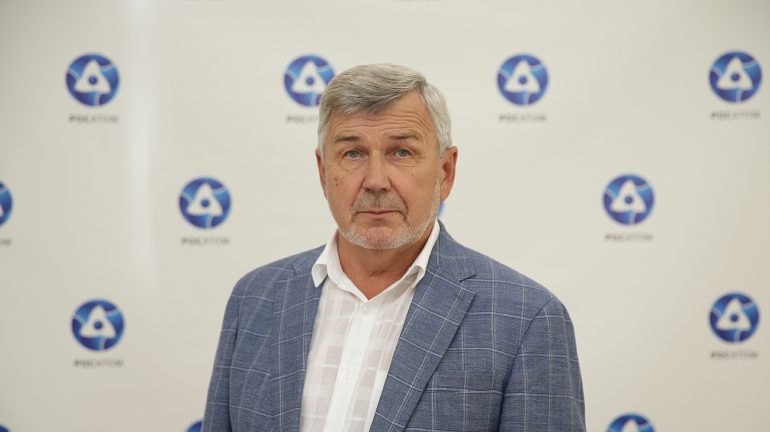
Рассказывает Александр Павелонец
Генеральный директор ООО «УЗГЦ» с 2007 по 2015 год
Теория — одно, а практика — другое
В свою профессию я пришел отчасти случайно, но остался в ней на всю жизнь. Я закончил Омский политехнический институт в 1978 году, распределился на Уральский оптико-механический завод в Екатеринбурге, но по ряду причин уволился через несколько месяцев. Как раз в это время был набор в особое конструкторское бюро приборного завода УЭХК, туда я и поступил в 1979 году старшим техником-конструктором. Своими учителями я бы назвал начальника ОКБ Всеволода Александровича Баженова и своего первого руководителя Семена Семеновича Бабурина. Когда человек приходит на работу после института, он начинает понимать, что теория —это одно, а практика — немного другое, так что они многое мне дали в плане практики и подходов к работе. Я проработал на приборном заводе 21 год, занимался конструированием оборудования для разделительных предприятий: это агрегатированный комплекс средств управления, специализированные преобразователи частоты, стенды для проверки выпускаемого оборудования.
В 2000 году назначен заместителем начальника производственно-технического отдела, который осуществлял управление подразделениями дискретного производства УЭХК. Основная задача дискретного производства — это выпуск оборудования для разделительных предприятий и продукции общепромышленного назначения. В это же время началась работа по организации, разработке и проектированию производства газовых центрифуг на УЭХК. Уральский завод газовых центрифуг (УЗГЦ) был создан в 2007 году согласно приказу Сергея Владиленовича Кириенко, в то время возглавлявшего госкорпорацию «Росатом», о выделении из состава УЭХК производства ГЦ. Структурные преобразования происходили в самый разгар строительства завода, и если посмотреть фотографии того времени, то можно увидеть, что вместо оборудования там был бетон. Я был директором УЗГЦ в период создания и в первые восемь лет работы предприятия.
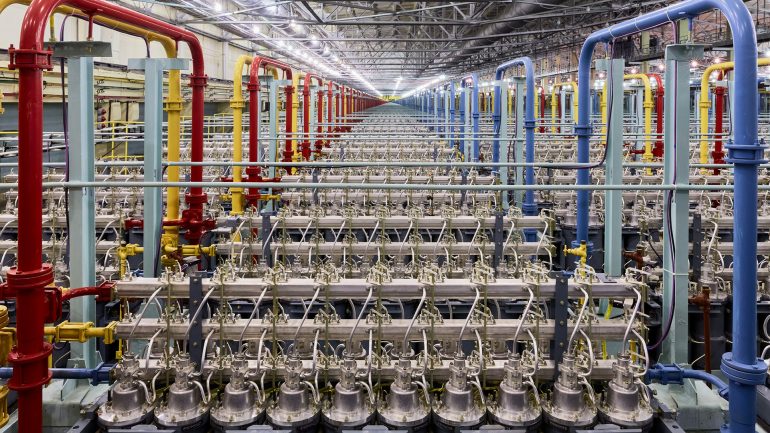
Отвечая на вызовы
С чем было связано решение о создании нового завода? Вопросы отработки технологии и ее соблюдения в условиях массового производства ГЦ являются очень важными и одними из самых сложных на протяжении всего пути создания и эксплуатации любых поколений серийных центрифуг. В связи с этим УЭХК, который тогда выступал в качестве главного конструктора последних двух поколений ГЦ, внес предложение за счет собственных средств создать на базе опытного производства комбината опытно-промышленное производство центрифуг, где опережающим образом отрабатывалась бы не только конструкция машин, но и технология производства, которую затем можно было бы передавать на серийные заводы-изготовители. Это позволило бы решить остро стоявшую тогда проблему качества изготовления ГЦ.
Основные трудности при создании завода были связаны с тремя главными вопросами. Если посмотреть на план УЗГЦ, видно, что завод располагается в нескольких зданиях, поэтому, во-первых, было необходимо таким образом разместить оборудование и выстроить логистику, чтобы обеспечить оптимальное перемещение материалов и комплектующих между разными участками производства.
Второй вопрос касался выбора оборудования. УЭХК был главным конструктором перспективных ГЦ, и если на обычных заводах оборудование предназначалось исключительно для изготовления серийных центрифуг, то для УЗГЦ требовалось оборудование как для серийного производства, так и для изготовления опытных партий перспективных машин. Поэтому оборудование подбиралось исходя из возможности его последующей адаптации к производству новых поколений ГЦ.
Ну и третий важный вопрос — это, конечно, кадры. Завод строился на базе электромеханического завода УЭХК, поэтому специалисты машиностроительных профессий у нас были. Однако мы остро нуждались в специалистах других профессий. Завод почти на 100% оснащен станками с ЧПУ, автоматами продольного точения и другой автоматизированной техникой. Поэтому нам в большом количестве требовались операторы станков с ЧПУ. Для решения этой задачи на базе технологического лицея был создан специальный класс, комбинат оснастил его необходимым оборудованием, и лицей начал готовить кадры для УЗГЦ. Самым трудным было найти специалистов по изготовлению стеклопластиковых изделий намоткой. Такие кадры не готовили ни в технических училищах, ни в лицеях. Поэтому нам пришлось их учить самим, причем прямо на рабочих местах. Набирали группы по 15–20 человек (больше просто не могли) и учили их два-три месяца, после чего они сдавали экзамен на разряд, а мы набирали новую группу.
Самой главной задачей, стоявшей перед нами, было завершение строительства завода и вывод его на проектную мощность. И с решением этой задачи мы справились. Другая важная задача была связана с переводом производства с машин 8-го поколения на изготовление центрифуг 9-го поколения. Для этого требовалось перенастроить все производственное оборудование, ведь новые надкритические машины были технологически сложнее предыдущих, имелись иные требования к балансировке ротора, точности и т.д. Я горжусь тем, что УЗГЦ, несмотря на все трудности, был построен, выведен на проектную мощность, начал производить продукцию и на нем сформировался отличный, слаженный, высокопрофессиональный коллектив.
Идти в ногу со временем
Я считаю, что любому предприятию требуется модернизация, так как оборудование устаревает. Это примерно так же, как если бы вы купили машину и проездили на ней 15–20 лет, после этого запчасти вы на нее уже вряд ли сможете купить. Так и на производстве. На момент пуска завода у нас было самое современное оборудование, какое только сумели в то время найти, и, как я уже подчеркивал, это было оборудование, которое позволяло выпускать не только серийные машины, но и перспективные опытные образцы. На других заводах в те времена такого не было.
На предприятии уже в 2007 году придавали большое значение автоматизации производства, устанавливали станки с ЧПУ, различные роботизированные комплексы. Приведу наглядный пример: у нас был робот для сварки рамы агрегата центрифуг. При кажущейся простоте рама — это довольно сложная конструкция, состоящая из уголков, швеллеров и других деталей. И чтобы ее ровно сварить, нивелируя напряжения, которые возникают при нагреве, нужно использовать сложную программу. Вот это было у нас уже тогда. Или взять другой пример, линию по порошковому окрашиванию. В то время, когда мы строили завод, на многих других предприятиях всё красили пульверизаторами. А у нас операторы только навешивали детали и закрывали те места, которые не надо красить, все остальное делала и делает автоматика. Сначала пассивация, потом сушка, потом окрашивание, потом опять сушка — все это автоматизировано. Также есть полностью автоматизированные станки, где робот берет заготовку, кладет ее на станок и после обработки снимает со станка. Вот это и есть автоматизация.
По сравнению с предыдущими технологиями, газоцентрифужная — не только более экономичная, она еще и позволяет обеспечить комфортные условия работы для персонала. На газодиффузионном производстве очень жарко, а в цехах с центрифугами хорошие условия, прохладно, чисто, гораздо чище, чем в любом механическом цехе. И тихо — только небольшой гул.
Комфортная технология
В те годы, я считаю, у нас был самый современный завод по производству ГЦ, но сегодня ситуация поменялась, ведь существующее оборудование проработало с 2007 года и уже самортизировано. Технологии и промышленность не стоят на месте, появляется более точное оборудование, создаются новые материалы. Так что планы по модернизации, конечно, есть.
Считаю, что самая основная задача сегодня — это обеспечение производства материалами и комплектующими, особенно теми, что раньше закупали за границей. Для этого необходимо наладить это производство у нас. В принципе, это решаемая задача. Хотя это не быстро: ни за день, ни за два, ни за год этого не сделаешь. Но раньше в атомной отрасли использовали только советские комплектующие. Выпускали в советские времена и конденсаторы, и транзисторы, и микросхемы, все это было. Вот этими вопросами сегодня необходимо заниматься.
Рождение «Центротеха»
Монопредприятием завод стал примерно к 2010 году, когда увеличили количество изготавливаемых центрифуг и передали другим предприятиям изготовление оборудования, которое делал в свое время электромеханический завод — запорной арматуры, компрессоров, регуляторов, запасных частей к ним и проч. Став монозаводом, мы проработали так четыре года, но в 2014-м, когда у нас снизились объемы производства центрифуг, пришлось заняться диверсификацией. Первый договор УЗГЦ заключил на разработку и изготовление оборудования для очистительного каскада буровых установок.
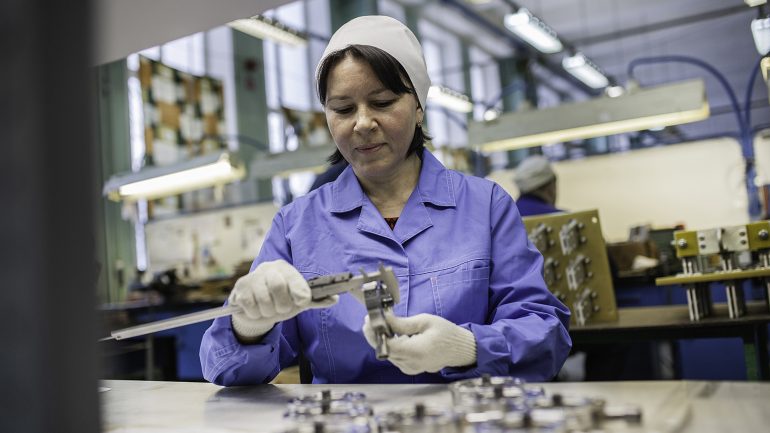
А потом, в 2015–2016 годах, началось объединение предприятий Новоуральской промышленной площадки, когда в УЗГЦ влился сначала Новоуральский приборный завод с производством электротехнического оборудования, потом Новоуральский научно-конструкторский центр с НИОКР по ГЦ, затем Завод электрохимических преобразователей. В итоге было создано Научно-производственное объединение «Центротех». Сейчас это многопрофильное предприятие, которое выпускает не только центрифуги, но и электротехническую продукцию, фильтры, электролизеры и другие изделия, а также занимается разработкой по всему перечню выпускаемой продукции.
Выращивать специалистов
Сейчас я работаю в «дочке» «Центротеха». В 2020 году НПО «Центротех» стало резидентом ТОСЭР — территории опережающего социально-экономического развития. По закону у предприятия — резидента ТОСЭР, не должно быть промышленных площадок на других территориях. Однако Новоуральский научно-конструкторский центр имел филиал в Санкт-Петербурге, а филиалы Новоуральского приборного завода расположены в Зеленогорске и в Ангарске. Пришлось эти филиалы выделять в отдельную дочернюю компанию ООО «Центротех-Инжиниринг», которую я тогда возглавил. Для меня это была примерно та же самая работа, что и на УЗГЦ, с той разницей, что производственные площадки были расположены по всей стране, так что пришлось поездить. Адаптироваться на новом месте работы мне не пришлось, потому что я прекрасно узнал эти площадки и персонал, работая в «Центротехе», не раз бывал там.
Молодые специалисты сейчас приходят к нам в основном после Уральского федерального университета (УрФУ, бывшего Уральского политехнического института — УПИ) и Новоуральского технологического колледжа. И в нашем колледже в Новоуральске, и в УПИ раньше была хорошая подготовка молодых специалистов. Сегодня ситуация несколько изменилась. Я несколько лет проработал в государственной экзаменационной комиссии Новоуральского филиала МИФИ (НТИ НИЯУ МИФИ) и присутствовал на защите дипломов по специальности «мехатроника». Последний раз я принимал дипломные работы у выпускников бакалавриата и видел, что по сравнению с теми, кто заканчивал специалитет, эти выпускники немного «недоученные» — им не хватает знаний, так как они профессию начинают изучать только на третьем-четвертом курсе.
Тем не менее как в свое время наши наставники помогали нам пройти путь от теории к практике, так и сегодня опытные специалисты помогают молодым, так что у нас получается обеспечить преемственность поколений.
А вообще я считаю, что руководителю, прежде всего, нужно быть профессионалом своего дела. Кроме того он должен, во-первых, хорошо относиться к людям и, во-вторых, быть честным перед людьми: если ты что-то пообещал, то должен выполнить. Но и рядовой сотрудник должен на своем месте делать все, что необходимо, принимать решения сам и не бегать постоянно к начальнику за подсказками и наставлениями, то есть должен быть специалистом. Именно так мы сможем решать важные задачи, которые стоят перед отраслью.