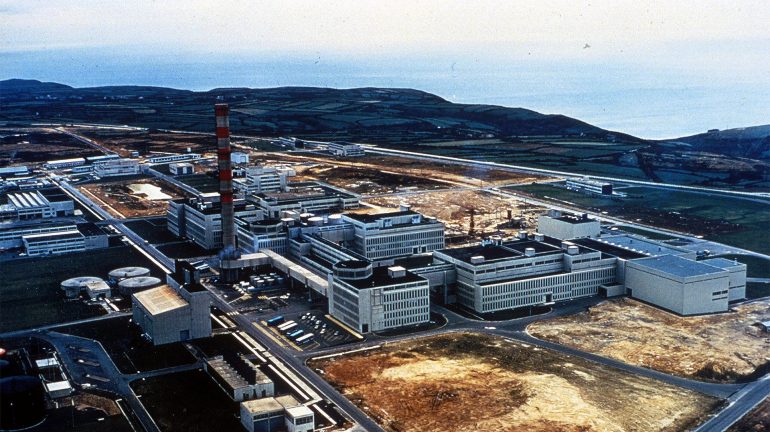
Иногда оно возвращается
Что делают в разных странах с отработавшим ядерным топливом
Эксперты Центра аналитических исследований и разработок частного учреждения «Наука и инновации» изучили [1] технологические решения и процессы, применяемые на основных зарубежных предприятиях по переработке ОЯТ, а также проанализировали опыт эксплуатации, текущий статус и перспективы развития перерабатывающих заводов.

Степан Квятковский
Аналитик Центра аналитических исследований и разработок частного учреждения «Наука и инновации» (госкорпорация «Росатом»):
— Можно отметить два обстоятельства, повлиявших на выбор темы «Технологические решения и процессы, используемые на зарубежных предприятиях по переработке ОЯТ»для отчета. Первое — это принятая стратегия по замыканию ядерного топливного цикла (ЯТЦ) и переходу к двухкомпонентной ядерной энергетике, что потребует модернизации существующих и создания новых промышленных мощностей по переработке отработавшего ядерного топлива (ОЯТ) энергетических реакторов. В этом контексте рассмотрение технических и технологических решений, используемых на зарубежных заводах, может быть полезно и для отечественной отрасли. Второе — на различных международных конференциях и совещаниях иностранными экспертами часто представлялась разрозненная информация о проводимых работах по модернизации действующих заводов или будущие планы по развитию перерабатывающих мощностей. Хотелось провести какую-то систематизацию собранных материалов, понять, где находится мир, а где мы, какие сейчас существуют тренды в этом направлении.
Хотя мы попытались описать основные действующие или действовавшие предприятия и установки в области переработки ОЯТ, с момента зарождения ядерной энергетики их было создано гораздо больше, чем представлено в работе. Кроме того, из-за общей закрытости и чувствительности данного направления не по всем установкам имелось достаточно информации, например по китайским перерабатывающим заводам. С другой стороны, французы и британцы подходят достаточно открыто к публикации собственных материалов. В ряде случаев было так, что поиск какой-либо технической информации, которая занимает в тексте отчета один абзац или одну строку в таблице, занимал несколько дней, но без нее анализ был бы неполным.
Отчет получился достаточно объемным, и в нем много технической информации, что скорее представляет интерес для специалистов отрасли. Однако описание подходов к организации исследований при создании производств, а также информация о планах будущего развития зарубежных мощностей по переработке ОЯТ и о рассматриваемых национальных стратегиях могла бы быть интересна и для руководителей отрасли.
В связи с глобальным ростом потребности в электроэнергии и трендом на декарбонизацию в мире растет интерес к ядерной энергетике. Одно из самых перспективных направлений ядерной энергетики сегодня — замыкание ядерного топливного цикла с повторным использованием отработавшего ядерного топлива (ОЯТ). Это в перспективе позволит не только снизить расходы, но и сделать ядерную энергетику более безопасной для окружающей среды. На сегодня промышленные заводы по переработке ОЯТ действуют только в России, Франции, Индии и Китае. В нашей стране принята стратегия развития двухкомпонентной платформы ядерной энергетики, основанная на замыкании ядерного топливного цикла, которая включает модернизацию существующих установок и создание новых мощностей по переработке больших объемов ОЯТ. Предполагается, что это не только уменьшит объемы хранимого ОЯТ и обеспечит топливом новые энергоблоки с реакторами на быстрых нейтронах, но и станет востребованной услугой на международном ядерном энергетическом рынке.
Франция: от завода к заводу
Промышленная переработка ОЯТ энергетических реакторов во Франции началась в 1966 году с пуском завода UP2. Изначально на заводе осуществлялась переработка ОЯТ газографитовых реакторов, но позже он был модернизирован для переработки оксидного ОЯТ легководных реакторов и получил название UP2-HAO. Сейчас в стране работают два завода, расположенные на мысе Ла-Аг. В 1990 году был запущен завод UP3, рассчитанный на переработку ОЯТ реакторов типа PWR и BWR из стран Европы и из Японии, а чуть позже была завершена реконструкция завода UP2-HAO, который получил название UP2-800 и предназначался для переработки ОЯТ легководных реакторов из Франции. Проектная мощность каждого из заводов составляет 800 тонн в год, но в реальности таких показателей удалось достичь только в 1990-е годы, когда активно выполнялись зарубежные контракты. Общая вместимость бассейнов-хранилищ ОЯТ двух заводов составляет 14,4 тыс. тонн топлива.
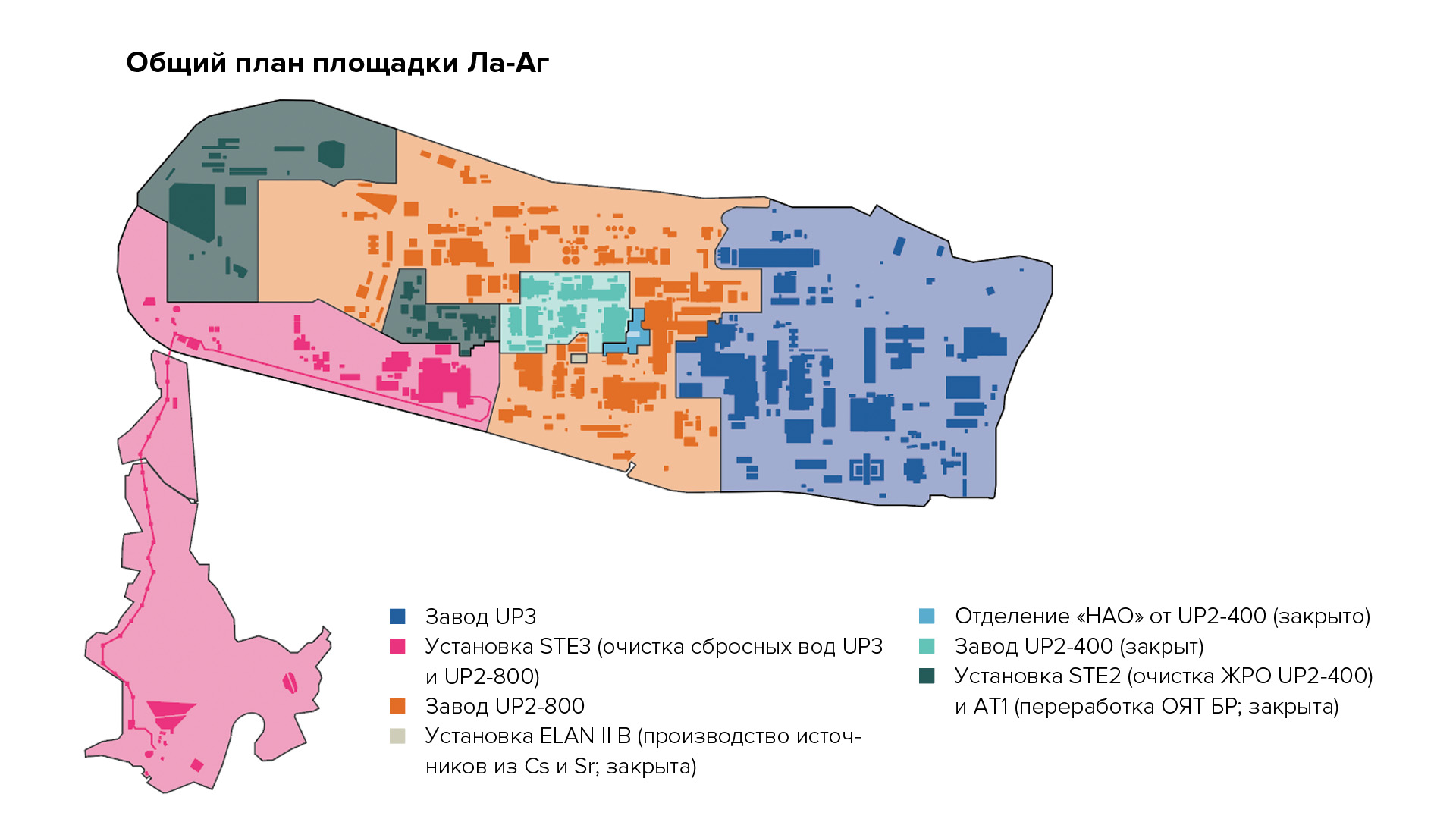
В основе технологии, которая применяется на этих предприятиях, лежит так называемый трехцикличный PUREX-процесс (Plutonium-Uranium Recovery by Extraction — экстракционное выделение урана и плутония). Структурно каждый завод состоит из нескольких отделений, где последовательно проходят приемка ОЯТ, подготовка его к переработке, резка-растворение и подготовка раствора топлива к экстракции целевых компонентов, выделение урана и плутония и разделение их между собой. Затем урановые и плутониевые продукты проходят окончательную очистку и концентрацию. Кроме того, в процессе используют различные установки для обработки газообразных, жидких и твердых радиоактивных отходов, подлежащих дальнейшему хранению и захоронению.
Несмотря на то что оба предприятия структурно похожи, в их технологических процессах есть различия. Так, завод UР2-800 предназначен для переработки оксидного отработавшего топлива французских реакторов PWR, поэтому там используется только одна линия резки-растворения, так как перерабатывается только один тип ОЯТ. На заводе UР3 имеются две линии для резки топлива с зарубежных АЭС (типа PWR и BWR), потому что оно отличается по размерам. Однако сами процессы резки и растворения идентичны на обоих предприятиях.
Процесс обработки ОЯТ начинается с того, что отработавшие тепловыделяющие сборки (ОТВС), которые привезли с АЭС, подвергаются резке. Это нужно, чтобы топливо, находящееся под оболочкой твэла, смогло в последующем раствориться. В процессе резки осуществляется обдувка азотом, чтобы исключить возгорание мелких частиц.
Далее нарезанные фрагменты ОЯТ попадают в узел растворения, в котором под воздействием азотной кислоты происходит растворение топлива, а оболочки твэлов и другие конструкционные материалы удаляются и направляются в РАО.
После этого смесь обрабатывают на центрифуге для освобождения от осадка твердых частиц. Этот процесс называют осветлением. В итоге получается раствор, который подходит для дальнейшего выделения урана и плутония.
После осветления раствор идет на экстракцию. В процессе используется три цикла экстракции, в ходе которых соединения урана и плутония сначала отделяются от продуктов деления, минорных актинидов и других элементов, а потом разделяются для дальнейшей очистки. Эти процессы проходят в трех типах оборудования: специальных колоннах, аппаратах смесителях-отстойниках и в центробежных экстракторах.
Из-за сложности физических и химических процессов, протекающих при переработке ОЯТ, для каждого из этапов по экстракции и очистке урана и плутония подходит свой тип оборудования. Например, смесители-отстойники и пульсационные колонны являются относительно простым, требующим минимального технического обслуживания, но очень габаритным оборудованием. В то же время многоступенчатые центробежные экстракторы обладают значительно меньшими габаритами, высокой эффективностью и производительностью, но имеют гораздо более сложную механическую конструкцию, требующую тщательного технического обслуживания, при этом дистанционного.
Поэтому на данный момент центробежные экстракторы используются на французских заводах только на заключительной стадии экстракции — очистки и концентрации раствора, содержащего плутоний. Затем из раствора получают твердый диоксид плутония.
Таким образом, конечными продуктами заводов являются диоксид плутония и раствор уранилнитрата. Оба продукта предназначены для использования в составе топлива для реакторов АЭС. Диоксид плутония применяется на заводах по изготовлению МОКС-топлива — смеси уранового и плутониевого компонентов.
Начиная с 1976 года на площадке Ла-Аг было переработано порядка 40 000 тонн ОЯТ, из которых более 10 000 тонн приходятся на ОЯТ зарубежных реакторов (Бельгия, Германия, Италия, Нидерланды, Швейцария, Япония). Большую часть переработанного ОЯТ составляет облученное UOX-топливо реакторов типа PWR и BWR с глубиной выгорания от 10 до 45 МВт·сут/кг и массой сборок от 150 до 500 кг. Также была осуществлена переработка более 80 тонн МОКС-ОЯТ реакторов PWR и BWR и порядка 10 тонн МОКС-ОЯТ быстрого реактора Phénix.
Хотя лицензия на эксплуатацию ядерного центра на площадке Ла-Аг, выданная в 2003 году, ограничивает мощность перерабатывающих заводов UP2-800 и UP3 в 1000 тонн ОЯТ в год для каждого из них и не более 1700 тонн ОЯТ в год суммарно, такие показатели за все время эксплуатации площадки были достигнуты всего пять раз. Резкое снижение объемов перерабатываемого ОЯТ после 2000 года связано с завершением переработки основного объема ОЯТ в рамках выполнения первого цикла зарубежных контрактов.
Цифры и факты
Отдельные технологии используют для обезвреживания радиоактивных отходов, полученных в процессе переработки ОЯТ. В 1960-е годы Франция сбрасывала бочки с ними в море или закапывала в землю, но быстро появившиеся утечки заставили отказаться от этой практики. В 1991 году в стране был принят закон об управлении радиоактивными отходами, который предусматривает жесткие нормативы обращения с ними. За это время во Франции был введен ряд мер, которые помогли уменьшить количество радиоактивных отходов и снизить их опасность для окружающей среды. Так, например, на перерабатывающих заводах внедрили рециклирование реагентов, которое позволило исключить из отходов 25–80% нерадиоактивных компонентов. Были разработаны и внедрены технологии переработки радиоактивных отходов: их концентрирование с помощью различных методов, сжигание, прессование и т. п. Итогом стало фактически восьмикратное сокращение количества конечных радиоактивных отходов на производствах по сравнению с проектными значениями.
Высокоактивные отходы подвергаются остекловыванию при температуре 1300 °C. Сейчас французскими разработчиками создана установка, которая позволяет остекловывать твердые и жидкие радиоактивные отходы прямо в канистрах, в которых они будут захоронены. Технология показала свою универсальность, простоту и экологичность.
Кроме того, Франция построила универсальную установку для извлечения плутония из различных радиоактивных отходов производства, включая золу от сжигания, пыль от фильтров, металлические компоненты оборудования, пластик и др. Извлеченный плутоний отправляется на завод для повторного использования, а оставшиеся отходы становятся более безопасными и пригодными для захоронения.
Великобритания: замыкания не будет
Промышленная переработка ОЯТ легководных реакторов в Великобритании началась в 1994 году на заводе THORP (Thermal Oxide Reprocessing Plant). Изначально он строился как коммерческое предприятие по переработке оксидного ОЯТ реакторов типа PWR и BWR в рамках контрактов с зарубежными клиентами, а также ОЯТ газовых реакторов AGR, находящихся в эксплуатации на территории Великобритании. Проектная мощность предприятия составляла 1200 тонн в год. Конечным продуктом завода было МОКС-топливо, которое поставлялось заказчикам.
При создании проекта предприятия разработчики предусмотрели моменты, повышающие его безопасность и надежность. В частности, установки, которые контактировали с радиоактивностью, были спроектированы так, чтобы не требовать ручного обслуживания в течение всего срока службы. Для ремонта оборудования внутри камер использовались дистанционные механизмы, а детали, которые требовали ручного ремонта, обслуживались вне ячеек. Камеры были оборудованы датчиками утечек.
При переработке ОЯТ из отделения хранения попадало в бассейн для подготовки к дальнейшим процессам. Оттуда оно направлялось на резку и выщелачивание и подготовку к экстракционной очистке. Далее следовала экстракция в двух циклах с финальным выделением уранового и плутониевого продуктов и их конверсия в оксиды.
Кондиционирование и ввод топлива в растворитель на заводе THORP производилось в один этап. Оно измельчалось с помощью больших гидравлических ножей на фрагменты в 5–10 см, которые хорошо подходили для растворения. На предприятии использовались три растворителя, через которые последовательно проходило измельченное ОЯТ. Это обеспечивало непрерывный процесс работы: пока в первый растворитель загружалось топливо, во втором происходило растворение, а третий сливал раствор. Для безопасности работы с большим количеством низкообогащенного топлива в растворители добавлялся поглотитель нейтронов — гадолиний.
После осветления раствора на центрифуге его подавали на экстракцию, где выделяли и разделяли целевые компоненты урана и плутония. В первой экстракционной колонне раствор обрабатывался экстрагентом, затем экстракт промывался азотной кислотой. В отличие от французской технологии, экстракт без специальной очистки в отдельной колонне поступал на реэкстракцию. Затем экстракт проходил очистку и шел на разделение.
Очищенный урановый продукт упаривали, а затем распыляли, получая таким образом порошок уранилнитрата. Плутониевая линия завода заканчивалась переводом раствора в диоксид плутония.
Оставшиеся от процесса экстрагент, разбавитель и азотная кислота перерабатывались, а высокоактивные отходы остекловывали двумя стадиями. На первой упаренный концентрат кальцинировали, на второй делали конечный продукт из кальцината и стеклообразующих добавок.
На заводе была также построена специальная установка для уменьшения радиоактивности воды, которую использовали для охлаждения бассейнов хранения ОЯТ. Две другие установки предназначались для извлечения актиноидов из жидких радиоактивных отходов с помощью осаждения. Некоторые виды радиоактивных отходов цементировались в бочках из нержавеющей стали для глубинного захоронения.
Однако во время работы завода на нем произошел ряд аварий. Самой крупной стала утечка 83 тыс. литров смеси ОЯТ с азотной кислотой в 2005 году. Из-за частых неисправностей предприятие останавливали, и его реальная мощность ни разу не достигла запланированной в проекте. По этой же причине заводу не удалось выполнить контракты, заключенные с иностранными поставщиками, в срок: свои обязательства по ним предприятие исполнило на девять лет позже. Также возникли проблемы и с производством МОКС-топлива.
В 2018 году было официально объявлено об окончательной остановке завода THORP. На тот момент все обязательства по переработке иностранного ОЯТ по заключенным ранее договорам были выполнены. Была еще одна причина закрытия предприятия: Великобритания отказалась от замыкания ядерного цикла, поэтому необходимости в переработанном плутонии не было. В стране остановили все быстрые реакторы, а использование МОКС-топлива признали нецелесообразным. Сейчас территория завода рассматривается как площадка для промежуточного долговременного хранения ОЯТ до 2070 года.
Япония: безопасность после «Фукусимы»
В Японии были построены два завода по переработке отработавшего ядерного топлива энергетических реакторов. Первый, TRP (Tokai Reprocessing Plant), пущенный в 1981 году, выполнен по проекту французской компании SGN, дочернего предприятия компании COGEMA (ныне Orano). Он работал с производительностью 90 тонн в год, хотя в проекте было запланировано 210 тонн в год. В 2006 году работа завода была приостановлена, а в 2016 году было принято окончательное решение о его выводе из эксплуатации. Такое решение приняли из-за того, что модернизация предприятия по новым требованиям безопасности, которые ввели после аварии на АЭС «Фукусима-1», оказалась экономически невыгодной.
Сооружение второго завода — RRP (англ. Rokkasho Reprocessing Plant) по переработке ОЯТ и производству МОКС-топлива — началось в 1993 году, а первые поставки ОЯТ прошли уже в 1998 году. Однако запуск предприятия переносился более 20 раз из-за различных инцидентов: утечки воды из бассейнов хранения топлива, повреждения оборудования для остекловывания, протечки жидких радиоактивных отходов и т. д. Новые правила ядерной безопасности, вступившие в силу после аварии на «Фукусима-1», тоже стали причиной для отсрочки пуска завода, так как ему потребовалась модернизация. По свежим данным, переработка ОЯТ на этом заводе должна начаться в 2027 году. Проектная мощность предприятия — 800 тонн в год, на нее планируют выйти к 2032 году. Производство МОКС-топлива на предприятии ожидается только в 2030 году. Завод будет перерабатывать ОЯТ из японских реакторов.
Структура обоих заводов схожа с французскими аналогами. Но нужно отметить, что в качестве одного из продуктов получают уранилнитрат, а в качестве второго — смесь оксидов урана и плутония.
Оборудование имеет, как правило, модульную структуру, что позволяет быстро заменять отдельные блоки при ремонте. Узел для резки исходного продукта дублируется для обеспечения бесперебойного процесса при проведении ремонтных работ. Растворение топлива проходит в непрерывном аппарате-растворителе.
Высокоактивные отходы на заводе RRP предполагается остекловывать. Для этого была разработана собственная установка. Особенность применяемого в ней метода заключается в том, что жидкие отходы и стеклянные ингредиенты помещаются непосредственно в плавильную печь. Там одновременно происходит испарение воды и азотной кислоты, а также плавление стекла. По проекту срок работы плавителя должен был составить пять лет. При этом его размеры в пять раз превысили габариты плавителя, используемого на французских заводах. Однако в ходе испытаний разработчики столкнулись с трудностями контроля температуры расплавов печи — не достигалось нужное значение в 1200 °C. Из-за этого расплавленному стеклу требовалось в три раза больше времени, чтобы стечь из плавителя в канистру. Собственно, проблема с установками по остекловыванию является одной из основных причин переноса запуска завода.
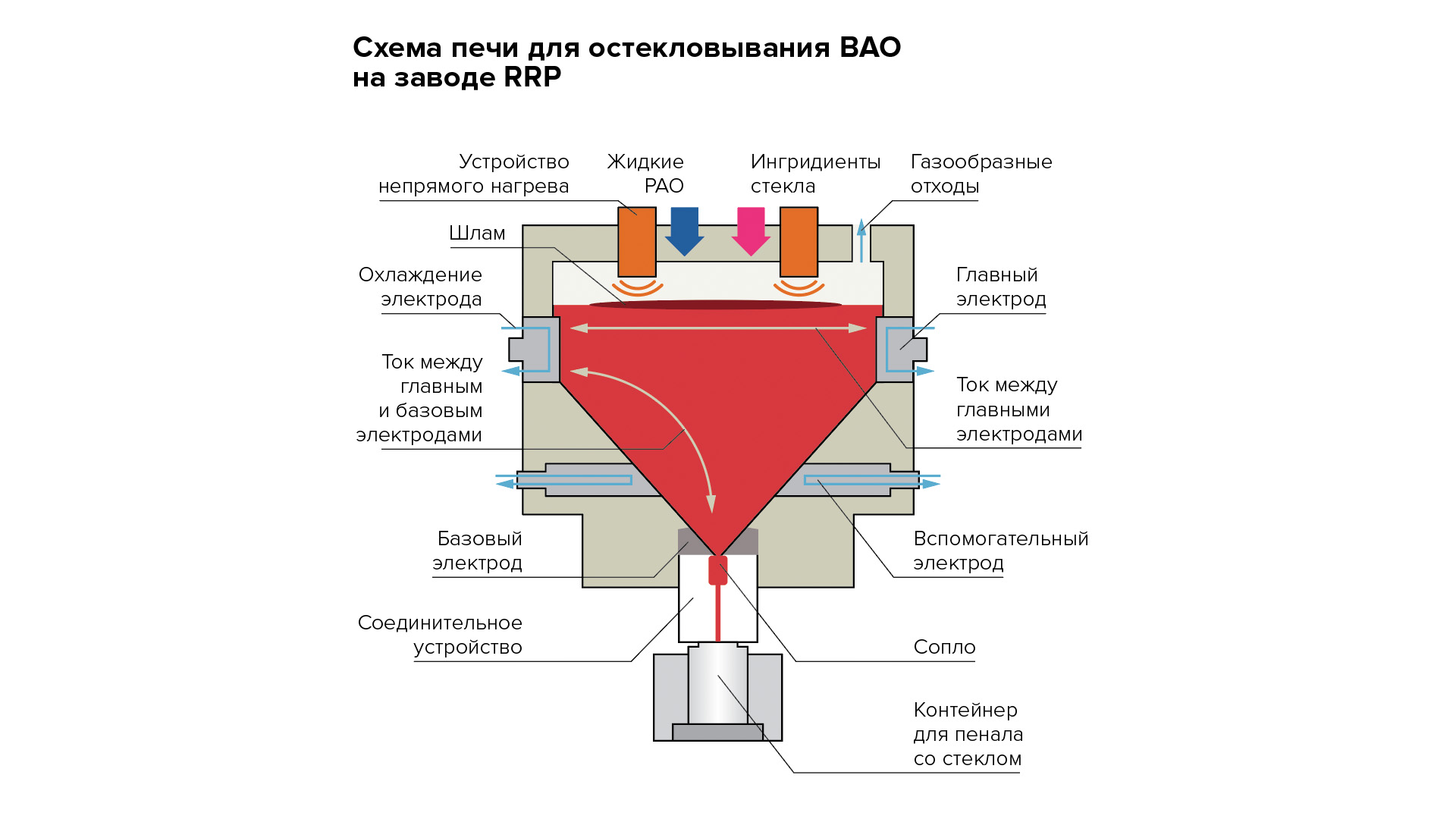
Индия: ориентация на собственные технологии
Особенностью ядерной энергетической политики Индии является ориентация на собственные энергоресурсы и на топливный цикл с использованием как традиционного уранового или уранплутониевого топлива, так и топлива на основе тория и 233U. В перспективе индийские власти нацелены на реализацию ториевого ядерного топливного цикла, так как в стране есть большие запасы монацитового песка — минерала, содержащего фосфаты редкоземельных металлов, а также торий и уран.
Первый индийский завод по переработке ОЯТ был построен в 1965 году в Тромбее. Через восемь лет он был выведен из эксплуатации из-за коррозии оборудования, а в 1982 году снова заработал. После реконструкции на нем перерабатывается ОЯТ исследовательских реакторов, расположенных на той же площадке. Здесь также производят ториевое и МОКС-топливо.
В 1982 году на площадке в Тарапуре состоялся пуск второго радиохимического предприятия, предназначенного для переработки топлива энергетических реакторов. Проектная мощность завода составляла 100 тонн ОЯТ в год, однако по разным причинам его реальная загрузка не превышала 20%. В конце 2010 года завод прошел капитальную реконструкцию, а в январе следующего года была введена в эксплуатацию вторая очередь предприятия.
В 1996 году состоялся пуск радиохимического завода в Калпаккаме недалеко от Центра ядерных исследований имени Индиры Ганди. Его проектная мощность составила 100 тонн ОЯТ в год.
Топливо, получаемое на индийских заводах, предназначается, в частности, для строящегося реактора на быстрых нейтронах. Эксперты прогнозируют, что в будущем ядерный парк Индии вырастет в несколько раз, и это поставит новые задачи по переработке ядерного топлива. Поэтому на площадке в Тарапуре строится завод INRP (Integrated Nuclear Recycle Plant), который в Индии считают предприятием с большой производительностью — до 600 тонн ОЯТ в год. На нем, возможно, будет перерабатываться топливо из быстрых реакторов.
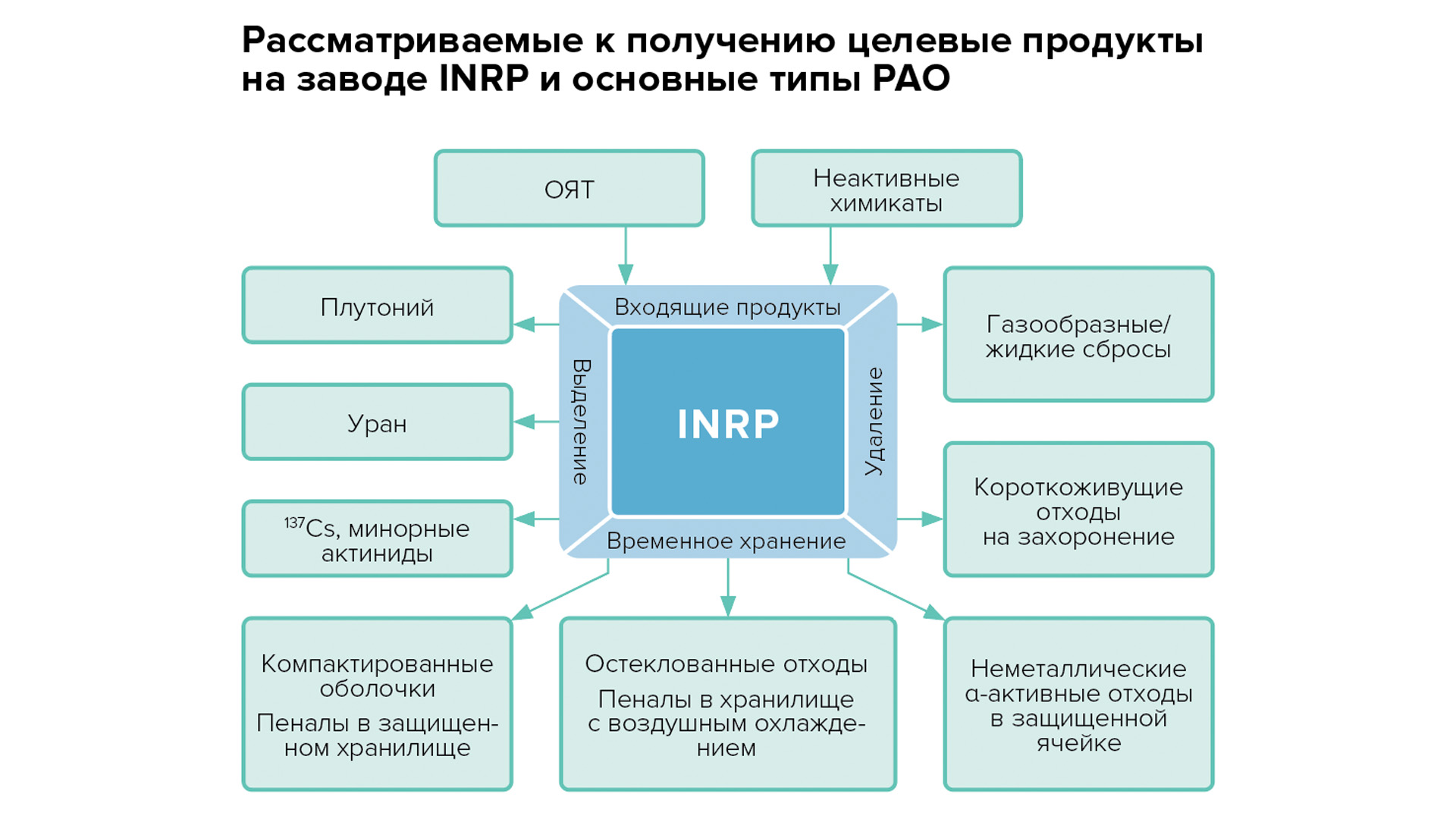
Завод INRP интересен и тем, что на нем будут использоваться технологии переработки и обращения с радиоактивными отходами, разработанные в Индии самостоятельно. В проект заложена концепция, по которой оборудование и системы комплекса сгруппированы по их назначению. Например, все испарители устанавливаются в отдельном блоке испарителей. Блочный подход, подразумевающий разделение по процессам, вынос общих служб отдельно от основных зданий, модульный принцип проектирования, обеспечение возможности быстрого дистанционного ремонта и замены деталей оборудования, единый пульт управления комплексом, учет обратной связи от персонала — все это должно дать экономические и технологические преимущества в работе предприятия. Подход позволит сократить общую площадь комплекса и количество персонала, даст возможность привлечения сотрудников для некоторых работ на аутсорс, снизит капитальные затраты при строительстве.
Важная составляющая комплекса — промежуточное хранилище ОЯТ открытого типа. Оно, кроме прочих мер безопасности, включает защиту от землетрясений. Все манипуляции с ОЯТ будут проводиться под водой, а специальные галереи вокруг хранилища будут удерживать уровень грунтовых вод ниже уровня дна хранилища.
Также в комплексе будет реализована инновационная схема прямой подачи топливных элементов из бассейна в горячие камеры, не требующая промежуточных операций с загрузкой и выгрузкой их из контейнеров. Для этой цели предусмотрен подземный тоннель, который будет соединять бассейн и горячие камеры. Вагонетки с ОЯТ будут двигаться по тоннелю и управляться дистанционно.
Разделка отработанных твэлов будет происходить за один проход, а не за несколько, как на остальных индийских заводах. При этом разделочное оборудование будет обслуживаться, ремонтироваться и заменяться без использования ручных операций.
Для обращения с отходами на заводах построены установки для битумирования и остекловывания. В 2006 году в Тарапуре был возведен комплекс для иммобилизации высокоактивных отходов, на котором впервые применили керамический плавитель, который позднее стали использовать и на других предприятиях.
Для изучения решений по переработке ториевого топлива в Индии был создан стенд UTSF (Uranium Thorium Separation Facility). В нем на переработку поступает оксидное ториевое топливо, а процесс предусматривает выделение всех трех компонентов (урана, плутония, тория) переходного этапа от уранплутониевого к торий-урановому циклу.
Азия развивается, Европа закрывается
В Китае функционирует опытный завод по переработке ОЯТ мощностью 50 тонн в год. Он располагается в провинции Ганьсу, рядом с ним находятся два промежуточных мокрых хранилища на 500 и 800 тонн.
В 2020 году в той же провинции завершилось строительство площадки для мокрого хранения ОЯТ вместимостью 1200 тонн. Планируется, что оно будет принимать ежегодно 200 тонн отработавшего топлива. Также Китай анонсировал строительство хранилища бассейнового типа вместимостью 6000 тонн.
Кроме того, в стране ведется строительство новых предприятий по переработке ОЯТ. Так, в 2015 году началось сооружение демонстрационного завода с проектной мощностью 200 тонн в год. Предприятие возводится по собственным разработкам в Промышленном парке ядерных технологий CNNC неподалеку от хранилища ОЯТ. Предполагается, что он начнет работать уже в нынешнем году. По данным СМИ, также ведется строительство второго завода на той же площадке с такой же производительной мощностью. Ввести в эксплуатацию второй завод китайские власти предполагают после 2030 года.
Планируется, что продукты экстракции китайского завода будут использоваться в качестве топлива для исследовательского реактора с быстрым спектром нейтронов и натриевым теплоносителем.
Еще в 2007 году компании Areva (ныне Orano) и CNNC вели переговоры по строительству предприятия по переработке ОЯТ и производству МОКС-топлива с объемом перерабатываемого топлива в 800 тонн в год. Однако за последние пять лет в открытых источниках не появлялась информация об этом проекте. Похоже, что переговоры, длившиеся около 10 лет, не продвинулись дальше меморандумов.
В области захоронения радиоактивных отходов Китай использует смешанную схему. Жидкие низкоактивные отходы битумируют, а твердые среднеактивные сжигают, цементируют и захоранивают.
Сейчас в стране запланировано создание пяти площадок для захоронения низко- и среднеактивных отходов. В настоящее время функционируют три пункта: в Северо-Западном, Юго-Восточном и Юго-Западном регионах. Суммарная их проектная вместимость — 460 тыс. м3. В 2022 году завершено строительство первой очереди централизованного пункта для размещения отходов в провинции Ганьсу. Его планируемая вместимость — 1 млн м3.
В Южной Корее была создана экспериментальная установка PRIDE, основанная на электрохимической переработке ОЯТ путем электролиза. На основе результатов, которые будут получены при эксплуатации установки, планировалось построить коммерческое предприятие по пирохимической переработке отработавшего ядерного топлива мощностью 100 тонн в год.
Европейские страны, принявшие решение отказаться от атомной энергии или ограничить ее использование, в основном решают задачи по обращению с отходами. Активные работы по этому направлению остались в прошлом веке.
Кроме представленных выше заводов в Великобритании и Франции, в Германии для переработки ОЯТ в Карлсруэ была построена экспериментальная установка WAK мощностью 35 тонн топлива в год. Ввод в эксплуатацию установки WAK состоялся в 1971 году, а за 19 лет ее эксплуатации было переработано 208 тонн ОЯТ, выделено более 1 тонны плутония и произведено около 60 м3 высокоактивных отходов, которые постепенно охлаждались в резервуарах из нержавеющей стали.
На заводе EUREX, построенном в Италии в 1970 году, перерабатывалось топливо двух типов: высокообогащенное уран-алюминиевое топливо с исследовательского реактора и низкообогащенное топливо с АЭС «Латина». Общая рабочая загрузка завода составляла 26 тонн ОЯТ в год. Однако в 1984 году предприятие было закрыто. В результате его деятельности осталось еще 2600 м3 твердых радиоактивных отходов. Окончательный вывод завода из эксплуатации планируется в 2028–2032 годах.
В 2015 году началось строительство объекта Cemex для жидких радиоактивных отходов. Предполагается, что на нем будет переработано около 260 м3 отходов, которые затем будут цементированы. Окончательно их планируется переместить в Национальный центр хранения радиоактивных отходов, когда тот будет построен.
Итак, подводят итог авторы исследования, зарубежный опыт переработки ОЯТ, с одной стороны, показывает, что эти технологии хорошо изучены и активно используются на промышленном уровне. С другой стороны, видно, что для бесперебойной и безаварийной работы предприятий нужны дополнительные исследования и усовершенствования технологических процессов и оборудования.
Французский опыт показал, что последовательное освоение технологий, учет эксплуатации предыдущих производств, создание лабораторных моделей и полномасштабных макетов для новых технологий стали эффективными стратегиями в развитии переработки ОЯТ. Они позволили за относительно короткий срок построить и ввести в эксплуатацию завод UP3 и обеспечить его безаварийную работу и долговечность используемого там оборудования.
Такой подход поможет избежать ненужного консерватизма при проектировании новых заводов, что положительно повлияет на финансовые и временные затраты при их строительстве. При этом необходимо учитывать, что недостаточное изучение влияния даже относительно небольших изменений на уже используемые процессы может привести к ухудшению работы оборудования или даже к невозможности его использовать в дальнейшем.
Особенно актуальным данный подход будет в случае создания инновационных перерабатывающих производств, основанных на технологиях, которые ранее не применялись в промышленных масштабах, а также при проектировании и сооружении заводов, единичная мощность которых значительно превышает аналогичные объекты, находившиеся в эксплуатации ранее.
1. Вахрушин А.Ю., Квятковский С.А., Пономарев А.В. Технологические решения и процессы, используемые на зарубежных предприятиях по переработке ОЯТ. / Госкорпорация «Росатом», ЧУ «Наука и инновации», ЦАИР. — М., 2024.