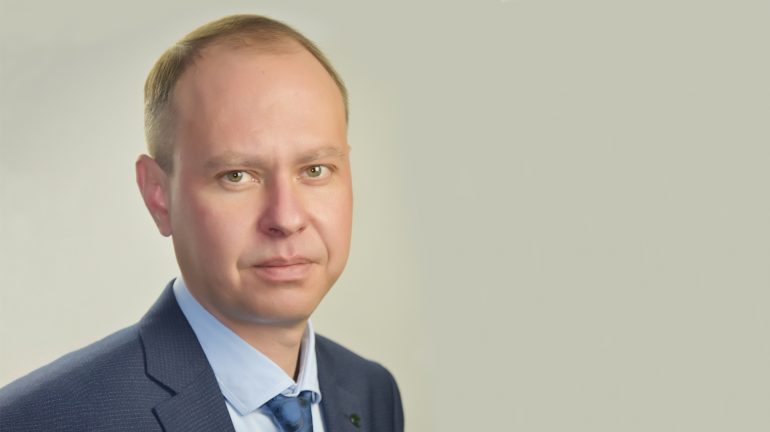
Рассказывает Виктор Минько
Заместитель генерального директора АЭХК по операционной деятельности — директор уранового производства
Неразрывная связь
Я родился в городе Навои, республика Узбекистан. В 2001 году окончил Томский политехнический университет по специальности «физик». Во время учебы проходил практику на АЭХК в качестве аппаратчика, а в апреле 2001 года был принят на комбинат технологом-стажером. Прошел трудовой путь от технолога, заместителя начальника смены до начальника цеха разделения изотопов урана, в 2020 году назначен на должность заместителя генерального директора по операционной деятельности — директора уранового производства. Так что вся моя трудовая жизнь неразрывно связана с этим предприятием. Расскажу о его богатой и яркой истории.
От рекорда к рекорду
В 1954 году было принято решение Совмина СССР о строительстве в Ангарске Иркутской области комбината атомной промышленности, и уже 21 октября 1957 года был произведен исторический пуск первой очереди корпуса № 1 диффузионного завода АЭХК: в работу были включены 308 диффузионных машин и начат отбор товарной продукции — обогащенного урана. Возведение в глухой сибирской тайге столь мощного и энергоемкого предприятия было продиктовано необходимостью сохранения ядерного паритета в условиях холодной войны. В то время кроме СССР подобные производства освоили только США.
Комбинат рос и развивался ударными темпами. На момент пуска на предприятии работали 1700 человек, каждый месяц к ним прибавлялись еще 130–140. В рекордные сроки — в течение 1957–1963 годов — были построены и сданы в эксплуатацию практически все основные промышленные объекты АЭХК.
В 1962 году был выведен на проектную мощность химический завод (сублиматное производство), который должен был обеспечить сырьем — гексафторидом урана — разделительное производство. Так комбинат обрел стабильность и независимость от поставщиков. Масштабы производства признаны рекордными: производительность фтораторов составляла до 100 тонн гексафторида урана в сутки. Это были мощнейшие установки в мире, напрямую фторирующие любое урансодержащее сырье и использующие для охлаждения воду.
Завод по обогащению урана был введен в эксплуатацию в проектном объеме (четыре корпуса) в 1963 году. 7000 газодиффузионных машин, в состав которых входили 14 000 мощных компрессоров, располагались в четырех километровых корпусах. АЭХК в те годы был самым мощным газодиффузионным производством в мире!
Комбинат был одним из самых энергоемких предприятий Советского Союза — электролизный завод АЭХК уже в 1962 году потреблял 14 млрд кВт·ч, что составляло 4% всей электроэнергии, вырабатываемой в СССР. Кроме энергетической базы производства — ТЭЦ-10, тогда одной из мощнейших в стране — энергию гиганту поставляли Иркутская и Братская ГЭС.
Запуск предприятия способствовал снятию международной напряженности и сохранению стабильности в мире. Когда пришло время, комбинат полностью перешел на производство мирного урана и ныне способствует решению важных задач научного и прикладного характера.
Новая эпоха
Диффузионный завод выпускал низкообогащенный уран (до 6,5%) для нужд ядерной промышленности и проработал на полную мощность в течение 30 лет. В 1990 году на АЭХК состоялся пуск первых блоков газовых центрифуг по разделению изотопов урана. Ранее внедрение принципиально нового центробежного производства на комбинате сдерживалось расположением Ангарска в зоне повышенной сейсмичности. Создание газовых центрифуг с высокой сейсмической устойчивостью, а также большой комплекс исследовательских работ по обоснованию возможности применения этих центрифуг в условиях сейсмичности района позволили в начале 1980-х годов принять решение о поэтапной реконструкции диффузионного завода.
В результате замены на АЭХК газодиффузионной технологии разделения изотопов на центрифужную, помимо повышения производительности, существенно изменилась экологическая обстановка в регионе. Водопотребление комбината сократилось в десятки раз, а потребление электроэнергии упало на порядок — появилась возможность значительно снизить нагрузку ТЭЦ-10, уменьшить выбросы в окружающую среду. АЭХК сегодня является одним из самых экологически чистых предприятий Иркутской области.
Экологично
Переход АЭХК на газоцентрифужную технологию обогащения урана стал мощным и своевременным технологическим прорывом. В этом огромная заслуга Виктора Федоровича Новокшенова — первого директора предприятия с момента его основания. Виктор Федорович понимал со всей прозорливостью, что новый метод эффективен, экономичен и перспективен не только для экономики страны и региона, но и для будущего родного комбината. Тотальная модернизация промышленного гиганта стала дерзким вызовом не только для работников АЭХК, но и для всего научного, проектного и производственного комплекса Минсредмаша СССР. Многие технологические задачи пришлось решать впервые в отрасли, но несмотря на все сложности и проблемы, уникальная производственная задача была реализована в сжатые сроки и с превосходным результатом.
Этапы большого пути
В 1982 году Ефим Павлович Славский, министр среднего машиностроения СССР, утвердил задание на проектирование реконструкции газодиффузионного завода и перевода АЭХК на газоцентрифужный метод обогащения урана. Реализация проекта реконструкции началась в следующем году с остановки и демонтажа части диффузионного оборудования корпуса № 1 (последние блоки были остановлены в 1987 году, год спустя оборудование в первом корпусе было демонтировано, полностью диффузионное оборудование в трех других корпусах было остановлено в 1992 году).
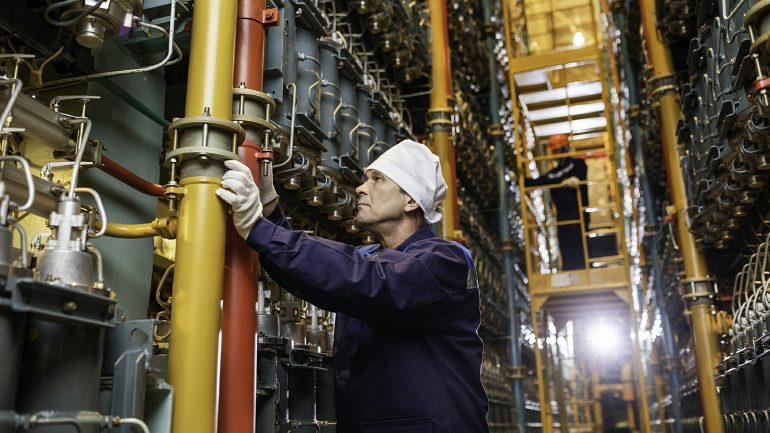
Для подготовки и обучения персонала эксплуатации центрифуг в 1983 году был построен и включен в эксплуатацию опытный стенд С-400, а также инженерно-сейсмометрическая станция.
В 1984 году в корпусе № 801 начались строительные работы по сооружению центрифужного каскада. В соответствии с проектом было построено здание ЦДП, холодильная станция с инженерными коммуникациями, рассчитанными на эксплуатацию каскада газовых центрифуг в объеме 54 блоков.
10 декабря 1990 года было подано напряжение на технологическую секцию № 25, начался разгон газовых центрифуг блоков № 24 и 25. После проведения комплекса регламентных работ блоки № 24 и 25 были выведены на номинальный технологический режим и включены в общую технологическую схему завода совместно с диффузионным оборудованием. На АЭХК наступила эпоха центрифужной технологии.
В результате смены технологии существенно повысилась производительность предприятия, при этом центрифужный метод обогащения сделал конечную продукцию предприятия дешевле. Конечно, в 1990 году, при все еще плановом хозяйстве, это не было определяющим параметром. Но в период смены экономического строя именно центрифужная технология смогла помочь АЭХК сделать свою продукцию конкурентоспособной по цене и выйти на мировые рынки.
Триллионы безотказных оборотов
Официальный ресурс российских ГЦ шестого поколения — 30 лет без останова и ремонтов при числе возможных отказов менее 0,1% в год. Это ресурс машины, ротор которой вращается со скоростью более 1500 оборотов в секунду! За ресурсное время ротор каждой центрифуги успевает совершить около двух триллионов оборотов под нагрузкой.
До 1995 года были введены в эксплуатацию еще 10 блоков, затем в 2000–2001 годах — ввели три блока газовых центрифуг шестого поколения. Далее наращивание разделительных мощностей было реализовано через строительство неперестраиваемых каскадных установок. («Традиционный» разделительный каскад состоит из технологических блоков, из которых формируются разделительные ступени. Количество ступеней в каскаде может меняться в зависимости от режима работы. Неперестраиваемый каскад состоит из последовательно соединенных технологических ступеней, число которых постоянно). В 2004–2005 годах на АЭХК был введен в эксплуатацию неперестраиваемый каскад № 1 с ГЦ шестого поколения. В 2009–2011 годах — неперестраиваемый каскад № 2, он укомплектован ГЦ восьмого поколения без оптимизации площадей предприятия.

Комплекс оборудования разделительного производства состоял из разделительного каскада, конденсационно-испарительной установки, станции производства жидкого азота, компрессорной станции, системы промышленного водоснабжения. Разделительный каскад размещался в четырех производственных корпусах.
На новые рынки
1990-е годы для комбината, как и для многих предприятий страны, были не самым лучшим временем. Снижение потребности в сырьевом гексафториде урана на внутреннем рынке, выведение из эксплуатации газодиффузионного оборудования и, как следствие, резкое сокращение разделительных мощностей способствовали замедлению темпов модернизации уранового производства. В этот нелегкий для АЭХК период его руководство определило одним из стратегических направлений дальнейшего развития предприятия строительство участка по переливу жидкого гексафторида урана. Наличие такого участка обеспечило бы комбинату возможность выхода не только на внутренний, но и на международный рынок поставок и услуг по обогащению урановой продукции. Участок решено было назвать «Челнок».
В процессе создания участка «Челнок» были впервые применены многие принципиально новые для отрасли и комбината решения: компоновка оборудования с многоступенчатой схемой защиты персонала и окружающей среды, новая схема очистки вентиляционных газов, улучшенная система охлаждения и уплотнения автоклавов. Всего с 1991 по 1997 год на участке было реализовано 290 уникальных технических решений.
Уникальный «Челнок»
В сентябре 1992 года руководством предприятия было утверждено решение о создании на АЭХК участка по переливу жидкого гексафторида урана (ГФУ), а уже в 1993 году был заключен контракт на изготовление и поставку оборудования для участка «Челнок-А» с предприятием из Финляндии. «Челнок» был задуман самостоятельным производственным подразделением, легко вписывающимся в любой цех или трансформирующимся в отдельную структурную единицу комбината. Закладывалась высокая степень автономии участка, что позволяло оперативно решать производственные проблемы.
1 февраля 1995 года был выполнен первый перелив ГФУ, с 24 апреля 1995 года участок приступил к выпуску продукции по утвержденному графику. В мае 1997 года на участке были введены еще две установки по переливу жидкого ГФУ. Они обеспечили возможность перетаривания продукции в контейнеры международного образца и осуществление пробоотбора в соответствии с требованиями международных стандартов.
С целью оптимизации производственной деятельности в 2010 году было произведено объединение структур технологического участка конденсационно-испарительных установок (КИУ) и участка по переливу жидкого ГФУ. В 2011 году руководством Топливной компании «ТВЭЛ» было принято решение о переориентации АО «АЭХК» для поставок ГФУ на внутренний рынок, и с 2011 года оборудование установок по переливу ГФУ законсервировано.
Под контролем МАГАТЭ
В наше время важность инициатив, связанных с гарантированными и недискриминационными поставками ядерного топлива, нераспространением ядерного оружия и технологий двойного назначения, существенно возрастает во всем мире. Россия стала первой страной, которая воплотила в жизнь свое предложение о создании сети международных центров по предоставлению услуг ядерного топливного цикла, включая обогащение, под контролем МАГАТЭ. Первым таким центром стал Международный центр по обогащению урана (МЦОУ) в Ангарске, созданный во исполнение Соглашения между правительством Российской Федерации и правительством Республики Казахстан от 10 мая 2007 года. Центр открыт для участия других государств, которые выполняют обязательства в рамках Договора о нераспространении ядерного оружия и разделяют цели и задачи МЦОУ.
Основной задачей центра является обеспечение гарантированных поставок услуг по обогащению урана своим акционерам за счет гарантированного доступа к разделительным и сублиматным мощностям всех российских предприятий. Кроме того, развитие инициативы нашло свое отражение в создании при МЦОУ банка топлива — запаса низкообогащенного урана для гарантированного обеспечения поставок в другие страны по запросу МАГАТЭ.
Регулировать с умом
Специалистами предприятия велась и ведется большая работа по совершенствованию производства. Расскажу об этом на одном примере. Для поддержания необходимых значений технологических параметров в схемах разделительных производств используются пневматические регуляторы, им требуются существенные объемы сжатого воздуха, которые обеспечиваются работой компрессорной станции, состоящей из трех компрессоров, каждый номинальной мощностью 75 кВт. Надо отметить, что работа компрессоров сжатого воздуха связана с высокими затратами как на энергоресурсы, так и на эксплуатацию здания и обслуживающий персонал.
Силами экспериментальной лаборатории отдела главного прибориста АЭХК в 2007 году был разработан полный комплект конструкторской документации на микропроцессорный регулятор для разделительного производства РМ ЭЛ.2.084. Далее была изготовлена партия опытных образцов, проведен комплекс всесторонних испытаний, в том числе стендовых — в лабораторных условиях и на газовом стенде СИГ в различных режимах расхода и давления ГФУ.
Первый регулятор РМ был установлен на расходомерный узел резервной линии потока № 6 межкаскадных коммуникаций в 2009 году. Существенные преимущества нового регулятора по сравнению с пневматическими (отсутствие необходимости в подаче сжатого воздуха, более устойчивое поддержание заданного давления и т.д.) были видны сразу. В ноябре 2011 года ведомственная комиссия провела приемочные испытания, по положительным результатам которых были приняты решения рекомендовать регулятор давления РМ к серийному выпуску и к применению на разделительных производствах предприятий Топливной компании.
С этого времени и до 2017 года на АЭХК регуляторы РМ внедрялись точечно, сначала на потоке № 5 МКК, затем на ступенях 1, 2, 3 неперестраиваемого каскада № 1, на блоке № 12 основного каскада. По результатам опытной, а затем и промышленной эксплуатации установленных РМ было принято решение о постепенном отказе от использования пневматических регуляторов, а затем (в июле 2019-го) — решение о вводе в эксплуатацию РМ, смонтированных на технологических коммуникациях разделительного производства. Экономический эффект от выключения из работы компрессорной станции разделительного производства в 2020 году только от экономии электроэнергии составил более 30 млн руб.
В особом режиме
В чем заключается технология обогащения газоцентрифужным методом? Гексафторид урана в газообразной форме подается внутрь вращающегося ротора центрифуги. При огромной скорости вращения ротора, достигающей нескольких десятков тысяч оборотов в минуту, внутри вращающегося ротора устанавливается определенное распределение газа по массе. Кроме того, внутри ротора имеет место циркуляция газа, дополнительно способствующая разделению газа на легкую и тяжелую фракции, которые и отводятся из центрифуги по отдельным трубкам. Легкая фракция, по сравнению с исходным сырьем, содержит больше легкого изотопа 235U и меньше тяжелого изотопа 238U, а тяжелая фракция — наоборот. Эффект разделения на одной центрифуге не слишком высок, поэтому центрифуги объединяются в многоступенчатые каскады для достижения необходимого уровня обогащения.
Итогом работы разделительного каскада, в который подается сырье — гексафторид урана природного изотопного состава, — является обогащенный гексафторид урана (UF6), в котором содержание 235U больше, чем в природном уране, и обедненный UF6, в котором 235-го изотопа меньше, чем в природном уране. Важно понимать, что газоцентрифужная технология позволяет эффективно использовать в качестве сырья не только UF6 природного изотопного состава, но и материал с меньшим содержанием 235U, например обедненный UF6, оставшийся с прошлых лет.
С 1 декабря 2014 года разделительное производство АЭХК перешло на работу в режиме «шахты»: продукция вырабатывается из старых «богатых» отвалов, которые являются ценным стратегическим сырьем. Уровень развития современных технологий обогащения урана в России позволяет дополнительно извлекать из обедненного гексафторида урана (ОГФУ) такое количество 235U, которое делает экономически оправданным повторное использование ОГФУ, оставшегося с прошлых лет наработки обогащенного урана. ОГФУ — это сырье, которое позволяет существенно экономить природную базу урана. Готовую продукцию АЭХК отправляет на родственные предприятия для дальнейшего дообогащения. Благодаря работе в таком режиме себестоимость единицы разделения на АЭХК одна из самых низких в отрасли.
Так называемые конечные отвалы в полном объеме направляются в АО «ПО «ЭХЗ», где работает установка W-ЭХЗ по реконверсии (обесфториванию) ОГФУ. «Вторичный» (дважды обедненный) ОГФУ, уже не пригодный для дальнейшего обогащения, также является ценным сырьем. Ключ к его дальнейшему использованию — технологии обесфторивания. Фторсодержащие продукты, получаемые в результате обесфторивания ОГФУ, — плавиковая (фтористоводородная) кислота и безводный фтористый водород — реализуются на рынке как отдельная сертифицированная продукция химического производства, а также повторно вовлекаются в ядерный топливный цикл на стадии конверсии урана.
Также на разделительных каскадах АЭХК сохраняется возможность выработки ГФУ с обогащением менее 5% для нужд российской атомной энергетики.