторов БН-350 и ВВЭР-440. За девять лет наша группа совместно с московским НИИХИММАШ разработала два варианта аппаратурного оформления процесса термического вскрытия твэлов. Первый на стенде ВНИИНМ, расположенном под кабинетом Бочвара. Там была смонтирована пилотная установка на основе индукционной вакуумной печи, в корпусе которой размещён поворотный тигель из огнеупора. В тигле осуществлялся процесс вскрытия путём сплавления стальных оболочек с добавкой чугуна и отделения полученного расплава от топлива при повороте тигля. Второй вариант запустили на заводе в Электростали по производству твэлов. Там была смонтирована установка бестигельного типа «ОГ» (оплавитель-гранулятор), выполненная в виде вертикальной стальной трубы, в верхней части которой расположен внутренний кольцевой жаростойкий нагреватель и высокочастотный индуктор. В нижней части трубы размещалась ёмкость с водой. Сборка твэлов БН-350, проходя через нагреватель, оплавлялась, и продукты вскрытия падали в ёмкость.
Испытания указанных аппаратов и отработка процессов показали, что наиболее работоспособным является вскрытие сборок БН-350 в поворотном тигле; термическое вскрытие сборок твэлов ВВЭР-440 практически нецелесообразно из-за реакции восстановления двуокиси урана цирконием уже при температуре 1200 градусов – температура сплавления циркония с медью. Мы поняли, что способ термического вскрытия твэлов неконкурентоспособен по сравнению с универсальной технологией механической рубки твэлов, заложенной в схему экстракционной регенерации отработавшего топлива на заводе РТ-1 ПО «Маяк».
Моим начальником был Георгий Новосёлов, у нас были прекрасные рабочие и человеческие отношения. И я ему предложил сменить тематику и отказаться от продолжения работы над технологией термического вскрытия. Новосёлов сначала меня отговаривал, предлагая продолжить исследования, но в итоге меня не поддержал, и я ушёл на другое предприятие. Но через год и два месяца снова вернулся во ВНИИНМ в лабораторию по обращению с радиоактивными отходами под руководством Веры Куличенко.
Я был назначен начальником группы. Лаборатория Куличенко с 60-х годов совместно с ПО «Маяк» занималась экологическими проблемами остекловывания ВАО. Работы вели в двух направлениях. Первое – остекловывание одностадийным методом в электростекловаренной печи. Этого направления придерживался ПО «Маяк», который в 1972 году выдал техническое задание на проектирование цеха остекловывания с электростекловаренной печью. Второе – двухстадийное остекловывание ВАО с использованием индукционных плавителей. В то время за рубежом эксплуатировались две подобные схемы. Куличенко поставила передо мной задачу усовершенствования процесса и основных конструкционных элементов в электростекловаренной печи, которая была наиболее продвинутым аппаратом. На стенде ВНИИНМ предлагалось создать малогабаритный плавитель типа ЭП для исследований и испытаний.
Помню наиболее яркие моменты по усовершенствованию процессов остекловывания. Это были разработки борофосфатного и ультрафосфатного стёкол и подбора перспективных высокостеклоустойчивых электродов из диоксида олова и кладки из хромцирконового огнеупора ХАЦ-30. Работы не заканчивались испытаниями, а доводились до разработки и изготовления конструкции электрода и испытания в опытной печи ЭПБС-100. Подбор высокостеклоустойчивых материалов был очень важен в связи с расширением номенклатуры перерабатываемых отходов, так как в них возрастало содержание таких коррозионноагрессивных примесей, как сульфат-ион и оксид железа.
Работа по процессу остекловывания отходов была прервана в мае 1986 года в связи с командировкой на ЧАЭС спустя неделю после аварии. Я был направлена в Чернобыль для проработки совместно с академиком Велиховым вопроса удержания расплава топлива вследствие аварийного расплавления топлива и прогара реактора. Удержание предполагалось с помощью бетонной водоохлаждаемой плиты, установленной под барботёром реактора. Исходя из нашего опыта, мы предлагали укладку на плиту фосфатного стекла, имеющего высокую степень растворения двуокиси урана. Кажется, 8 или 9 мая стало ясно, что проработка не потребуется, так как топливо в основном было выброшено в рабочие помещения и атмосферу. Остаток месяца я занимался дезактивацией территории вокруг 1–3-го блоков ЧАЭС и захоронением отходов в недостроенном хранилище 5-го блока станции.
В 1987 году я был назначен ответственным от института за пуск первой печи ЭП-500. Эксплуатация первой печи была очень тяжёлой из-за выхода из строя одного из водоохлаждаемых токоподводов электродов варочной зоны после тринадцати месяцев работы. Это была неудача. Для выхода из этого положения мы несколько раз собирали совещания специалистов по электроварке стекла из московских и ленинградского НИИ для анализа аварии и поиска вариантов решения. Основными причинами аварии оказались недостаточность охлаждения и несовершенство конструкции токоподвода электродов варочной зоны и схемы электропитания. Конструкция токоподвода была переделана, изменена схема его размещения. В схему охлаждения введено использование конденсата с непрерывным контролем его качества. Эти изменения были введены в конструкцию следующей электропечи ЭП500/1Р. Печь эксплуатировалась в цехе остекловывания 6 лет, что в два раза превышает проектный срок службы. Печь переработала больше 11 тысяч кубических метров ВАО с наработкой двух тонн фосфатного стекла с общей радиоактивностью 281,9 млн Кu. Остальные три печи ЭП-500 цеха остекловывания также работали со сроком службы выше проектного. В итоге на «Маяке» был создан цех остекловывания, в основе которого была заложена электростекловаренная печь ЭП-500 производительностью 500 литров жидких ВАО в час. За разработку и эксплуатацию технологии остекловывания жидких ВАО я в составе коллектива авторов в 1997 году был удостоен Государственной премии РФ в области науки и техники. Цех остекловывания жидких ВАО на ПО «Маяк» работает с 1988 года по сей день.