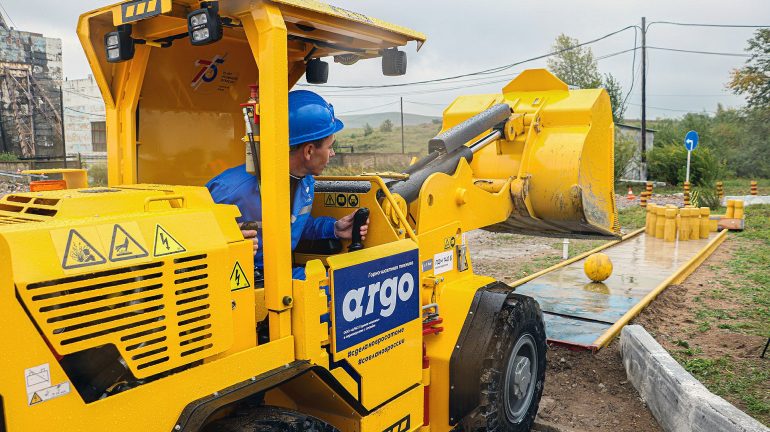
ARGO: начало пути
Производство горно-шахтной техники на ППГХО
ARGO — бренд горно-шахтной техники производства «АРМЗ Горные машины» для горнорудного дивизиона Росатома и других предприятий горнодобывающей отрасли. Первый проект молодого предприятия — малогабаритная погрузочно-доставочная машина с литийионной батареей. Рассказываем, как было создано серийное производство необходимой горнякам техники.
Выйти из замкнутого круга
Горно-шахтное машиностроение в России испытывает определенные сложности. В числе унаследованных проблем — традиция производить все комплектующие своими силами, отставание в обеспечении качества, консервативность конструкторской школы, недостаточная клиентоориентированность в сервисном обслуживании. Современная причина в том, что рынок машиностроительной продукции поделен крупнейшими мировыми производителями и пробиться туда можно лишь при сопоставимом уровне качества и практичности и меньшей приведенной цене предлагаемых решений.
Цель, которая была изначально поставлена перед «АРМЗ Горные машины», — поиск и реализация лучших технических и организационных решений в области горного машиностроения и технологий горного дела для использования как на внутреннем «атомном» рынке, так и за его пределами. Одна из составляющих этой работы — трансфер передовых технологий для снижения стоимости производимой продукции.
Подробности
В горнорудном дивизионе Росатома была сделана попытка выйти из замкнутого круга, и она оказалась удачной. Одно из предприятий дивизиона — «АРМЗ Горные машины» (самостоятельная производственно-сервисная компания, основанная в 2019 году и реализующая собственные проекты с привлечением мощностей ремонтно-механического завода при ППГХО им. Е. П. Славского) стало оператором проекта по производству погрузочно-доставочных машин.
Узкое место
Технология добычи руды на урановых месторождениях Стрельцовского рудного поля (Краснокаменский район Забайкальского края) такова. В горном массиве выполнены горные выработки (шахты, штольни). В выработку (штрек, идущий по рудному телу) входит буровая установка, с ее помощью бурятся скважины — каналы для зарядов. После подрыва зарядов отбитая взрывом горная масса собирается фронтальными погрузчиками и доставляется до рудоспуска. Там горная масса перемещается на нижний горизонт, где посредством железнодорожной откатки транспортируется до шахтного подъема и выдается на поверхность для обогащения.
Фронтальный погрузчик — одна из важнейших машин в такой технологии. Погрузчики, как правило, за пять лет вырабатывают ресурс полностью (такова мировая практика). Запрос на машины с нужными характеристиками для ППГХО был, а соответствующее предложение российской промышленности отсутствовало. Отечественные крупногабаритные погрузчики на рынке есть (их производят для наземных дорожных и строительных работ), но малогабаритная шахтная машина не освоена. Она нужна в небольшом сегменте рынка, хотя спрос постепенно растет: по мере исчерпания месторождений уменьшается сечение выработки, и становятся востребованы узкозахватные самоходные машины. Краснокаменское месторождение урановой руды тоже относится к узкожильным — большое сечение забоя там нецелесообразно.
«Никогда не прекращайте добычу»
Решение было найдено в локализации производства нужной техники. В качестве технологического партнера была выбрана французская Aramine SAS, производитель узкозахватной шахтной самоходной техники (погрузочно-доставочных машин, шахтных автосамосвалов и самоходных буровых установок). Один из девизов компании — «Никогда не прекращайте добычу» — адресован именно владельцам месторождений, вырабатывающих ресурс. Сотрудничество начали с локализации производства ключевого изделия — мини-погрузчика L140B на электрической тяге от аккумулятора. В ходе переговоров договорились о передаче интеллектуальной собственности — чертежей конструкций рамы и рабочего органа, сборочной документации.
Производство рамных конструкций и финальную сборку «АРМЗ Горные машины» организовали на ремонтно-механическом заводе при ППГХО: там изначально был реализован весь технологический передел для горного машиностроения. Важные комплектующие приобретены у Aramine SAS. Это электроприводы, гидравлика, блоки управления, элементы ходовой части, на первом этапе — аккумуляторная батарея. Закупка по льготной цене обошлась существенно дешевле, чем на открытом рынке. На площадке имеющегося завода производятся все рамные конструкции, козырек кабины, балансир, стрела и ковш, выполняется сборка корпуса, установка комплектующих и пусконаладка. Предприятие получило дополнительную загрузку, можно сказать, второе дыхание.
Клиентоориентированность на практике
Реализовав сборочное производство (по сути, весь корпус) и дополнив его необходимыми комплектующими, предприятие вышло на первую стадию локализации. В серии удалось уменьшить стоимость машины для внешних клиентов примерно на 20% по сравнению с импортной, а также сформировать отраслевой заказ при производстве этих машин для предприятий Росатома. На снижении цены сказались закупка сортового и листового проката на внутреннем рынке, металлообработка, сборка. Предприятие быстро вышло на серийный выпуск — и уже до 25% фронтальных погрузчиков ППГХО произведены на площадке «АРМЗ Горные машины».
По словам председателя совета директоров «АРМЗ Горные машины» Игоря Семенова, испытания и эксплуатация образцов на близлежащем горнодобывающем предприятии Росатома стали важной составляющей успешного выполнения всей задачи. Это клиентоориентированность на практике: немедленная и неформальная обратная связь, учет реальных условий, понимание культуры эксплуатации. В распоряжении молодого предприятия оказался полигон для испытания техники в условиях, максимально приближенных к реальной работе, в непосредственной близости от сборочного производства, в условиях действующего предприятия. Впрочем, и свой полигон тоже потребовался: для обучения водителей. Его «АРМЗ Горные машины» построили вблизи сервисного центра.
Традиционно шахтные погрузчики работали на дизельной или электрической (от сети) тяге. Среди недостатков машин на дизельном приводе — шумовое воздействие, и вибрация от работы двигателя, и не отфильтрованные каталитическим нейтрализатором выхлопные газы, то есть необходимость усиленно вентилировать забой. Кроме того, у дизельных и электрических (работающих от сети) машин намного сложнее вся механическая часть. Уже первый опыт эксплуатации аккумуляторной техники показывает, что это выгоднее, чем дизельный парк. Электропривод и система управления технологичнее, многократно упрощается задача техобслуживания, повышается безопасность, не требуется топливо, сокращается громоздкое и небезопасное хозяйство ГСМ.
Подробности
Победа за аккумулятором
Особенность погрузчика, который освоили на «АРМЗ Горные машины», в том, что он работает на аккумуляторной батарее. Ближайшая задача, которая стоит перед предприятием, — замена одного из дорогих элементов машины, импортной литийионной батареи, на отечественную. Было сформулировано задание для Топливной компании «ТВЭЛ», в контуре которой действует бизнес-интегратор РЭНЕРА, реализующий ноу-хау по разработке и производству литийионных батарей. Эффект ожидается не только денежный: это накопление опыта, повышение компетенций, выход с литийионными источниками питания на новые направления, где нужны аккумуляторные технологии.
Деятельность по переводу оборудования на электротягу поддержана на уровне госкорпорации: экспертный совет Росатома по устойчивому развитию одобрил проект производства и применения аккумуляторной горно-шахтной техники. Этот проект содействует повышению устойчивости в производственной цепочке атомной энергетики: это и снижение углеродного следа, и безопасность шахтерского труда. В перспективе вся эта деятельность сложится в комплексный «аккумуляторный рудник», значимый и за пределами Росатома. Когда производство литийионных батарей как нового продукта будет развернуто для нужд различных потребителей, литий сможет поставлять именно АРМЗ: освоение месторождений этого металла в Мурманской и Иркутской областях — в планах по диверсификации горнорудного дивизиона.
Маршрут проложен
Компания начала серийное производство с выпуска первой единицы в марте 2020-го, но уже есть впечатляющий рост. Выручка 2020 года составила порядка 70 млн руб. — весь заказ забрал ППГХО. В 2021 году объем вырос практически вчетверо, и порядка 40% — заказы горнодобывающих предприятий вне Росатома. Опыт эксплуатации изучают неатомные горнодобывающие компании России и СНГ. Даже при сегодняшнем объеме выпуска предприятие стало лидером производства горных машин на электрической тяге от аккумуляторных батарей.
Игорь Семенов уверен, что не за горами не только полная «электрификация» добычи, но и полноценная цифровая трансформация — переход к дистанционному и затем к роботизированному управлению. Именно появление электропривода и не критичной к обслуживанию батареи позволяет заметно сократить трудоемкость. Уже внедряется комплексное роботизированное решение по быстрой замене аккумуляторов, ее на ППГХО предполагают освоить в течение года.
40%
заказов на погрузчик ПДМ 140 Б производства «АРМЗ Горные машины» в 2021 году — от горнодобывающих предприятий вне контура Росатома
~на 20%
по сравнению с импортной машиной удалось уменьшить стоимость машины для внешних клиентов
~в 4 раза
выросла выручка «АРМЗ Горные машины» от поставок ПДМ 140 Б в 2021 году по сравнению с 2020-м
25%
фронтальных погрузчиков ППГХО произведены на площадке «АРМЗ Горные машины»
Цифры
В дальнейшем можно отказаться и от «пилотирования» с присутствием человека в шахте. Уже сегодня технологии позволяют управлять машиной дистанционно: оператор может действовать из безопасного пространства, получая информацию на монитор, и находиться даже за много километров от предприятия. Для освоения дистанционных, а затем и беспилотных технологий (когда человека заменит алгоритм) нужна системная работа: качественная цифровая связь в шахте, сканирование пространства и построение цифровой модели, установка меток. Все эти технологии, включая решения искусственного интеллекта, уже существуют. Но роботизировать рудник, собрав весь этот «пазл» воедино, можно лишь совместными усилиями заказчика, производителей техники и ИТ-специалистов. Это нелегко: горное дело консервативно, инновации происходят медленно. Именно со стороны заказчика должна возникнуть воля к работе с представителями ИТ-отрасли; также и специалисты в области ИТ должны быть способны и готовы вникнуть в сложности освоения подземного пространства. Именно кадровый аспект всей задачи — наиболее сложная составляющая подобных проектов. Подкрепленная аргументами оценка: на пилотный проект «безлюдного» рудника нужно примерно два года. Реализованный в Краснокаменске проект не претендует на полную «перезагрузку» горно-шахтного машиностроения, однако тенденция освоения аккумуляторной техники, а в перспективе и полноценная цифровая трансформация горного дела — очевидны.