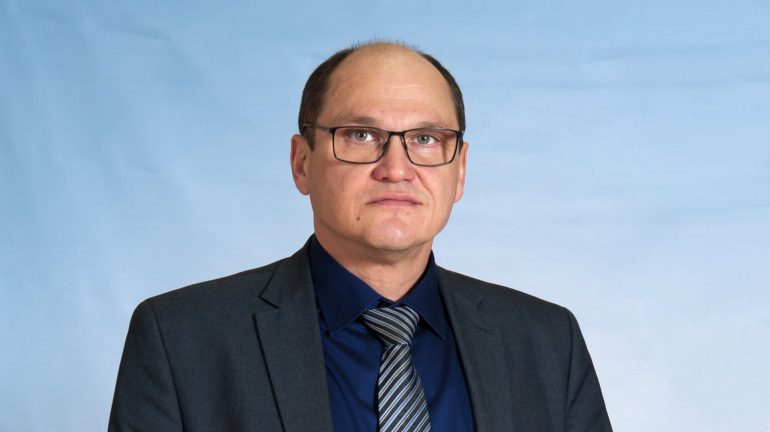
Рассказывает Ринат Асадулин
Заместитель генерального директора по производству АО «ПО «Электрохимический завод»
Для мирного урана
Не секрет, что получение высокообогащенного урана (по изотопу 235) в 50-е годы ХХ века в первую очередь было необходимо для создания ядерного оружия: в это время ковался ядерный щит страны. Этим занимался не только СССР, но и другие государства. Но тогда же, в 1954 году, была запущена в эксплуатацию первая в мире АЭС — Обнинская, и стало понятно, что 235U может использоваться и в мирных целях. А это уже принципиально новая задача. Атомные станции должны были стать источником стабильной и при этом дешевой электрической энергии, то есть быть экономически эффективными. Соответственно, появилась задача снизить затраты на каждом этапе ядерного топливного цикла с конечной целью всех этих усилий — снизить цену кВт·ч.
На момент пуска Обнинской АЭС были известны несколько методов разделения изотопов, в том числе электромагнитный, термодиффузионный, газоцентрифужный, газодинамический (звуковое сопло, вихревая труба и т.п.), но первым промышленным методом разделения изотопов стал газодиффузионный. Это эффективный метод, но чрезвычайно энергозатратный. Поэтому разработка советскими учеными газоцентрифужной технологии разделения изотопов урана, причем технологии промышленной, а не экспериментальной, была настоящим прорывом. По сравнению с газодиффузионным методом затраты на одну единицу работы разделения (или, говоря по-другому, энергозатраты на производство) сократились более чем в 20 раз! Это главное конкурентное преимущество газовых центрифуг.
Пуск первых газодиффузионных мощностей на Электрохимическом заводе был произведен в 1962 году. Первая промышленная очередь газовых центрифуг была запущена на заводе уже в 1964 году. ЭХЗ в то время был самым молодым предприятием разделительного производства в СССР. При этом и от газодиффузионного метода разделения изотопов на заводе не отказались. Обе технологии разделения существовали совместно вплоть до 1990 года, то есть на ЭХЗ одновременно эксплуатировались газодиффузионные корпуса и параллельно запускались очереди газовых центрифуг. В итоге завод совместно решал конструкторские, технологические и научные задачи — как наиболее эффективно состыковать эти технологии.
Содружество разделителей
Газовая диффузия — это технологический процесс, основанный на различной скорости проникновения молекул газа с разной молекулярной массой через микропористую структуру, изготовленную из спеченного металлического порошка, при котором необходимо прокачивать значительное количество гексафторида урана с использованием компрессорного оборудования. При этом эффект разделения на одной ступени очень низкий, значит, этот очень энергозатратный процесс нужно повторить множество раз. Ротор центрифуги вращается в вакууме на магнитном подвесе с опорой на тонкую иглу. Центробежная сила действует на молекулы гексафторида урана, и в соответствии с разницей молекулярных масс происходит разделение. В пристеночном слое оказываются более тяжелые молекулы, содержащие изотоп 238U, к центру ротора концентрируются более легкие молекулы, содержащие изотоп 235U. Дополнительный эффект разделения в центрифуге возникает за счет осевой циркуляции рабочего газа в пристеночном слое. Раскрутить ротор в вакууме существенно проще, чем продавить гексафторид урана сквозь мелкоячеистую мембрану (для этого нужно создать очень высокое рабочее давление). А с газовыми центрифугами избыточное давление создавать не нужно, соответственно, энергозатраты на разделение в разы ниже.
Новая страница
Как только был создан каскад газовых центрифуг для разделения изотопов урана, ученые задались вопросом, можно ли с помощью центрифуг разделять изотопы других элементов. Прежде всего речь шла о стабильных изотопах — изотопные таблицы уже были известны. На базе Института атомной энергии в Москве (впоследствии — Курчатовский институт) еще в конце 1950-х начали проводиться экспериментальные работы. Базовой площадкой по созданию промышленных методов разделения был УЭХК. Академик Исаак Константинович Кикоин в 1970-е годы предложил создать опытно-промышленное производство стабильных изотопов. И первой промышленной площадкой не только в Советском Союзе, но и во всем мире стал ЭХЗ. Эту инициативу тогда поддержали технические руководители — Валентин Григорьевич Шаповалов, Анатолий Николаевич Шубин, которые стояли непосредственно у истоков разделения изотопов неурановых элементов. Можно сказать, что тогда была открыта новая страница в истории атомной отрасли.
Довольно серьезную роль в деле развития производства изотопов сыграло участие ЭХЗ в проектах «Килограмм-2» и «Килограмм-3». Эти проекты решали сразу две фундаментальные задачи — создание образца эталона массы и уточнение числа Авогадро. В процессе работы по созданию альтернативы эталона массы специалисты ЭХЗ смогли достичь степени обогащения 28Si до 99.999%. Это высочайшая степень обогащения. Теперь мы знаем, что можем добиваться такой степени для самых разных элементов. Благодаря этому, мы участвуем во всех значимых проектах по поиску безнейтринного двойного бета-распада, которые ведутся в мире. Так, изотопы 72Ge и 100Mo, которые нарабатываются для международных научных коллабораций в рамках проектов GERDA и AMoRE по поиску безнейтринного двойного бета-распада, существенно продвигают фундаментальную науку в области понимания процесса развития Вселенной после Большого взрыва.
Эталонная работа
И уже в 1971 году была наработана первая партия 57Fe, обогащенного до 80%. Естественно, все разработки были строго засекречены. Область применения 57Fe — от дефектоскопии и метрологии до космических технологий. Не надо забывать, что 1960–1970-е годы — это начало космической эпохи в СССР, в это время активно разрабатывались первые ядерные реакторы для космических аппаратов. И для этого могли быть использованы специфические свойства стабильных изотопов различных химических элементов, которые ученые тогда не могли получить в значимых количествах другими методами.
Задачи тех времен раскрывались как большая толстая книга. С получением каждого нового изотопа, отдельно обогащенного, можно было изучать его свойства, также можно было, используя уже существующие ядерные реакторы, получать радиоактивные изотопы, проводить исследования как в медицинских целях, так и для развития фундаментальной науки. Отдельное направление — изучение влияния свойств стабильных изотопов на конструкционные материалы, ведь в ядерном реакторе при высокой плотности потока нейтронов, естественно, происходит изменение свойств материалов. Вторым элементом, изотопы которого разделили на ЭХЗ, был вольфрам.
Опытно-промышленное производство стабильных изотопов на ЭХЗ начали создавать с 1971 года. Лабораторные и малые стенды были созданы на базе центральной заводской лаборатории совместно с учеными Института атомной энергии им. И. В. Курчатова.
Затем задачи применения изотопов начали расширяться, и в конце 1980-х годов было построено отдельное специализированное производство по получению радиоактивных изотопов. Помимо 55Fe, на заводе был получен 14C. Следующим шагом стало получение в промышленных масштабах 85Kr, который до сих пор востребован на рынке, в первую очередь как источник для дефектоскопии.
«Светлана» расширяет линейку
Успех работы над получением стабильных изотопов в 1970–1980-х привел к появлению так называемого проекта «Светлана» — созданию на ЭХЗ полноценного промышленного комплекса производства стабильных изотопов.
В 1990-е, когда Росатом вышел на мировой рынок, производство стабильных изотопов на ЭХЗ получило новый толчок к развитию, поскольку пошли заказы от научных организаций и коллабораций практически со всего мира.
Другое направление использования стабильных изотопов — медицина. Это в первую очередь получение изотопов молибдена, иридия, теллура и ксенона, которые в дальнейшем после облучения в ядерных реакторах и ускорителях переходят в радиоактивные изотопы, например 98Mo — в 99Tc. За последние годы на ЭХЗ линейка производства стабильных изотопов расширилась до 22 элементов таблицы Менделеева. Учитывая, что у одного элемента может быть несколько изотопов, на ЭХЗ освоена технология наработки 115 различных изотопов.
Изотопы одного и того же элемента могут использоваться в различных сферах. Например, одним из старейших у нас является производство цинка, обедненного по изотопу 64. Он широко используется на атомных станциях зарубежного дизайна для добавления в теплоноситель первого контура, мы производим его уже много лет, успешно поставляем в форме оксида цинка либо ацетата цинка на международный рынок. А в настоящий момент ученым потребовались также 66Zn и 68Zn. Это говорит о том, что наука еще изучает свойства изотопов, и какие изотопы будут востребованы в дальнейшем — это нам только предстоит узнать. Наука ведь не стоит на месте, идет вперед. И наши технологии позволяют не отставать от этого процесса.
Технологии ЭХЗ постоянно совершенствуются, и мы стремимся успевать за потребностями современных индустрий. И здесь ЭХЗ имеет возможность опираться на очень богатую базу, наработанную десятилетиями.
И сейчас, если потребуется, мы можем взять любое вещество, которое может находиться в газообразном состоянии и давление его насыщенных паров позволяет подать его в газовую центрифугу, и произвести разделение по изотопам.
Полезная радиоактивность
Кроме производства стабильных изотопов, ЭХЗ имеет возможность разделять изотопы радиоактивных элементов. Газовой центрифуге, так скажем, все равно, какой изотоп разделять — стабильный или радиоактивный (конечно, с учетом активности радиоактивного изотопа и коррозионной стойкости используемого вещества). Например, мы достигли больших успехов, впервые получив партию обогащенного 63Ni, который является источником мягкого бета-излучения и может использоваться, например, как источник электропитания с длительностью работы до нескольких десятилетий. В перспективе область применения низковольтных бетавольтаических источников питания колоссальна — начиная с медицинских электрокардиостимуляторов и заканчивая приборами в космосе, которым необходимо надежное электроснабжение на десятилетия.
Важный эпизод в истории ЭХЗ связан с реализацией большой межправительственной программы ВОУ-НОУ (высокообогащенный уран — в низкообогащенный уран), которая продолжалась больше 10 лет. Заложенный в те годы научный и технологический фундамент позволил впоследствии разработать технологии обращения с регенерированным ядерным топливом. Тогда же наши специалисты получили возможность изучить опыт американских коллег в области системы учета ядерных материалов, аналитики, контрольно-измерительных приборов, что в принципе имело положительный результат для Росатома в целом. Цена, по которой производились покупка и продажа урана, до сих пор вызывает споры, но сотрудничество физиков-ядерщиков из США и России было, безусловно, взаимовыгодным. В области мирного атома это был один из примеров того, что сотрудничество разных стран в технологии и обращении с ядерными материалами должно только развиваться. Без этого атомная энергетика многое потеряет.
Мегатонны в мегаватты
Суть технологии такова: после облучения обогащенного 62Niв ядерном реакторе получается радиоактивный 63Ni, а после синтеза рабочего вещества, которое позволяет производить разделение, нарабатывается обогащенный 63Ni. Сейчас идет работа по промышленному получению в отечественных реакторах изотопа 63Ni для последующего его обогащения. Подготовка производства для получения 63Ni практически закончена, в ближайшее время его планируется запустить.
Перелить по стандарту
В начале 1990-х с выходом на международный рынок появилась новая задача. По международным стандартам, в частности ASTM, требования к упаковке и подходы к определению качества обогащенного уранового продукта отличаются от российских. В первую очередь должна быть произведена так называемая гомогенизация гексафторида урана, которая производится в установках перелива. По сути, твердый гексафторид урана, находящийся в стальных контейнерах, должен быть подвергнут расплаву и перелит в контейнер заказчика для последующей поставки зарубежному покупателю. На ЭХЗ было решено строить собственные установки перелива. Первый поставщик обогащенного уранового сырья за рубеж — УЭХК — уже имел такие установки. Мы проанализировали опыт УЭХК, провели исследования рынка поставщиков оборудования. В итоге совместно с Четвертым главным управлением Министерства атомной промышленности и институтом ВНИПИЭТ (г. Ленинград) в качестве поставщика установок перелива была выбрана французская фирма COGEMA, имеющая богатый опыт их производства. Тогда впервые работники нашего закрытого предприятия посетили французские площадки, а представители COGEMA побывали на ЭХЗ.
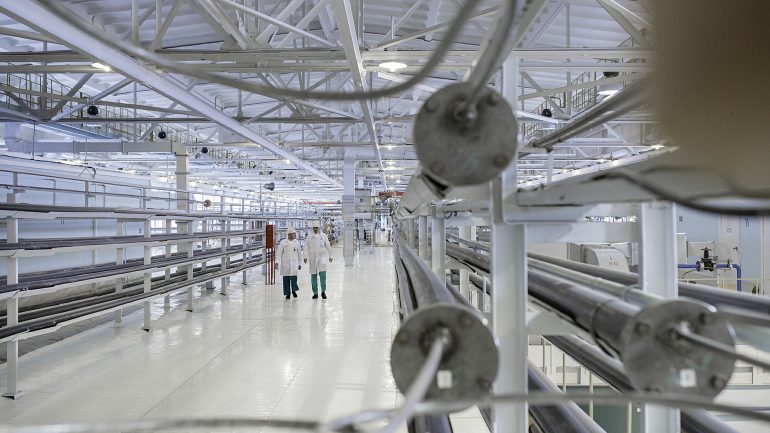
Непосредственно внедрением технологий и строительством установок перелива занимались на тот момент заместитель главного инженера по производству Станислав Михайлович Тащаев и вновь назначенный начальник участка перелива Сергей Иванович Белянцев, которых, к сожалению, сейчас с нами уже нет. В 1994 году первая установка перелива была успешно запущена. В шефмонтаже и строительстве на площадке ЭХЗ участвовали французские специалисты. Сотрудничество с фирмой COGEMA и в целом с французскими атомщиками продолжилось. Мы построили еще несколько установок. А опыт такого сотрудничества перерос в новый перспективный проект — создание установки по обесфториванию W-ЭХЗ. Хочу отметить: строительство установок перелива стало действительно значимым событием как для завода, так и для города.
Переход на мирные рельсы
Производство оружейного урана на ЭХЗ было прекращено в 1987 году. Поскольку комбинат должен был перейти на задачи обеспечения топливом АЭС, мы заранее стали готовить производство под обогащение 235U до 5%.
Предварительная подготовка велась несколько лет, и в 1987 году в химическом цехе (цех кондиционно-испарительных установок) ввели в эксплуатацию секции коллектора К-02, который и производит конденсацию урана, обогащенного до 5%. Кроме того, пришлось перестроить схему каскадов центрифуг, перестроить схему технологического контроля изотопного состава урана, оборудовать места для физического размещения масс-спектрометров и гамма-спектрометров, адаптировать существующие, разработать и аттестовать новые методики измерений для установления соответствия новой продукции требованиям технических условий, запустить и освоить новое аналитическое оборудование для измерений. С тех пор ЭХЗ успешно выполняет поставки 235U для производства топлива для АЭС.
Надо понимать, что газовые центрифуги лежат в основе технологии всех действующих разделительных заводов в мире. Но отечественная технология газоцентрифужного производства все же отличается от зарубежных аналогов. В первую очередь нашим преимуществом является гибкая система универсальных каскадов, которые без значимых переделок позволяют получать всю линейку обогащенного уранового продукта для реакторов всех типов — РБМК, ВВЭР, PWR, исследовательских реакторов и реакторов на быстрых нейтронах. Эту линейку обеспечивает целый набор отечественных ноу-хау, что позволяет нам, в том числе, успешно работать на спотовом рынке.
Исключительно чисто
Одно из ноу-хау, использующихся сейчас в производстве, — очистительные центрифуги. Чтобы синтезировать вещество (газ), которое будет направлено в газовую центрифугу, где произойдет разделение изотопов, нужно использовать различные химические соединения: фториды, метилы, этилы, бораты, карбонилы и многие другие. Химические соединения для каждого элемента специфичны по свойствам: у них разные температуры конденсации, кипения, терморазложения, разное коррозионное взаимодействие с конструкционными материалами оборудования разделительных каскадов.
Чтобы эффект разделения был максимальным, химически активное соединение, подающееся в центрифугу, необходимо очищать от примесей. Очистительная машина как раз и предусматривает очистку основного рабочего вещества от легких соединений. Также проводится и очистка товарной продукции. Без очистительных машин стабильное производство многих изотопов было бы просто невозможно.
Энергия на тысячи лет
Еще одно перспективное направление, над которым сейчас работают специалисты ЭХЗ, — работа по обесфториванию накопленных запасов гексафторида урана. В мире на сегодняшний день накоплено несколько миллионов тонн обедненного гексафторида урана. Он надежно упакован в стальные контейнеры, но надо понимать, что соединение гексафторида урана является коррозионно-активным. А значит, требующим дополнительного внимания и затрат на обеспечение безопасного хранения.
В свое время французская компания Areva разработала референтную технологию по созданию установок обесфторивания гексафторида урана. В начале 2000-х годов руководство ЭХЗ задалось целью включить предприятие в мировой цикл работ по переводу обедненного гексафторида урана в более безопасную форму хранения — в форму закиси-окиси, которая является естественным инертным веществом. В 2005 году был заключен контракт с компанией Areva. К тому моменту апробированной промышленной технологии по переводу гексафторида урана в оксидное состояние в нашей стране не существовало. Имелся большой набор различных способов и методов, но референтной технологией владели именно французы.
Благодаря тесным связям, наработанным еще во время создания установок перелива, работа пошла быстро. Обесфторивание обеспечили реакторы высокотемпературного пирогидролиза — установка W-ЭХЗ. В реактор подаются перегретый пар и водород, и в зонах реактора при температурах, достигающих 780 °C, из обедненного гексафторида урана образуется закись-окись урана. Ее остается упаковать в контейнеры и отправить на площадку для хранения. Обедненная закись-окись урана — это, безусловно, потенциальный источник топлива для следующего этапа развития атомной энергетики, в первую очередь для реакторов на быстрых нейтронах. Если оценивать сегодняшние объемы накопленного обедненного гексафторида урана, хранящегося на площадках по всему миру, это источник энергии на тысячи лет вперед. На сегодняшний день на ЭХЗ более 125 000 тонн обедненного гексафторида урана переведено в более безопасную форму хранения в виде закиси-окиси.
Помимо этого, фтор, который присутствует в гексафториде урана, тоже можно использовать. Опыт французов показал, что получаемые после обесфторивания гексафторида урана фтористоводородные продукты, прежде всего химически чистая концентрированная фтористоводородная кислота (уже не содержащая уран), являются востребованным товаром на рынке. Фтористоводородная кислота активно используется во всем мире при производстве фторопластов, электролитов, в металлургической промышленности. Разумеется, мы на ЭХЗ ведем непрерывный контроль как безопасности самого процесса, так и качества фтористоводородной кислоты. Сейчас мы начинаем второй проект по обесфториванию гексафторида урана, на сей раз с фирмой Orano. Проект находится в стадии реализации, и в ближайшие год-полтора мы эти установки запустим.
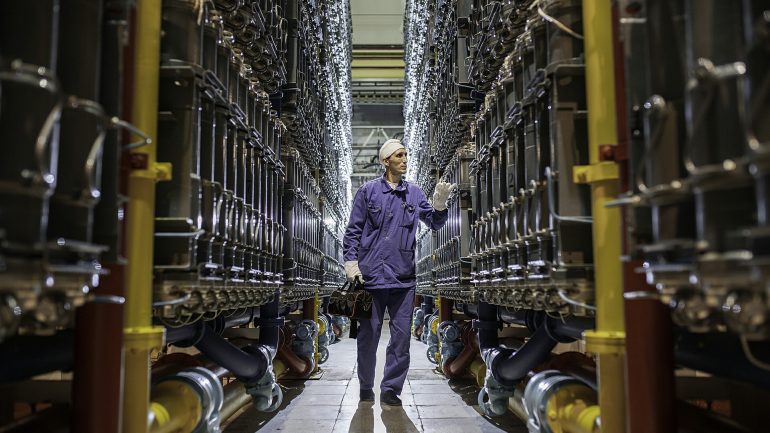
Центрифуги нового века
Нашим постоянным партнером в деле совершенствования технологий, в частности технологий ГЦ, является «Центротех-Инжиниринг» в г. Санкт-Петербурге. В 1990-е это было КБ, которое входило в состав ЭХЗ, что в то время было неплохим решением для финансирования и развития КБ, конкретизации заказов. Сейчас мы продолжаем тесное сотрудничество уже в рамках топливного дивизиона Росатома. Прежде всего, речь идет о разработке новых центрифуг для производства стабильных изотопов на базе современных урановых ГЦ поколения 9+. Второе направление сотрудничества — цифровой инжиниринг, работа в области создания цифровых двойников перспективного оборудования.
В наши дни развитие газоцентрифужной технологии в первую очередь связано с созданием поколений новых машин, более эффективных, менее энергоемких, более надежных. В настоящий момент на ЭХЗ идет очередная модернизации с заменой газовых центрифуг поколения 5 на поколение 9+, сегодня производятся предпусковые работы, в 2022 году будет запущено пять очередей ГЦ 9+. Вместе с заменой газовых центрифуг проводится замена устаревшего вспомогательного оборудования: меняются схемы и оборудование электроснабжения, контроля автоматики и управления.
Наши газовые центрифуги работают десятки лет практически без остановки. Технологии работы вспомогательного оборудования за эти годы уходят далеко вперед. Сейчас разделительное производство не только в России, но и во всем мире относится к числу наиболее автоматизированных. Участие человека в процессе сведено к минимуму — обслуживание, поддержание рабочего состояния и, естественно, проведение технологических переключений при переходе на различные номиналы обогащения. Поколение ГЦ 9+ уже на этапе внедрения позволяет изменить систему управления разделительными каскадами. Можно сказать, что это шаг в сторону полной цифровизации производства обогащенного уранового продукта.
Дальше — «цифра»
Системы управления каскадами и вспомогательным оборудованием постоянно совершенствуются. При таком уровне автоматизации возможности для оптимизации как технологий, так и бизнес-процессов практически уже исчерпаны. Сейчас мы стоим на пороге перехода от автоматизированной к цифровой системе управления. Цифровая система подразумевает разработку алгоритмов управления производством, что открывает принципиально новые возможности. Современное производство, в том числе разделительное, — это работа с большими данными. Использование MES-систем управления производством и внедрение верхнего уровня ERP-систем позволяют найти те узкие места, которые человек, даже погруженный в производство на протяжении 50–60 лет, просто не видит. «Цифра» способна охватить все производство, до самого мелкого болта или гайки. ЭХЗ и сегодня работает с наилучшими показателями коэффициента использования установленной мощности в отрасли — 97%. Чтобы сделать следующий шаг, необходимо внедрять цифровые системы, полностью отказываться от бумажных отчетов, сокращать время протекания процессов. Пришло время научиться использовать методы предиктивного анализа, оптимизировать работу вспомогательного оборудования.
В настоящее время вместе с АО «ТВЭЛ» и АО «Гринатом» мы ведем активную работу по созданию унифицированной цифровой платформы по управлению производством. Одна из задач этой системы, когда она заработает на всех предприятиях «ТВЭЛ», — показать, сколько стоит каждый передел в каждый отдельный промежуток времени. На более высоком уровне внедрения платформа позволит равномерно загрузить заказами предприятия топливного дивизиона, исходя из имеющихся мощностей и эффективности их работы.