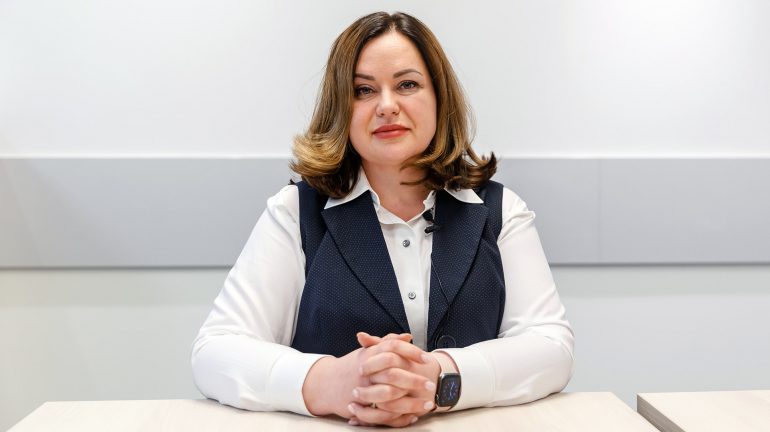
Материалы нового века
Как в Росатоме идет разработка новых технологических решений для развития наукоемких отраслей
То, что раньше казалось вымыслом писателей-фантастов, теперь стало реальностью: промышленные принтеры печатают сложные многосоставные изделия, с помощью цифровых технологий можно детально предсказать свойства еще не созданных материалов, ученые готовятся синтезировать новые элементы таблицы Менделеева. Для Росатома направление по разработке новых материалов программы «Развитие техники, технологий и научных исследований» (РТТН) — одно из приоритетных.
Директор проектов НИОКР по федеральному проекту «Разработка новых материалов и технологий для перспективных энергетических систем» (ФП‑4 РТТН) Татьяна Тихоновская рассказывает о целях работы и уже достигнутых результатах.
— Татьяна Александровна, расскажите об основных направлениях, которые включает в себя четвертый федеральный проект.
— Все проекты в составе РТТН дополняют друг друга. Наш проект также направлен на достижение целей других федеральных проектов. Этим объясняется и выбор основных направлений.
Первое направление — это разработка материалов, в первую очередь для нужд атомной энергетики, но также и для авиации, космоса и других стратегических отраслей.
Второе направление — разработка и демонстрация технологических решений для создания исследовательского жидкосолевого реактора (ИЖСР). Это сложный и амбициозный проект: пока ни в одной стране мира нет промышленно эксплуатирующихся реакторов этого типа.
Третье направление — разработка технологий, оборудования и изотопов для синтеза сверхтяжелых элементов.
И последнее, четвертое, направление — это изучение свойств вещества в экстремальных состояниях, например при сверхвысоких значениях давления и температуры. Это нужно в том числе для выполнения прикладных задач при разработке конструкционных материалов для атомной энергетики.
— Вы упомянули жидкосолевой реактор. Для чего нужна эта установка?
— Жидкосолевой реактор будет необходим на последней стадии замкнутого ядерного топливного цикла (ЗЯТЦ). Основная задача жидкосолевого реактора — дожигание минорных актинидов, что позволит отказаться от захоронения радиоактивных отходов (РАО) и таким образом решить проблему ядерного наследия. Топливом для активной зоны ИЖСР выступает расплавленная смесь из фтористых солей легких металлов и фторидов делящихся материалов, включая минорные актиниды, являющиеся высокоактивными отходами от переработки ОЯТ. Это сложная и малоосвоенная технология. Поэтому кроме новаторских конструкторских разработок потребуется и решение других серьезных научных задач: прежде всего разработка технологий контроля и управления окислительно-восстановительным потенциалом топливной соли при эксплуатации реактора и в ходе ее переработки, чтобы снизить коррозионную нагрузку на конструкционные материалы.
Отмечу, что разработкой ИЖСР занимается не только Россия, но и другие страны с развитой ядерной энергетикой. Специалисты рассматривают различные топливные системы, например французы — хлоридные, китайцы — фторидные, но готового промышленно освоенного решения пока нет ни у кого.
— А какие задачи ставятся перед Фабрикой сверхтяжелых элементов?
— Фабрика сверхтяжелых элементов — это глобальный проект фундаментальной науки. Он позволит ответить на вопрос о границе материального мира (масс ядер): 118-й элемент — сейчас последний в периодической таблице Менделеева, и ученым предстоит выяснить, могут ли существовать новые, еще более тяжелые элементы. Если удастся синтезировать 119-й и 120-й элементы, ученые смогут глубже изучить строение ядерной материи, моделировать процессы образования тяжелых элементов во Вселенной, прогнозировать их существование в природе и т. д.
Синтез 119-го элемента будет осуществляться в наиболее перспективной реакции берклий-249 + титан-50, а синтез 120-го элемента — в реакции калифорний-251 + титан-50. 119-й элемент станет первым элементом в восьмом периоде периодической системы химических элементов. Результаты будут исключительно важны для планирования экспериментов по синтезу более тяжелых элементов.
Для успешного проведения этих работ необходима глубокая модернизация имеющихся экспериментальных установок и создание Фабрики сверхтяжелых элементов. Для этого нужно будет изготовить уникальное оборудование. Это, во-первых, сильноточный инжектор многозарядных ионов на базе сверхпроводящего ионного источника электронно-циклотронного резонанса с частотой СВЧ-накачки 28 ГГц. Именно он увеличит чувствительность эксперимента в 50–100 раз. Во-вторых, в саровском РФЯЦ-ВНИИЭФ построят комплекс разделения изотопов трансурановых элементов на базе электромагнитного масс-сепаратора нового поколения. Такое оборудование позволит, например, нарабатывать калифорний-251 — редкий и дорогой материал. Наши коллеги в димитровградском ГНЦ НИИАР (входит в научный дивизион Росатома) разработают технологии получения и наработают изотопы трансплутониевых элементов — кюрия, берклия, а также изготовят из них мишени для проведения экспериментов по синтезу 119-го и 120-го элементов.
— Поделитесь, пожалуйста, основными результатами работы по всем четырем направлениям. Какими из них вы особенно гордитесь?
— Все поставленные на прошлый год задачи успешно выполнены. Отдельно хотелось бы отметить, во-первых, создание эскизного проекта ИЖСР. Он описывает облик всех основных систем будущего реактора. Это достаточно значимый шаг, далее следуют более детальные стадии разработки, включающие в себя, например, изготовление макетов отдельных систем, проведение экспериментов и т. д. Во-вторых, подобран коррозионно-стойкий материал, который будет использоваться в крупномасштабном жидкосолевом реакторе (он будет испытываться и для ИЖСР). Параметры этого материала по скорости коррозии не имеют аналогов в мире. В-третьих, разработаны материалы для перспективных реакторов ВВЭР.
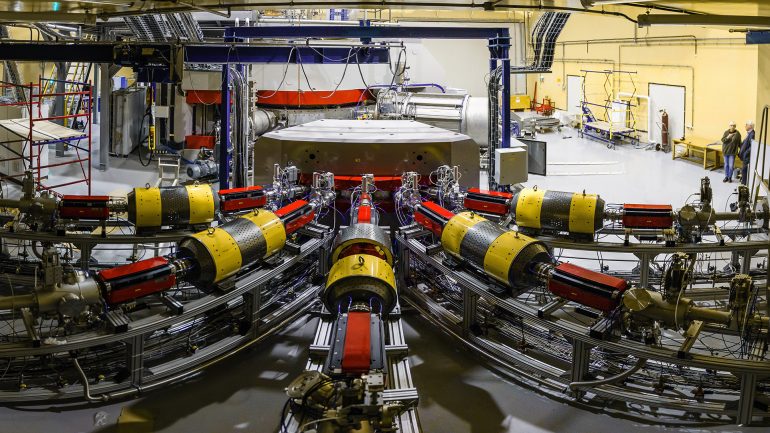
Кроме того, активно развивается аддитивное направление: создаются принтеры, способные работать с порошковыми и проволочными материалами и даже с монокристаллическими прутками тугоплавких металлов. Аналогов таких установок в России нет. В прошлом году специалисты НИИ НПО «ЛУЧ» изготовили крупные узлы такой установки. Задача этого года — запустить установку и напечатать на ней первые изделия, доказав эффективность этой технологии.
— Какие организации задействованы в ФП-4 РТТН?
— В выполнении проекта задействованы около 40 организаций. Это не только отраслевые компании (их 17), но и порядка 10 академических институтов, а также несколько вузов. Такая кооперация компетенций дает нужный синергетический эффект и позволяет выполнять все поставленные цели.
— Как повлияли новые геополитические реалии на выполнение целей федерального проекта?
— Мы провели масштабную работу, в результате которой смогли заменить импортные критически важные компоненты и материалы на отечественные. Как говорится, нет худа без добра: наша промышленность собралась и смогла изготовить вполне конкурентоспособные аналоги.
— Программа РТТН изначально была рассчитана до 2024 года, затем ее продлили до 2030-го. Какие значимые результаты должны быть достигнуты по ФП-4 в следующем году?
— Действительно, в 2024 году мы подводим промежуточные итоги. Прежде всего, будут подобраны конструкционные топливные материалы для активной зоны новых реакторов, в том числе для быстрых натриевых и свинцовых реакторов.
Также мы ожидаем большой прорыв по направлению аддитивных технологий. Продемонстрируем линейку из восьми установок, некоторые из них не имеют аналогов в мире. Наша гордость — высокотемпературный принтер, работающий по технологии селективного лазерного плавления, который будет работать при температурах свыше 800 °C.
Кроме того, планируем подготовить обоснование инвестиций по исследовательскому жидкосолевому реактору, оценить его воздействие на окружающую среду. Это позволит нам двигаться в сторону получения лицензии на размещение объекта.
По направлению синтеза сверхтяжелых элементов намерены полностью разработать всю инфраструктуру и технологии для Фабрики сверхтяжелых элементов, чтобы в 2025–2030 годах приступить непосредственно к синтезу.
Направления ФП-4 в деталях
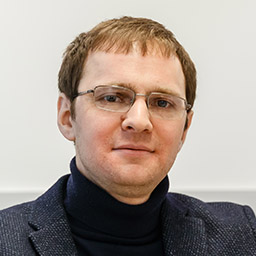
Новые материалы
Иван Сафонов
Руководитель направления по разработке новых материалов
— Направление по разработке материалов является самым объемным — сейчас это 16 НИОКР. Одна из ключевых областей — металлические материалы. Серия проектов посвящена разработке корпусных реакторных материалов для технологии ВВЭР, в частности для ВВЭР-С (со спектральным регулированием) и ВВЭР-СКД (со сверхкритическим давлением). В 2022 году по этим работам удалось перейти от лабораторных плавок к промышленным ступенчатым поковкам — изделиям с переменной толщиной металла и весом около 10 тонн. В этом году ставится задача по отработке технологии сварки этих толщин и постановке на аттестационные испытания основного материала и материала сварного шва, полученного промышленным способом.
Еще одно «металлическое» направление НИОКР — разработка и обоснование применения новой марки стали аустенитного класса с повышенными прочностными свойствами для энергетических установок малой мощности. Смысл проекта в том, чтобы максимально уменьшить массогабаритные характеристики оборудования вокруг реакторной установки и тем самым получить выигрыш в массе — этот параметр весьма критичен для АСММ. В 2022 году удалось выйти на изготовление промышленного полуфабриката. В 2023 году начинаются аттестационные испытания по всему комплексу свойств новой стали.
Помимо металлических материалов, активно развивается и направление композитов. Яркий проект — это разработка технологии получения сверхвысокопрочного углеродного волокна для специальных применений, например для крыла самолета МС-21 или для ответственных изделий атомпрома.
Другое направление НИОКР — это разработка углеволокон с применением пековых технологий. Пековые волокна обладают интересным сочетанием свойств: традиционной для композитов легкостью, высоким пределом прочности при растяжении не менее 3500 МПа и коэффициентом теплопроводности не менее 600 Вт/м·К. Это делает такое углеволокно предпочтительным кандидатным материалом для изготовления теплорассеивающих панелей радиаторов космических аппаратов. К 2024 году мы выйдем на первые образцы изделий с заданными свойствами.
К 2030 году основная часть этих проектов должна быть завершена. Поэтому в 2027–2028 годах по направлению металлических материалов мы должны будем иметь промышленные технологии, по направлению композитов — готовые изделия, прошедшие испытания.
После 2030 года, на мой взгляд, будет активно развиваться термоядерная энергетика, а значит, нужно будет разрабатывать и материалы для нее. А еще у ученых Росатома уже есть задумки по футуристичным материалам, связанным с биопечатью, и их различным применениям.
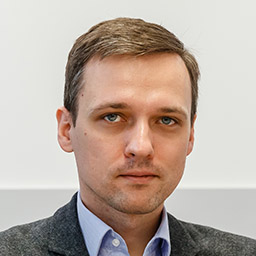
Цифровое материаловедение
Павел Козлов
Научный руководитель проектов НИОКР по разработке инфраструктуры для создания новых материалов
— У Росатома широкая линейка инновационных установок: это водо-водяные, жидкосолевые, быстрые реакторы. Развитие любых конкурентных технологий атомной энергетики напрямую связано с доступностью материалов, обеспечивающих достижение заданных параметров надежности и безопасности на протяжении всего срока службы оборудования. Атомная отрасль — одна из самых консервативных, и для разработки материалов, особенно топливных и материалов активной зоны, может требоваться не одно десятилетие. Поэтому особое место в федеральном проекте занимают работы по созданию инфраструктуры ускоренной разработки материалов.
Здесь выделю два основных направления. Первое — инструменты цифрового материаловедения, которые включают в себя большой пул программ для моделирования и предсказания свойств материалов. Фундаментом является база данных свойств реакторных материалов, насчитывающая тысячи результатов экспериментов. Уже разработаны инструменты, позволяющие анализировать данные в заданных граничных условиях и предсказывать специальные свойства материалов: радиационную стойкость, распухание, некоторые физико-механические свойства, например жаропрочность. При этом речь идет о широкой группе материалов: стали, сплавах и даже композитах. Сейчас продолжаются работы по расширению функциональных возможностей этих инструментов, пополняется база данных.
Второе важное направление — разработка методик ускоренных испытаний материалов, в том числе с использованием ионных ускорителей. Это испытания, позволяющие получить высокие значения повреждающих доз путем облучения тяжелыми ионами металлов, ядрами гелия и водорода. Такие испытания на порядок быстрее и доступнее реакторных: 1–3 месяца вместо 10 лет, стоимость ниже в 10 раз. Вдобавок после испытаний мы получаем образцы, сразу готовые к исследованиям, тогда как после реакторных испытаний сборка должна до полугода «высветиться» в водяном бассейне.
В целом применение этих инструментов и методик позволит заменить дорогостоящие реакторные эксперименты на этапе выбора кандидатных материалов перед выходом на стадию промышленного освоения и сократить время разработки в полтора-два раза. Отобранные таким образом материалы уже идут на реакторные испытания для обоснования их ресурса в условиях, максимально приближенных к эксплуатации.
В 2024 году мы ожидаем отработку всех этих методик, а к 2030 году эти инструменты должны войти в регулярную практику материаловедов-исследователей, что позволит существенно ускорить темпы поиска и разработки новых материалов.
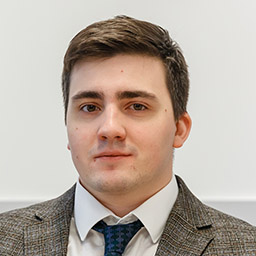
Аддитивные технологии
Александр Жедаев
Руководитель направления аддитивных технологий
— Аддитивные технологии сейчас — ключевой инструмент для ускорения разработки и изготовления новых перспективных изделий и устройств для наукоемких отраслей. Именно поэтому одной из главных целей нашего направления является изготовление целевых изделий с применением новых технологических подходов.
В рамках четвертого федерального проекта РТТН применяется комплексный подход к реализации НИОКР в области аддитивных технологий. Он включает в себя создание материалов, программного обеспечения, аддитивного оборудования как ключевых компонентов при разработке технологии изготовления целевых изделий.
В 2022 году на площадке НИИ НПО «ЛУЧ» был изготовлен и успешно испытан опытный образец трехосевой лазерно-оптической системы для применения в установках селективного лазерного плавления. Устройство уникально и не имеет аналогов в мире. Оно позволяет не только управлять лазерным излучением в процессе синтеза изделия, но и контролировать температуру в жидкой ванне расплава диаметром около 100 микрометров, а также управлять кристаллизацией в короткий промежуток времени — до 500 микросекунд.
Другим достижением 2022 года является разработка и создание опытных образцов 3D-принтеров для печати изделий из керамических и полимерно-композиционных материалов, работающих по технологиям стереолитографии фотополимерной пастой, прямого нанесения керамической пасты карбида кремния, а также прямого нанесения полимерных композиционных материалов с возможностью управления армированием в объеме изделий.
Команда Санкт-Петербургского политехнического университета Петра Великого, ведя исследования в области металлической 3D-печати, разработала и изготовила два опытных образца аддитивных установок. Первый образец — установка электродугового выращивания, второй — установка плазменно-дугового выращивания. Оба образца приступят к изготовлению крупногабаритных изделий уже в первом квартале 2023 года.
Также в этом году будут изготовлены и другие образцы перспективного аддитивного оборудования. Это, например, установки высокотемпературного селективного лазерного плавления, разработанные НПО «ЦНИИТМАШ», а также установки прямой электронно-лучевой наплавки и селективного электронно-лучевого плавления НИИ НПО «ЛУЧ».
В 2024 году мы планируем провести испытание целевых изделий в условиях, приближенных к эксплуатационным, чтобы доказать и продемонстрировать эффективность новых технологических подходов. Цель к 2030 году — вывести наши технологии на уровень серийного производства. Для этого нужно будет решить вопрос с нормативной документацией, чтобы изделия, изготовленные с применением аддитивных технологий, можно было использовать в существующих устройствах.
Уже сейчас мы пробуем печатать модели изделий для ядерного острова, например корпуса реакторов, и изучаем, как они будут вести себя под воздействием облучения. Думаю, после 2030 года нормальной практикой будет применение аддитивных технологий не только для изготовления новых деталей, но и для оперативного ремонта вышедших из строя. Уже сейчас существуют методы обратного инжиниринга, когда деталь, вышедшая из строя, подвергается 3D-сканированию для создания 3D-модели, по которой будет изготовлена точная копия.