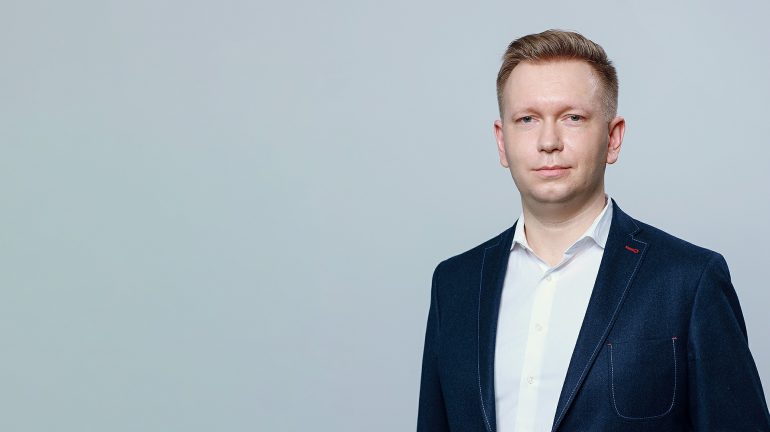
«Мы видим возможные зоны роста»
Юрий Свистунов — о ближайших задачах и стратегии компании «Юматекс»
Заместитель гендиректора — технический директор «Юматекса» Юрий Свистунов был приятно удивлен тем, что в России работают производители оборудования, с которыми можно собрать технологическую линию для производства премиальных углеродных волокон. Российское оборудование — часть стратегии компании и новые технологические конкурентные преимущества в глазах потенциальных потребителей как на внутреннем рынке, так и на зарубежном.
— Юрий Сергеевич, для начала расскажите, пожалуйста, коротко, как развивалась компания.
— Компания «Юматекс» — это композитный дивизион в структуре Росатома численностью более 1500 человек. Исторически деятельность в области углеродных волокон началась в рамках процесса консолидации производств ядерного топливного цикла «Техснабэкспорта». По заказу «ТВЭЛ» мы разрабатывали новые типы углеродных волокон для роторов центрифуг, начали их выпускать для Топливной компании, потом ими заинтересовались представители других отраслей. Позже, в рамках «Юматекса», эта деятельность превратилась в полноценный интегрированный бизнес, который начинается от сырья для углеродных волокон и заканчивается конечными изделиями — композитами. Благодаря запуску производства углеродного волокна в Алабуге мы смогли сформировать линейку продуктов, с которой вышли на внешние рынки. Нас стали узнавать, упоминать в профильных журналах, которые формируют аналитику по этому направлению.
Одновременно мы смогли стать интересными и для «ТВЭЛ», поскольку добились — в том числе с помощью их специалистов — интересной для них цены и предложили несколько типов углеродных волокон, которые смогли заменить импортные аналоги. А благодаря запуску собственного завода по производству ПАН-прекурсора мы разрабатываем так называемое среднемодульное высокопрочное волокно, которое позволит нам заместить лучшие образцы зарубежных конкурентов. Полтора года назад мы получили образцы таких материалов в лабораторных условиях, в прошлом году мы выпускали опытные партии, «ТВЭЛ» подтвердил их свойства. Теперь наша задача — довести технологию до промышленных масштабов и стабильных показателей.
В целом мы решаем задачи не только отрасли, но и всего композитного направления в России. Мы начали с продуктов на основе углеродного волокна, но сейчас мы также работаем со стекловолокном, есть партнерские продукты с другими типами наполнителей. Мы работаем в таких отраслях, как строительство, авиация, спортивное оборудование, атомная энергетика.
— Конкурентов много?
— Меньше 20 компаний — думаю, не так много, как в сегментах других материалов. Из них 10–12 очень серьезных. Они исторически превосходят нас по объему производства, по амбициям, по возможностям, потому что у нас все-таки небольшой объем производства. Кроме того, появляются, в основном на азиатских рынках, новые конкуренты.
— Какова производственная мощность линий «Юматекса»?
— У нас одна линия, рассчитанная на выпуск 1000–1200 тонн в год. С учетом того, что в мире выпускается порядка 100 тыс. тонн волокна в год, мы занимаем 1%. В полуфабрикатах, то есть материалах на основе волокна, наш процент выше, потому что у нас высокий уровень собственной переработки.
— Какова доля «ТВЭЛ» в структуре заказов на волокно?
— 10–11% в деньгах и чуть больше 12% в объеме.
— Если у вас одна линия по производству углеродного волокна, то вам приходится переключаться с одного вида на другой. Как это влияет на стабильность?
— Одна высокопроизводительная линия — ключевой недостаток нашего производства в Алабуге. У него два аспекта. Первый — гибкость. Мы не так гибки, как некоторые наши конкуренты, которые выпускают каждый тип углеродного волокна на отдельной линии. Это — непроизводительное время на перезаправки и переналадки, лишние отходы, в какой-то степени и стабильность работы. Второй аспект — это надежность оборудования. Для нас это сейчас большая головная боль и объект активного развития новых инвестиционных проектов. Оборудование технически сложное, наукоемкое, склонное к тому, чтобы выходить из строя. А когда на нас рассчитывают «ТВЭЛ», авиация и стратегические отрасли, которые у нас сейчас в приоритете, поскольку линия одна, мы не можем себе позволить незапланированную остановку. Поэтому мы много тратим на то, чтобы обеспечить надежность всеми способами — это и увеличенный объем запчастей, и программные продукты для предсказывания отказов, и организация увеличенного объема планово-предупредительных работ. Эти траты «ложатся» в себестоимость продукции, поэтому возникает вторая проблема — необходимость сдержать ее рост.
— Как можно решить эту проблему?
— Надо строить новые линии. Но делать это затруднительно, потому что оборудование, которое мы использовали для линии по производству углеродного волокна, в основном иностранное – из Германии, Италии, Великобритании. А сейчас международные партнеры, мягко говоря, охладели к сотрудничеству.
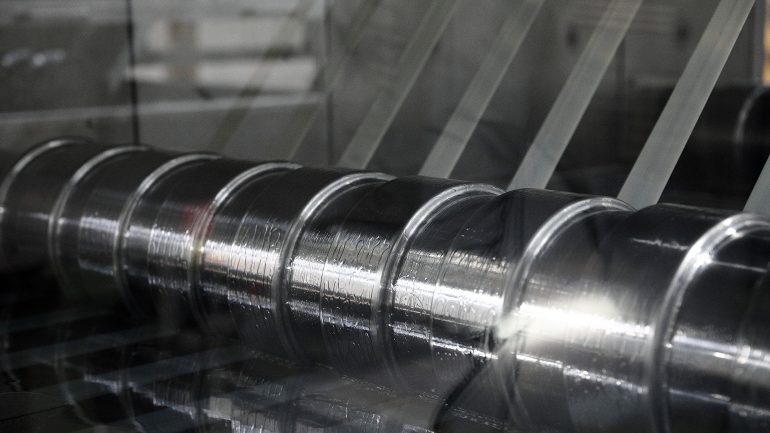
— Переход на отечественное оборудование реалистичен?
— Мы над этим работаем, причем начали не с февраля. Мы к этому готовились, потому что для нас российское оборудование — очередной качественный этап развития. Наша идея для одного из проектов, который мы уже активно реализуем, заключается в том, чтобы создать в России цепочку кооперации и, возможно, компанию, которая бы интегрировала решения по нестандартному оборудованию для производства углеродного волокна, отвечала бы за определенный уровень качества, который мы можем сверить с тем, которое мы получаем на существующей линии. Конечная цель кооперации в том, чтобы выпускать полностью отечественное оборудование и составить в среднесрочной перспективе конкуренцию западным производителям оборудования, которые уже работают на рынке.
— Где вы сейчас на этом пути?
— Проведя предварительную работу, мы, к своему удивлению, довольно быстро нашли тех, кто способен участвовать в создании комплекта оборудования для композитной отрасли. Почти не осталось узлов, которые мы не можем заместить. До конца этого года мы будем строить макет одной из ключевых печей для производства углеродного волокна и проверять, как она работает и насколько наши идеи и решения воплощаются «в железе». Конечная наша цель — построить еще одну линию по производству углеродного волокна, которая возьмет на себя задачи стратегических заказчиков. Предположительно, ее производительность будет на уровне 60–70% от производительности нашей первой линии.
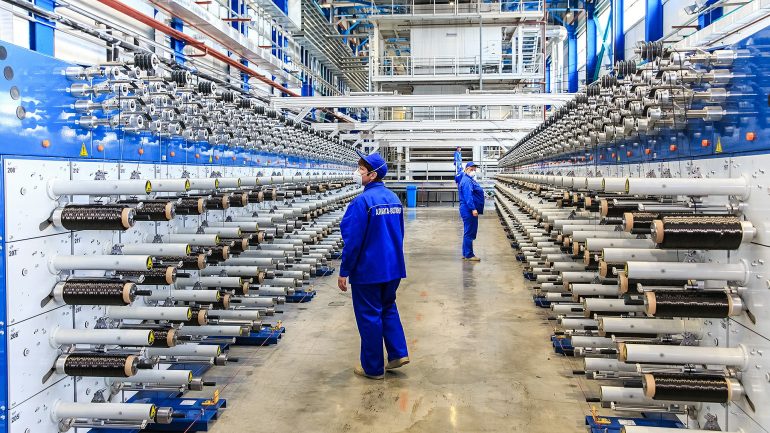
— То есть около 600–800 тонн в год?
— Да, примерно так. Линия должна обеспечить надежность производства и стабильность поставок углеродного волокна специальных номиналов. Плюс еще такой момент: наши заказчики из высокотехнологичных отраслей хотят, чтобы оборудование было изготовлено на отечественной линии, потому что современное оборудование оснащено системами управления. Это значит, что зарубежное оборудование может управляться извне и в работе могут быть намеренно созданы ошибки. В российском оборудовании вероятность таких отказов минимальна. С другой стороны, требуется время на то, чтобы прийти к тому же уровню качества, к которому шли наши зарубежные коллеги в течение десятилетий. Тем не менее мы в этот проект идем, и я надеюсь, что в ближайшие несколько лет мы такую линию создадим.
— В чем именно проблема? Сложно повторить?
— Наоборот, повторять нельзя. Приведу такой пример: одна из ключевых печей — это печь окисления, или, иначе, термостабилизации. В ее конструкции заложены несколько десятков патентов немецкого производителя, который поставил ее «Юматексу». Наша задача заключается в том, чтобы создать свою печь, не нарушив ни один из этих патентов, потому что мы все-таки ответственная компания, входим в Росатом. А Росатом — это глобальный технологический лидер, он не может себе позволить просто дублировать образец, хотя и такая практика в мире есть. Поэтому мы должны что-то новое в каждом из этих узлов придумать — это первая задача. Вторая задача — сделать так, чтобы печь работала лучше, чем образец, чтобы затраченные усилия были оправданны. И третья задача — печь должна быть надежной, удобной и обеспечивать выпуск продукции должного качества при том, что у нас — и этого нельзя отрицать — есть проблемы с подготовкой и квалификацией инженеров, конструкторов, да и оборудованием для производства углеродного волокна они никогда раньше не занимались.
— Каков ориентир по срокам создания оборудования?
— Построить новую производственную линию, если есть доступ к оборудованию, возможность провести конкурс и выбрать лучшие образцы, заключить контракты можно за 3,5–4 года. Когда нужно оборудование разрабатывать и делать что-то, чего еще не было никогда, скорее всего, срок будет увеличен на полгода-год.
— С момента создания макета пройдет года полтора-два?
— Не так. В этом году мы строим макет, в 2023 году — промышленную печь, затем еще год — на создание полного участка производства.
— То есть к концу 2024 года у вас будет полный участок производства, верно?
— Да. Причем параллельно мы будем создавать не один участок, а восемь — все элементы непрерывной линии по производству углеродного волокна. Это подача прекурсора, термостабилизация, карбонизация, транспортировка волокна, электрохимическая обработка, поверхностная обработка и намотка, система нейтрализации продуктов пиролиза и возврата тепла в технологию. Мы планируем получить опытные образцы, а затем и промышленные на каждом переделе и в финале процесса сформировать полную производственную линию.
— То есть в конце этого года будет не один макет, а восемь?
— Все макеты в этом году не получится сделать, что-то перейдет на следующий год, какое-то оборудование будет разрабатываться сразу в промышленном размере. Но главное, что для каждого участка мы нашли партнеров, которые готовы с нами сотрудничать, и у них есть нужные компетенции.
— Назовите, пожалуйста, участников кооперации.
— Пока не могу, мы заключили соглашения о неразглашении. Могу только сказать, что «ТВЭЛ» в том числе заинтересован участвовать как разработчик и поставщик оборудования, перечень мы уже обсуждаем. Надеюсь, что они в этой цепочке кооперации сыграют важную роль. Я больше удивился тому, что в России в целом не так уж все и плохо с машиностроением. Есть целый пласт достаточно эффективных компаний с оборотом 200–400 млн рублей, небольшой командой — как правило, это семейные компании либо компании, основанные группой хороших знакомых, — которые давно существуют (некоторым больше 20 лет) и выполняют заказы для крупных игроков, в том числе для Росатома.
— Если в 2024 году вы сформируете восемь участков, то когда появится вся линия?
— Наверное, в 2025–2026 годах.
— Можно ли сократить этот срок?
— Даже «мастера спорта» в нашем сегменте не смогут построить производство меньше чем за три — три с половиной года. Просто потому что срок изготовления ключевого оборудования — полтора года, и его не сократить, потому что заказы выстроены в плотную очередь.
— Вторая линия будет установлена на той же площадке, что и первая?
— Да.
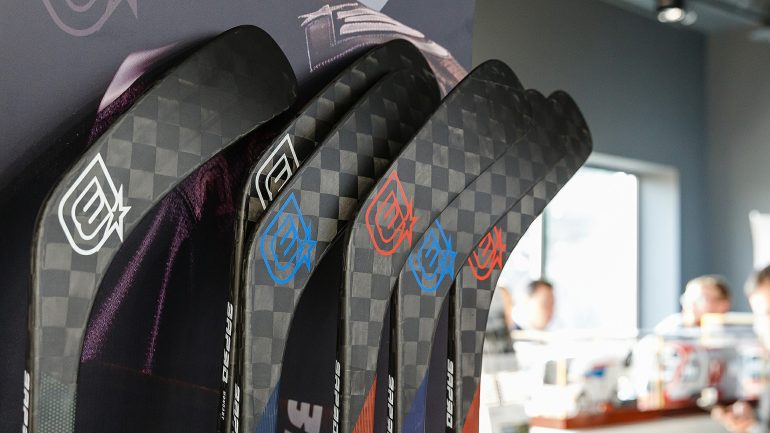
— Этого достаточно? Может, для клюшек надо одну линию, для крыльев — другую, а для центрифуг — третью?
— Принцип сегментации не продуктовый. Углеродное волокно с одними и теми же характеристиками может применяться и для клюшки, и для крыла самолета.
— Серьезно? У нас клюшки из тех же композитов, что и крылья самолетов?
— Да, может так быть. Только надо учитывать, что у авиаторов и конструкторов газовых центрифуг требования к отклонениям гораздо строже. Они проверяют в первую очередь коэффициент вариации основных характеристик от партии к партии и меняются ли они вообще. В производстве клюшек уровень приемки и количество испытаний волокна перед применением гораздо ниже. Конечно, отличия в производстве есть, но по сути производство продуктов очень похоже. Другое дело, что мы сейчас работаем над созданием следующих поколений углеродного волокна, поэтому линии будут разделены по их типам. На новой линии, например, будут выпускаться только волокна тонких номиналов, которые применяются в авиации и специальных сферах. А на большой линии можно выпускать углеродное волокно для широкого рынка — строительства, спорта, баллонов высокого давления и лопастей для ветростанций.
— А волокно для центрифуг где будете производить?
— Скорее всего, на новой линии. Мы рассчитываем, что новое волокно будет востребовано в «ТВЭЛ», где отбор самый строгий среди всех наших потребителей.
— Что происходит, если продукция некачественная? Ее перезапускают на повторное производство или это уже брак и отходы?
— Волокно можно отправить менее требовательным потребителям. Отходы, кстати, одна из проблем композитного производства. Они накапливаются, потому что и связующие, и само углеродное волокно практически не подвержены коррозии, гниению и другим разрушающим процессам. Поэтому мы запустили еще в позапрошлом году проект «Рециклинг».
— В чем его суть?
— Разработка технологий переработки. Мы берем углепластики, сортируем их, термически перерабатываем, удаляем связующее. Остается углеродное волокно, которое мы измельчаем, а затем используем для производства углепластиков другими методами. Например, методом объемного армирования. Таким способом делают, например, корпуса ноутбуков. Под верхним слоем вашего ноутбука находится черный материал из пластика, наполненного рубленым углеродным волокном. Механические свойства его те же, что у обычного пластика, но процесс производства гораздо дешевле. Если вы используете вторичное волокно, его стоимость очень низкая.
— А производители лопастей утверждают, что переработка дорогая.
— Они работают со стеклопластиками, у углепластиков не так. Углеродное волокно стоит дорого по нескольким причинам. Первая причина — сырье. Цепочка технологического производства углеродного волокна начинается с акрилонитрила. Это рыночный товар, его выпускают лишь несколько компаний в мире, один из мировых лидеров — это «Лукойл». Цена акрилонитрила зависит от цены пропилена, которая, в свою очередь, зависит от цены нефти. То есть цена колеблется в зависимости от рыночных тенденций, но очевидно, что акрилонитрил не может стоить очень дешево. Он перерабатывается в полиакрилонитрил, затем в углеродное волокно и материал на основе углеродного волокна по технологиям, очень похожим у всех производителей в мире. Они энергоемкие, наукоемкие, но принципиально между ними не пропасть. Все понимают, сколько конкурент тратит на каждый передел. Поэтому углеродное волокно не может стоить меньше 12 долларов за килограмм — это нижний предел. Но волокно для массовых применений не может стоить и дороже 30–40 долларов за килограмм, просто потому что так резко не скачет цена на акрилонитрил.
Такая ситуация на рынке наблюдается в течение последних 20–30 лет. Были, конечно, случаи, когда крупные японские производители манипулировали рынком и искусственно повышали или снижали стоимость углеродного волокна для того, чтобы достигать своих целей. Но в целом цена углеродного волокна варьируется в довольно узком диапазоне, и его границы сложно раздвигать. Когда же вы берете углеродное волокно из отходов, вы в качестве сырья используете то, что, скорее всего, было бы выброшено и что имеет почти нулевую стоимость. Есть даже случаи, и мы в одной из таких цепочек участвовали, когда тот, кто забирает композитные отходы, еще и получает деньги от того, кто их ему отдает для переработки. Конечно, переработка — пиролиз, затраты на персонал и прочее — стоит денег, но это не очень дорого. То есть можно теоретически получить углеродное волокно с себестоимостью в три-четыре раза дешевле исходного.
— А связующее куда уходит?
— Оно превращается в газообразные продукты, которые технологически легко довести до предельных оксидов азота и углерода. Конечно, это углеродный след, но гораздо хуже, если композиты будут накапливаться в непереработанном виде.
— Какой у вас объем производства в сегменте переработки?
— Мы пока создаем опытную линию, перерабатываем, испытываем продукты на основе переработанного волокна. Определенные успехи у нас есть, некоторые заказчики уже готовы покупать эти материалы. Для нас это, с одной стороны, не основной бизнес, с другой, он хорошо укладывается в деятельность Росатома в области устойчивого развития.
— Кто потребители таких композитов?
— Основные покупатели — производители теплоизоляции и нетканых материалов, которые, в свою очередь, используются для разных целей, например для изготовления автомобильных панелей. Для автопроизводителей цена на композиты крайне важна с точки зрения их собственной себестоимости. Они не возьмут материал, если он не будет стоить дешевле металла.
— Вы — потенциальные поставщики материалов для электромобилей?
— Да, их производители — очень важные для нас будущие заказчики, мы на них делаем большую ставку. Применений достаточно много: можно делать конструктивные элементы, элементы корпуса или целый кузов. У BMW i8 монокок сделан из углепластика, причем не из волокна аэрокосмического назначения. Они для производства углепластика именно для этой модели целый завод по производству углеродного волокна в Америке построили в кооперации с одним из японских производителей. Насколько я знаю, он работает.
— Вы готовы двигаться в этом же направлении?
— Да, но поскольку у нас рынок не очень большой, даже если мы все отходы будем перерабатывать, то не станем крупным поставщиком. Поэтому мы обсуждаем вопрос с одним из китайских производителей углепластика, чтобы получать их отходы.
— А почему схема по вторичному использованию композитов не работает для стекловолокна?
— Стекло стоит дешевле, чем продукт переработки. Лимитирующий фактор — стоимость пиролиза, который дороже стекла.
— Вы говорили, что производственная мощность действующей линии «Юматекса» — около 1 тыс. тонн. А какова емкость российского рынка?
— Когда мы выходили на рынок, она составляла около 300 тонн. Сейчас побольше, около 500. Часть выпускаемой нами продукции в прошлые годы шла на экспорт.
— Каковы перспективы российского рынка?
— Они связаны с авиацией. Она развивается, производители требовательные. Все эти десятилетия, вопреки расхожему представлению, наши авиастроители не бездействовали, а серьезно развивались в сторону композитных материалов. Российские композитные решения на очень продвинутом уровне находятся, наши не отстают от западных коллег. Про МС-21, конечно, все уже говорят, и я считаю, что это действительно хороший, очень интересный проект с технологической и технической точек зрения. Тем не менее российский рынок не безграничен, как бы он быстро ни развивался, поэтому нам надо позиционировать себя как глобального игрока.
— Что вы поставляете на экспорт?
— Мы стараемся не экспортировать углеродное волокно, потому что это невыгодно. На экспорт мы стремимся поставлять полуфабрикаты: ткани, препреги, а также конечные изделия. Это более маржинальные продукты, которые позволяют нам развивать бизнес.
— Куда экспортируете?
— В Китай, где до сих пор дефицит углеродного волокна и рынок растет. Китай готов покупать все: и волокно, и полуфабрикаты, и изделия. На втором месте была Европа. Сейчас работаем над тем, чтобы проверить потенциал других рынков.
— На арабский рынок выходили?
— Да, но там ситуация специфичная: арабский рынок вроде бы стремится к тому, чтобы открыть для себя баллоны высокого давления, лопасти и другие композитные товары. Интерес вспыхивает, бизнесмены хотят в переработку идти, нефтехимию развивать, начинаются активные разговоры — а потом они угасают. Мы уже несколько таких циклов наблюдали. Тем не менее думаю, что это перспективный рынок.
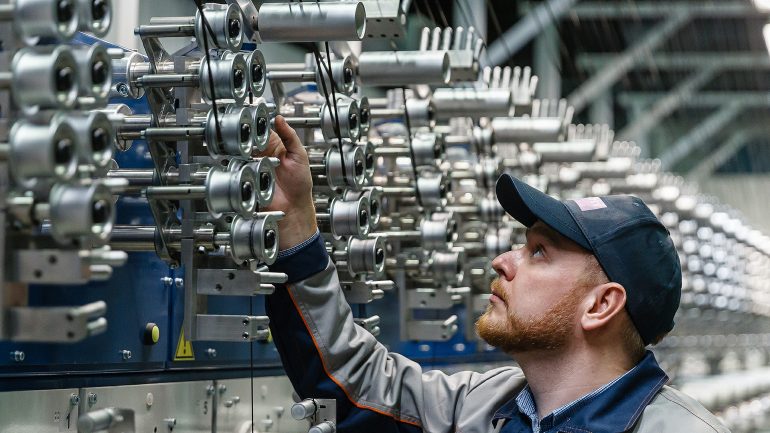
— А в Индии?
— В Индии странная ситуация: огромное население, потенциально огромный рынок потребления композитов, даже на шлемах для велосипедистов и для тех, кто на скутерах ездит, можно было бы гигантский объем сделать. Но почему-то этот рынок даже не начинает расти, текущий объем — лишь 500–600 тонн. Есть несколько госкомпаний, которые постоянно проводят конкурсы на поиск партнеров для создания производства и переработки углеродного волокна, но эти конкурсы, как и в арабских странах, то возникают, то пропадают. Нет компании, которая стала бы лидером на рынке и взяла бы на себя задачу его развить. Думаю, что появление такой компании — вопрос времени, другой вопрос, насколько это время соотносится с продолжительностью жизни. Поэтому мы видим два пути: пытаться искать партнеров там или создавать производство здесь и туда готовые изделия возить. Но далеко, кстати, можно и не ходить. Хороший потенциал у стран СНГ.
— Страны Центральной Азии?
— Да, в этих странах есть остатки советской химической промышленности, современные, активные и достаточно замотивированные люди, чтобы развивать новые технологии. Их, конечно, привлекают высокотехнологичные отрасли, и мы одним из компонентов своей стратегии видим партнерства как зоны возможного роста.