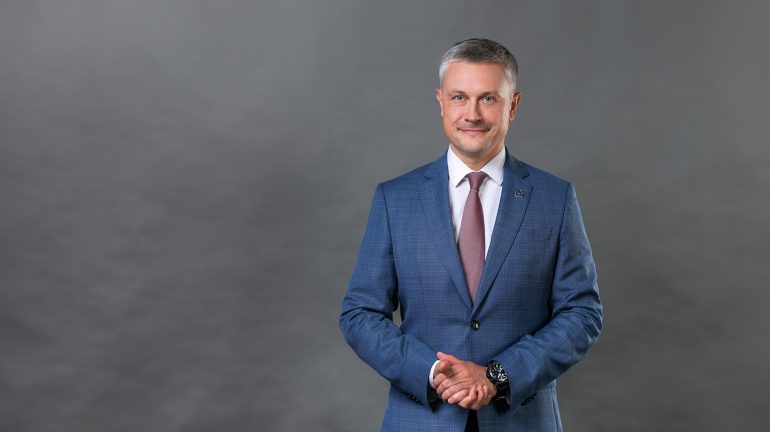
«Наша цель — сделать Россию передовой страной в области композитных технологий»
Александр Тюнин, гендиректор Композитного дивизиона Росатома, — о достижениях и новых задачах дивизиона
Производство композитов — один из самых интересных новых бизнесов Росатома. Композитный дивизион участвует в создании материалов для нового транспорта и чистой энергетики, экономичных строительных решений и спорта высших достижений. О том, какие задачи ставит перед собой и решает Композитный дивизион Росатома, какова динамика и ключевые тренды российского и мирового рынков, «Вестнику атомпрома» рассказал генеральный директор дивизиона Александр Тюнин.
Краткая композитная хроника
— Александр, расскажите, какой была история становления дивизиона.
— Начать надо с 1970-х годов. СССР серьезно развивал тематику композитных материалов и входил в тройку лидеров как по производству, так и по потреблению. Но многие годы углеродное волокно использовалось в основном в специальных применениях и для производства центрифуг для обогащения урана для обеспечения атомных электростанций топливом. После распада страны в предбанкротном состоянии оказались два композитных предприятия: челябинский Завод углеродных и композиционных материалов и балаковский «Аргон». Росатом взял их под свое крыло, сохранил компетенции, чтобы гарантированно обеспечивать собственные потребности и государственный заказ. А в 2016 году было принято решение сформировать самостоятельный дивизион и объединить эти два предприятия с третьим, вновь построенным и запущенным в 2015 году передовым заводом по производству углеволокна в Татарстане. На тот момент в России не было современного производства базового сырья — ПАН-прекурсора, белой нити, которая обеспечивает 70% качества и половину себестоимости (это сырье покупалось в Китае).
Преимущества полимерных композитов:
— легкость;
— прочность;
— стойкость к коррозии и агрессивному воздействию сред;
— технологичность (возможность получать заданные свойства в конкретной точке изделия);
— снижение углеродного следа.
Подробности
За прошедшие семь лет мы создали единственную на территории России, стран СНГ и Восточной Европы полную производственную цепочку — от сырой нефти до крыла самолета МС-21, корпусов кораблей, ракет, автомобилей, топливных газовых баллонов, линейки строительных продуктов, спортинвентаря. Что важно, все технологии собственные! В период с 2018 по 2021 год, несмотря на серьезные пандемические ограничения, в чистом алабужском поле построили самый современный завод по ключевому сырью — ПАН-прекурсору, сырьем для которого, в свою очередь, выступает нитрилакриловая кислота, производная нефтепереработки, один из продуктов, получаемых при изготовлении пропилена. Из ПАНа там же, в Татарстане, и в балаковском «Аргоне» производим углеродное волокно широкой номенклатуры, которое идет как напрямую заказчикам, так и на наши собственные предприятия в Подмосковье, Москве и Балакове для производства тканей, лент и препрегов.
Препреги — основа для производства многих готовых изделий, в частности элементов механизации и хвостового оперения самолета МС-21. На углеродном волокне в мире практически никто не зарабатывает, вся экономика в следующих переделах — тканях, препрегах и готовых изделиях. Ровно поэтому наша стратегия на первом этапе обеспечила Россию полной цепочкой композитных материалов, а текущий этап предполагает активный выход в сегмент готовых композитных изделий в шести ключевых отраслях, драйверах мирового развития композитов — это авиация и космос, ветроэнергетика, автопром, строительство, газомоторный транспорт и водород, спорт и здоровье.
В последние годы мы стали участниками ижевского «Реал-Шторма» — российского лидера по производству композитных топливных газовых баллонов; производителя профессиональных хоккейных клюшек «ЗаряД» в Татарстане; саровского «Русатом Пултрузия», а также предприятий по производству композитных шпунтов, лотков, мостовых конструкций, строительной химии. Кроме того, в конце 2022 года мы приобрели два американских актива во Владимирской и Тверской областях и стали лидерами не только по углеродному, но и по стекловолокну, материалам на его основе, теплоизоляции. В целом за последние два года в дивизионе появилось более десятка новых компаний, как в полной собственности, так и совместные предприятия (50/50). В этом году открываем инжиниринговое направление по разработке отечественного оборудования.
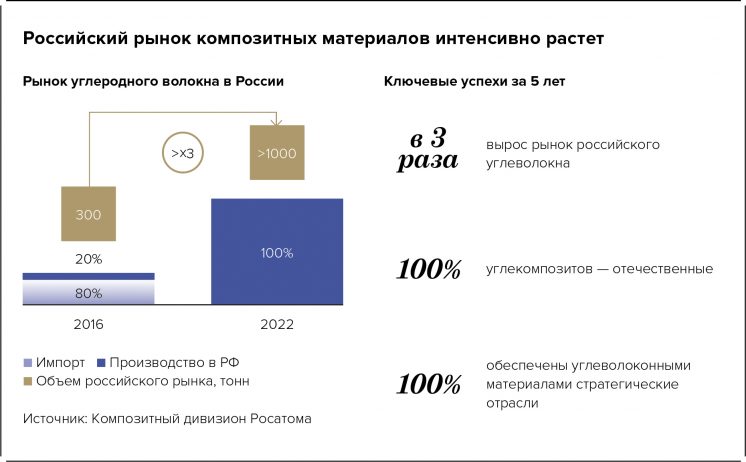
— В структуре дивизиона есть стекло- и углекомпозитные мощности. Базальтовое волокно не интересно?
— Базальтовое волокно используется в мире кратно меньше, чем углеродное и стекловолокно. В России есть производители базальтового волокна, они нашли свою нишу прежде всего в дорожном строительстве, но объем рынка пока невелик. К сожалению, распространения оно не получило, потому что технико-экономических преимуществ у угле- и стекловолокна пока больше. Перспективы дальнейшего развития у базальта есть, но пока такого динамичного развития, как у стекловолокна и углеродного волокна, не происходит. На российском рынке доля стекловолокна и изделий из него в деньгах составляет порядка 59%; углеродное волокно, углепластики и изделия из них — где-то 30%; остальные виды волокна и композитов на их основе — порядка 11%. Общий объем российского рынка — немногим более 100 млрд рублей.
— Кроме волокон, в композитах есть связующие. Какова стратегия компании в развитии этого направления?
— В части волокон мы обеспечили России технологический суверенитет. В области ткачества и препрегирования и мы, и другие компании тоже создали необходимые мощности, и страна сегодня все свои потребности закрывает. При этом потребление серьезно растет каждый год, реализуются государственные программы по развитию ветроэнергетики, газомоторного транспорта, авиационной техники, беспилотных летательных аппаратов, что требует кратного масштабирования производства. Связующие мы и другие компании тоже разработали. А вот компонентная база для этих связующих, малотоннажная химия, сегодня на 90–95% импортная. Львиная доля оборудования тоже из-за рубежа. Правда, последние семь-восемь лет появляются новые компании, которые начинают делать отдельные виды оборудования. Но, во-первых, это пока еще первые шаги, а во-вторых, пока не так много этого оборудования. Поэтому, если говорить в логике импортозамещения, я бы так сказал: около 60% всех потребностей рынка (материалы) за последние семь-восемь лет мы заместили. Следующие этапы — компонентная химическая база и оборудование. Мы и ряд других игроков эту задачу будем решать.
Композитный драйв
— Расскажите, пожалуйста, подробнее, как и где применяются современные композиты.
— Во-первых, в возобновляемой энергетике. Лопасти ветроустановок, солнечные панели — стопроцентный композит. Все больше композитов применяется в строительстве современных атомных электростанций. Вторая важная сфера — транспорт. За последние 20 лет доля композитов в самолетах Airbus и Boeing увеличилась с 10 до 50% и продолжает расти, повышая топливную эффективность на 20% и сокращая эксплуатационные затраты на жизненном цикле самолета на 30%. Наш новейший МС-21 уже на 30% углекомпозитный. Топливную эффективность и скоростные характеристики за счет снижения веса корпуса композиты обеспечивают и в современных электрокарах, скоростных поездах, в водном транспорте. Третья сфера — более экологичные, прочные и дешевые, чем металлические, баллоны для газомоторного транспорта. В перспективе эти баллоны можно будет использовать для водорода. Четвертая — строительство. С помощью композитов строятся дома, предприятия, мосты и дороги, укрепляются берега и прочее. Пятая — спорт и здоровье людей. Сейчас практически в каждой семье есть хоккейные клюшки, теннисные ракетки, сноуборды и лыжи, велосипеды, которые по большей части композитные.
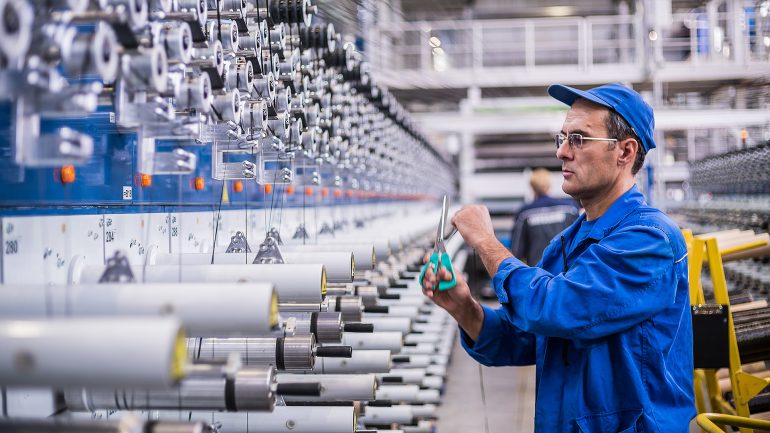
— Насколько на композитном рынке совпадают центры производства и потребления?
— Исторически мировые лидеры композитного рынка — Япония, США и Западная Европа. Это страны и регионы, где композитная отрасль развивается быстрее всего. Если брать японцев, они всегда производили больше, чем потребляли сами. За последние 20–30 лет в сегменте композитов, особенно в углепластиках, они задавали многие тренды. В США внутренний рынок большой, но они много поставляют и в другие страны. Западная Европа в большей степени себя обеспечивает. Китай сейчас активно развивает как собственное потребление, так и экспорт. Считаю, что Китай в перспективе ближайших пяти-семи лет точно будет входить в уверенные лидеры и по объемам производства, и по объемам потребления внутри страны, и по объему экспорта по всему миру. В целом потребление композитов с каждым годом уверенно растет.
— Каковы темпы роста?
— В мире в целом по композитам рост составляет 5–8% в год (различается по регионам), по углепластикам — 11%.
— А в России как обстоят дела?
Мировой рынок композитов
~ $100 млрд
объем рынка
~ 12 млн тонн
производство стекловолокна
~ 120 тыс. тонн
производство углеродного волокна
Цифры
— Что отрадно, наша российская отрасль хоть и невелика в абсолютных цифрах — мы занимаем порядка 1% мирового рынка, — но на те же 5–6% в год растет. А если брать отдельно углекомпозиты, где наш дивизион занимает лидирующие позиции, рынок России увеличен за последние шесть лет в 3,5 раза. На рынках металлов темпы роста существенно ниже. Композитная отрасль перспективна, и не случайно Росатом развивает это направление как один из ключевых новых бизнесов. У нас большое пространство для роста, потому что, если брать такой показатель, как количество композита на душу населения, мы пока серьезно отстаем. У нас используется порядка полукилограмма композитов на человека в год, в мировых ведущих экономиках — 4–6 кг, в ряде стран до 8–10 кг доходит. Поэтому ближайшая наша задача — эту перспективную отрасль масштабировать в нашей стране, чем мы каждый год и занимаемся. Речь идет о рынке и материалов, и готовых изделий.
— Насколько потребители в России заинтересованы в использовании композитов?
— Авиастроители очень заинтересованы и являются драйверами развития рынка. Рывок произошел благодаря проектированию самолета МС-21. Его сразу планировали делать конкурентоспособным на мировом уровне. Конструкторы спроектировали уникальное по аэродинамическим характеристикам крыло полностью из углепластика, но американского, потому что на тот момент отечественного не было. В августе 2018 года американцы остановили поставки, и мы очень быстро, буквально за два года, прошли весь путь квалификации наших материалов и полностью импортозаместили американские в крыле, элементах механизации и хвостовом оперении.
— Каково положение дел для вас в российском самолетостроении на текущий момент?
— Дивизион — поставщик для серийных самолетов, поскольку МС-21 уже вышел в серию. За последние два года объем материалов, которые мы поставляем авиастроителям, удвоился. Кроме того, правительство РФ утвердило программу развития авиационной техники, в ней, конечно, ставка сделана на масштабирование авиапарка на базе МС-21, ТУ-214. Так вот, только эти поставки с 2035 года полностью загрузят нашу площадку по производству углеволокна в Татарстане. Помимо этого, утверждена программа по развитию беспилотных летательных аппаратов, наши материалы активно применяются в вертолетной технике. Нужно масштабировать производственные мощности по всем материалам, что мы и собираемся делать.
— Какие еще отрасли в России наращивают потребление композитов?
— Судостроение. Во-первых, мы, начиная еще с 2017 года, поставляли углеродные ткани и стеклоткани на ведущие итальянские судоверфи для производства люксовых яхт и катеров, а также обеспечивали все программы Объединенной судостроительной корпорации по их композитному кораблестроению. Во-вторых, мы планируем создать верфь на Сахалине по выпуску композитных судов. Проект уже утвержден Росатомом и находится в финальной стадии получения льготного долгосрочного финансирования со стороны ВЭБ.РФ. Напомню, на Восточном экономическом форуме в 2022 году мы подписали с Министерством по развитию Дальнего Востока и Арктики, Корпорацией развития Дальнего Востока и Арктики и администрацией Сахалина соглашение о создании верфи в порту Корсаков, где предполагаем выпускать линейку полностью композитных рыболовных, пассажирских и грузовых малоразмерных судов.
Продолжая про драйверы. Программа ветроэнергетики, в которой активно участвует Росатом, стимулировала производство ветролопастей. Мы утвердили в Росатоме и приступили к реализации проекта по созданию собственных ветролопастей в Ульяновске. Раньше Ветроэнергетический дивизион Росатома покупал их за рубежом. Теперь у нас будут свои, причем нами самими спроектированные лопасти. На 90% они будут состоять из стекловолокна, еще 10% — ребро жесткости из углеродного волокна. Первый комплект мы должны поставить Ветроэнергетическому дивизиону до конца этого года, затем будем активно поставлять лопасти в течение двух лет, до конца 2026 года. Наши инвестиции в создание производства лопастей вполне окупаются поставками на российский рынок. Кроме того, Ветроэнергетический дивизион активно работает над расширением своего присутствия за пределами России: коллеги прорабатывают ряд международных проектов.
— Вы еще упомянули программу по развитию газомоторного топлива для автотранспорта. Это касается производства композитных баллонов, так?
— Да, дивизион сейчас лидирует на российском рынке композитных баллонов для компримированного газа для автобусов, грузовиков, систем транспортировки и хранения газа, мобильных заправок благодаря участию в капитале ижевской компании «Реал-Шторм». Всего за год с момента покупки мы удвоили масштаб бизнеса в России и вышли на белорусский рынок. В прошлом году первые полторы тысячи баллонов поставили Минскому автомобильному заводу — МАЗу. Следующий этап — завершение разработки баллонов для водорода, опытные образцы уже созданы и проходят испытания. Росатом позиционируется как производитель водорода в будущем, поэтому сейчас мы разрабатываем линейку емкостей, начиная от емкостей для автомобилей (грузовых, легковых) и вплоть до крупных морских газовозов, проводим НИОКР. Программа газомоторной техники, которую правительство несколько лет назад утвердило, — хороший пример господдержки. Я искренне считаю, что господдержка работает, когда она нацелена на формирование спроса. Видите, и ветроэнергетическая программа породила целый ряд новых производств в России, и газомоторная программа тоже дала серьезный толчок развитию производства композитных баллонов.
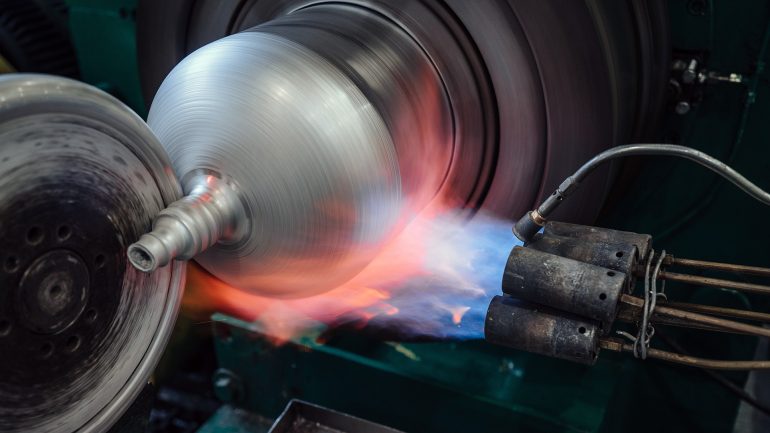
— Говоря про транспорт, нельзя не затронуть сегмент электромобилей.
— Конечно. Мы, естественно, тесно сотрудничаем с Топливным дивизионом Росатома в программе электромобильности, прорабатываем свою часть проекта по созданию электромобиля. Это все композитные элементы корпуса, потому что корпус надо делать максимально легким. Кроме того, в проработке собственная платформа электромобилей коммерческого класса. Но об этом подробнее расскажу в следующий раз, когда проект перейдет в инвестиционную фазу.
— Как развивается строительное направление?
— В России, как и во всем мире, строительные компании и вообще любые компании, улучшающие свою инфраструктуру, все больше и чаще используют композиты. Мы за последние три-четыре года кратно масштабировали и линейку продуктов, и размер бизнеса. Сегодня это одно из ключевых направлений, где мы в том числе решаем внутриотраслевые задачи. В частности, поставляем шпунт для дивизиона «Экологические решения», который обеспечивает безопасную ликвидацию объектов накопленного вреда. Свежие примеры — ртутный цех бывшего «Усольехимпрома» в Усолье-Сибирском и полигон в Красном Бору. Более ранний — подземная линза нефтепродуктов на территории «Усольехимпрома». Это самые грязные объекты, которые по всему периметру огородили нашим композитным шпунтом. Погрузили шпунт более чем на 10 м в глубину, чтобы избежать попадания ртути, нефтепродуктов и других опасных веществ в грунтовые воды и Ангару.
Мы также поставляем композитные шпунты и лотки для берегоукрепления, проектируем цельные композитные пешеходные мосты: с РЖД есть целая программа, планируем строительство пилотных образцов. Построили несколько полимерных наплавных мостов через реки, береговых площадок для производственных, технологических и бытовых нужд. Мы абсолютный лидер в России на рынке систем внешнего армирования, которые применяются для модернизации и капитального ремонта зданий и сооружений с продлением срока службы на 10–30 лет с затратами на 20–30% ниже капитального ремонта из традиционных материалов. Использование внешнего армирования позволяет ремонтировать объекты, не прекращая их эксплуатацию. Это важно, например, для городов, разрезанных рекой на две части, в России таких много. Традиционная история: два-три месяца ремонтируется мост, по всему городу пробки, объезды, нервы и срывы. А применяя систему внешнего армирования, можно не ограничивать поток транспорта.
— Какова ситуация в спорте?
— Потребление композитов тоже растет. Наша первая ласточка — производство профессиональных хоккейных клюшек совместно с трехкратным чемпионом мира Данисом Зариповым. Следом за клюшками пошли мотокомпоненты, которые уже четвертый год едут в чемпионате мира по мотогонкам. Третья ласточка — профессиональный сапборд. Наши ведущие спортсмены его высоко оценили.
Инвестпланы и научные разработки на перспективу
— Если российский рынок растет по разным направлениям, то возникает вопрос, достаточно ли дивизиону существующих мощностей для соответствия растущему спросу?
— Хороший вопрос. Давайте приведу пример. Когда в 2016 году мы сформировали дивизион, наш завод в Татарстане не имел ни одного заказчика, а по мощности в 3,5 раза превосходил потребности российского рынка. Сегодня у нас дефицит мощностей, заказчики выстраиваются в очередь, потому что мы завод загрузили полностью. Это значит, что за прошедший период российский рынок углекомпозитов мы увеличили в эти самые 3,5 раза. Поэтому следующий этап нашего развития — масштабировать кратно свои производственные мощности.
Планируем до конца I квартала этого года утвердить инвестиционный проект по строительству очередной линии по производству углеродного волокна. Что важно, предполагаем частично использовать для нее отечественное оборудование. Будем его создавать вместе с партнерами. Для этого мы создали инжиниринговое направление и планируем разрабатывать оборудование не только для себя, но и для композитного рынка в целом. Завод по выпуску стекловолокна будем модернизировать и строить вторую очередь. Потребность в нем постоянно растет, а жить на дефицитном рынке материала — значит сдерживать развитие самого рынка и нашего бизнеса. В Челябинске развиваем производство высокомодульных углеродных волокон на основе углеродных волокон из отечественного ПАН-прекурсора.
Мы растем как органически, создавая новые мощности, так и через сделки слияния и поглощения. Но такие сделки — это не просто сложение финансовых показателей в отчетности. Новые активы мы продолжаем энергично развивать, масштабировать, создавать новые продукты, осваивать новые технологии. Бизнес же тоже можно масштабировать по-разному. Мы ставим задачу быть передовой, высокотехнологичной компанией, создавая новейшие продукты. За семь лет мы преодолели 20-летнее отставание, догнали ведущие мировые компании в сегменте углеродного волокна. И теперь наш научно-исследовательский центр разрабатывает технологии на опережение.
— Какие именно технологии разрабатывают в центре?
— Углеродные волокна с различными свойствами, среднемодульные и высокомодульные. В научно-исследовательском центре в 2023 году получили первые образцы прочностью 7 ГПа. Такое волокно выпускают в мире всего две японские компании. Поясню для сравнения: самое распространенное в мире волокно Т700 имеет прочность 4,9 ГПа, его доля — около 80% рынка. Волокно Т800 имеет прочность 5,5 ГПа, применяется там, где нужна повышенная прочность. А волокно прочностью 7 ГПа — это передовая научная разработка. Оно массово не потребляется и не производится, но в перспективе призвано еще больше облегчать конструкции. Это важно, например, для космоса, где вывод на орбиту каждого килограмма стоит очень больших денег. Кроме того, к современным изделиям предъявляются повышенные требования. Поэтому, когда появляются материалы, которые могут им соответствовать, появляется и спрос на такие материалы.
— Такое волокно, наверное, будет очень дорогим.
— Цена, естественно, высокая на первом этапе, пока объемы производства маленькие. Но, во-первых, рынок масштабируется: сейчас целый ряд стран инвестирует в создание новых мощностей. Во-вторых, одна из ключевых тенденций развития композитов — все более масштабное использование цифровых инструментов при разработке материалов и конструировании конечных изделий. Пока материалы разрабатываются в научно-исследовательских центрах с помощью исследований, проб и ошибок. Цифровое проектирование должно резко сократить сроки и себестоимость разработок. В-третьих, активно развивается рециклинг. Использование вторичного сырья вдвое дешевле первичного производства волокон и их производных, кроме того решает проблемы, связанные с экологической повесткой.
Кластер «Композиты без границ»
Для развития усилий ведущих игроков российского композитного рынка сформирован Межрегиональный промышленный кластер «Композиты без границ» — по инициативе Композитного дивизиона госкорпорации «Росатом», ответственного за развитие направления полимерных композиционных материалов (ПКМ). Кластер зарегистрирован в Реестре Минпромторга России в 2018 году. В кластер входят:
— 7 регионов;
— 7 инфраструктурных площадок;
— 9 вузов;
— 51 промышленная компания.
Ключевые задачи кластера:
— формирование экосреды и развитие кооперации;
— стимулирование спроса на композиты на российском рынке, содействие реализации их экспортного потенциала;
— Обеспечение господдержки производителям композитов.
Подробности
Все эти факторы, как кирпичики, складываются в поступательное снижение цены. Кроме того, во многих названных мной отраслях смотрят не только на цену материала, но и на финансовые параметры жизненного цикла изделия, и где-то этот фактор даже важнее. Ведь композит может работать до 100 лет и более, не требуя обслуживания, как металл, который, например, если взять морские и речные суда, надо красить, то есть ставить судно в док на срок до месяца. Экономическая выгода от композитов в целом ряде применений, которые мы обсчитывали, на жизненном цикле по сравнению с традиционными материалами доходит до 30%.
— Вы упомянули про рециклинг. Что-то уже делаете в этом направлении?
— В Челябинске мы построили первую линию по рубке остатков тканей после раскроя. Порубленная масса стала новым продуктом, мы его продаем для штамповки изделий. Это первый шажок на пути переработки и вовлечения отходов в производство. Пока нет ни одной компании, которая научилась бы полностью перерабатывать отслужившие свой срок композиты, но нужно в этом направлении активно двигаться вперед.
— А «цифру» как развиваете?
— Полноценное проектирование в «цифре» у нас пока только в планах. Наша задача — построить цифровые двойники технологических процессов предприятий, чтобы научиться получать требуемые параметры материала.
О господдержке
— Вы уже говорили о господдержке. Какие меры, на ваш взгляд, будут стимулировать отрасль?
— Мы и сами в определенном смысле — один из видов господдержки. Дивизион отвечает за выполнение дорожной карты «Технологии новых материалов и веществ» по направлению «Полимерные композиционные материалы», в 2018 году создали кластер «Композиты без границ», в него входит уже более 60 участников и 7 регионов. Мы помогаем выстраивать кооперационные цепочки, обеспечиваем тягу спроса по всей технологической цепочке и помогаем бизнесу получить меры господдержки.
— Каким образом?
— У компаний различается масштаб деятельности, бизнесмены далеко не о всех мерах поддержки знают и не всегда умеют их использовать, и мы им помогаем эти задачи решить.
В 2023 году в рамках исполнения дорожной карты, потратив четыре года, мы наконец добились утверждения правительством России комплексной научно-технической программы (КНТП). На нее выделено больше 7 млрд рублей, из которых половина — федеральное финансирование и половина — плечо бизнеса. Задачи КНТП — импортозамещение малотоннажной химии и компонентов, разработка технологий рециклинга, развитие самых передовых технологий по проектированию и изготовлению конечных изделий. В рамках КНТП пять компаний получили прямое федеральное финансирование. Я считаю, принятие программы — очень важный шаг, потому что целый ряд компаний получили поддержку на формирование технологического задела. Создавать его — самое сложное для бизнеса, потому что нужны деньги длинные, не быстро окупаемые, и, конечно, без плеча государства формирование технологического задела ни в одной отрасли, включая композиты, просто невозможно.
Уже названные мною неоднократно государственные программы по авиации, ветроэнергетике, газомоторному транспорту формируют серьезный спрос по всей производственной цепочке. Считаю такие меры поддержки гораздо более эффективными и полезными, чем прямое субсидирование отдельных инвестиционных проектов.
Человеческий взгляд
— Как решаете вопросы с кадрами?
— Во-первых, популяризируем композиты в целом для населения страны. Уже семь лет «из каждого утюга» стараемся про композиты рассказывать, из года в год осведомленность повышается, но над этим надо постоянно работать. Второй момент — профподготовка кадров. Мы ведем системную работу — от детишек младшего возраста до студентов и магистров. Например, мы выпустили мультфильм и детскую книжку «Фиксики» про композиты, чтобы малыши знали, где они применяются, что это за материалы, в чем их преимущество.
В сочинском «Сириусе» создали производственно-образовательный центр, где ребята сначала на компьютерах проектируют 3D-модели, а затем на оборудовании, которое мы за свой счет в этом центре поставили, делают готовые изделия — кораблики, квадрокоптеры или что-то еще. Более того, мы с «Сириусом» прорабатываем проект, чтобы дети не просто получали начальный опыт проектирования и изготовления, а творческая наша молодежь придумывала какие-то передовые изделия, о которых мы пока даже не задумываемся. Мы готовы эту историю поддерживать, чтобы открывать для себя новые ниши.
Системная работа идет с вузами, с РХТУ им. Д. И. Менделеева мы три года назад открыли магистратуру, сейчас у нас там уже порядка 80 магистров. Еще один проект — передовые инженерные школы, в них 150 ребят учатся по композитному направлению. Два инжиниринговых образовательных центра мы сделали в Казани и в Ульяновске, это полноценные программы практического обучения студентов, центры полностью оснащены современным оборудованием. Фактически это мини-производства. Там получают полный набор компетенций не только студенты, но и сотрудники композитных компаний, поскольку квалифицированных специалистов на рынке не хватает. На Сахалине мы сразу озадачились вопросом: а откуда мы возьмем на верфь 400–500 человек, которые умели бы работать с композитами по заданным технологиям? Будем создавать инжиниринговый образовательный центр, который на месте поможет выращивать специалистов и повышать их компетенцию.
Уже 10 лет проводим главный в стране тематический ежегодный форум «Композиты без границ», собирая на одной площадке всех игроков российского рынка, зарубежных партнеров и экспертов, вузы и науку, молодежь. Обсуждаем ключевые тренды развития отрасли, достижения российских предприятий, задачи по обеспечению технологического суверенитета.
— Может, есть смысл создать безлюдные производства?
— Где возможно и выгодно, автоматизацию будем применять. Но та же значимая для России верфь является, например, для Китая мелкосерийным производством. Поэтому где-то автоматизация снизит затраты, а где-то будет необоснованно дорога. На новых заводах, которые мы строим и которые полностью покрывают все потребности страны, и так уже работают сотни человек, а не тысячи и не десятки тысяч. На той же линии по производству углеродного волокна весь процесс автоматизирован, операторы только контролируют его непрерывность и следят, чтобы параметры не отклонялись от проектных. В этом смысле мы высокотехнологичная компания. Но дело даже не в том, что мы решаем локальную бизнес-задачу в стране. Мы боремся с вызовами мирового масштаба. Поэтому молодежь и идет к нам с охотой.
— Вы нацелены на мировой масштаб?
— Ну конечно. Еще в 2016 году, когда я пришел на первую встречу с главой Росатома Алексеем Евгеньевичем Лихачевым, сказал ему, что наша цель — топ-5 мировых лидеров в области композитов к 2030 году. На что сразу получил встречный вопрос: а почему не топ-3? Круто работать в такой компании, решая задачи уровня мирового лидерства, какой является Росатом. У нас нет сегодня возможности, как в Китае, строить десятками различные линии больших мощностей, но есть большой запрос от ряда стран, которым нужны наши передовые технологии и с которыми вместе мы сможем выйти за пределы Российской Федерации. Поэтому наш следующий шаг — партнерства с международными и локальными игроками, которые нам обеспечат доступ к новым рынкам. Дорогу осилит идущий, наша цель — сделать Россию передовой в области композитных технологий и стать крупной международной компанией, объединив наши технологии с бизнесом на крупных внешних рынках. Над этим и работаем каждый день.