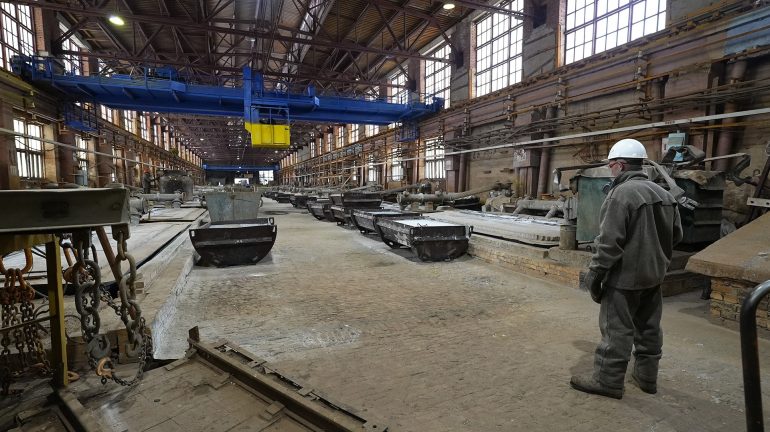
Редкоземельная химия
Знакомство с работой Соликамского магниевого завода
В соответствии с указом президента РФ, Соликамский магниевый завод (СМЗ) будет передан Росатому. Недавно корреспондент «Вестника атомпрома» побывала на предприятии. Рассказываем, как работает единственный в России производитель редкоземельных металлов.
Указ, в соответствии с которым акции СМЗ будут переданы Росатому, вышел в конце января 2023 года. В настоящее время 89,455% акций владеет Росимущество. Директор по развитию бизнеса «Атомредметзолота» Руслан Димухамедов стал гендиректором завода.
Выбор Росатома в качестве будущего мажоритарного акционера завода не случаен. Госкорпорация с 2019 года отвечает за реализацию направления «Редкие и редкоземельные металлы» в рамках дорожной карты «Технологии новых материалов и веществ». А СМЗ — единственный крупный действующий производитель редкоземельных металлов в России.
Соликамский магниевый завод заработал в 1936 году. Основным его продуктом, как следует из названия, был магний. В 1971 году в технологическую цепочку было добавлено производство редкоземельных металлов. В 2009 году завод начал выпускать титановую губку. Технологическая схема всего комплекса СМЗ выстроена таким образом, что отходы одного этапа переработки становятся сырьем для других.
СМЗ перерабатывает два типа рудного сырья — карналлитовый и лопаритовый концентраты. Карналлитовый поставляет «Уралкалий» — в буквальном смысле сосед СМЗ, его шахты по добыче калийных солей расположены вокруг Соликамска. Особенность карналлита в том, что он содержит не только калий, но и магний, все они, что важно, в форме хлоридов. Запасов карналлита хватит на сотни лет при условии поддержания добычи на шахтах. В настоящее время СМЗ перерабатывает порядка 250 тыс. тонн карналлитового концентрата в год.
Лопаритовый концентрат приходит на СМЗ с Ловозерского ГОКа, расположенного в Мурманской области. У рудников красивые местные названия – Кедыквырпахк и Карнасурт. В лопаритовом концентрате содержатся редкоземельные металлы, ниобий, тантал и титан. СМЗ перерабатывает 8 тыс. тонн концентрата в год, при этом мощности предприятия позволяют перерабатывать до 12 тыс. тонн в год.
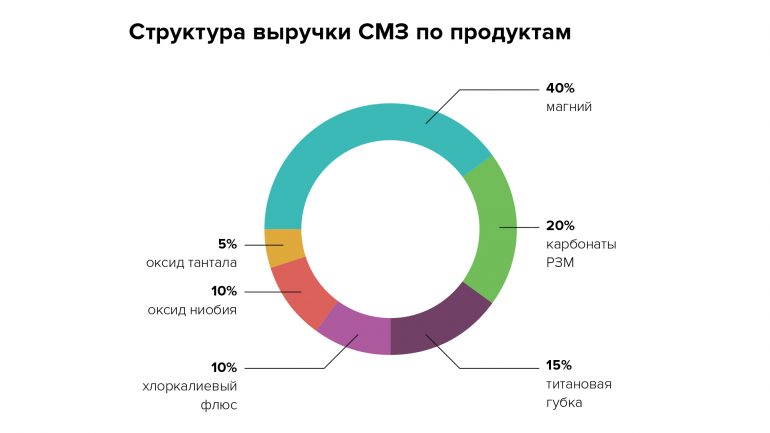
Карналлитовая технологическая цепочка
Карналлитовый концентрат по системе транспортерных лент подается в цех № 1. Здесь его обезвоживают — загружают во вращающиеся печи, где навстречу карналлиту идут топочные газы. После обезвоживания карналлит подается в печь-хлоратор, где концентрат расплавляется. Расплав наливают в ковши и подают в следующее, электролизное отделение. Поскольку ковши футерованные и хорошо хранят тепло, а плечо передачи всего несколько метров, расплав застыть не успевает.
В электролизном отделении расплавленный карналлит заливается в электролизер. Под действием электрического тока карналлит разлагается на хлор, магний и отработанный электролит, состоящий преимущественно из калия. Газообразный хлор по системе сборного коллектора отводится на компрессорную станцию, а затем — на станцию сжижения. Основной объем хлора поступает на переработку лопаритового концентрата, остаток продается в виде товарного жидкого хлора. Он нужен, например, водоканалам для обеззараживания воды. Кроме того, из хлора производят хлористый кальций — его используют для осушения, в медицине и пищевой промышленности и проч. Объем производства хлористого кальция и продуктов из хлора — порядка 40 тыс. тонн в год.
Магний при электролизе всплывает на поверхность расплавленного электролита в виде серебристых бляшек. Их собирают с поверхности вакуумным ковшом и отправляют в литейное отделение. В печи непрерывного рафинирования магний очищается от остатков примесей. Затем ковш с расплавленным магнием перемещают на литейный конвейер и аккуратно, струйкой, наливают магний в изложницы — специальные формы. Меньшую часть направляют на получение титановой губки. Остывшие слитки магния складывают в штабеля, упаковывают и отправляют клиентам. СМЗ на текущий момент выпускает 15 тыс. тонн магния в год. Потребители — российские предприятия.
Отработавший электролит не пропадает: его либо охлаждают и дробят, либо из жидкого расплава формируют гранулы — получается дробленый или гранулированный хлоркалиевый флюс (порядка 70 тыс. тонн в год). Из него делают удобрения, а также используют в металлургической промышленности.
Лопаритовая технологическая цепочка
Вторая часть производства — переработка лопаритового концентрата. Для вскрытия лопарита используют хлор, полученный на магниевом производстве. В результате образуются хлориды титана, тантала, ниобия и редкоземельных металлов (РЗМ). Поскольку у них разные температуры кипения (а, следовательно, и конденсации), то хлориды последовательно разделяют. Сначала отделяют тетрахлорид титана, затем пентахлориды тантала и ниобия (на этом этапе они отводятся вместе), после чего выделяют хлориды РЗМ.
Чтобы удалить из хлоридного концентрата РЗМ примеси, плав хлоридов смешивают с водой, добавляют реагенты, и примеси выпадают в осадок, который отделяют от раствора. Чтобы получить товарный продукт — карбонаты, в раствор добавляют соду. Карбонаты РЗМ выпадают в осадок, его фильтруют, сушат, упаковывают и отправляют клиентам. Из 8 тыс. тонн лопаритового концентрата производится чуть более 2 тыс. тонн карбонатов РЗМ.
Чтобы получить титановую губку, в специальную реторту заливают расплавленный магний (1,3–1,5 частей) и тетрахлорид титана (1 часть). Затем собирают аппарат сепарации из двух реторт, поставленных одна на другую и совмещенных устьями. Аппарат сепарации со смесью опускают в печь. Под нагревом магний восстанавливает титан, в реторте образуются металлический титан в виде губки и хлорид магния, который сливают и отправляют обратно в цех № 1 на электролиз. А блок титановой губки выбивают из реторты и перемещают на пресс послойной резки. Здесь блок режут, как колбасу, на ломти. Затем они измельчаются и подаются на барабанный грохот, где куски титана сортируются по фракциям в соответствии с ГОСТами. Следующий этап — проверка и отбраковка некондиционных фрагментов и, наконец, упаковка и отправка потребителю. Продают губку Чепецкому механическому заводу — для производства титанового проката. СМЗ производит порядка 2,5 тыс. тонн губки в год.
Ниобий и тантал до недавнего времени разделяли в ректификационных колоннах. Принцип разделения так же, как в основном техпроцессе, основан на разных температурах конденсации хлоридов ниобия и тантала, на этом этапе температуру выдерживают более точно. При необходимости тетрахлорид тантала дополнительно очищают в ректификационной колонне. В апреле 2023 года внедрена новая — экстракционная — технология разделения тантала и ниобия. «Технология себя оправдала, удалось добиться как повышения извлечения, так и существенной экономии. Уже выпущены первые партии продуктов», — сообщает Руслан Димухамедов.
Из пентахлоридов ниобия и тантала производят их оксиды. Оксид ниобия получают с помощью парового гидролиза, а оксид тантала — аммиачного. Полученные продукты сушат или прокаливают и отправляют клиентам.
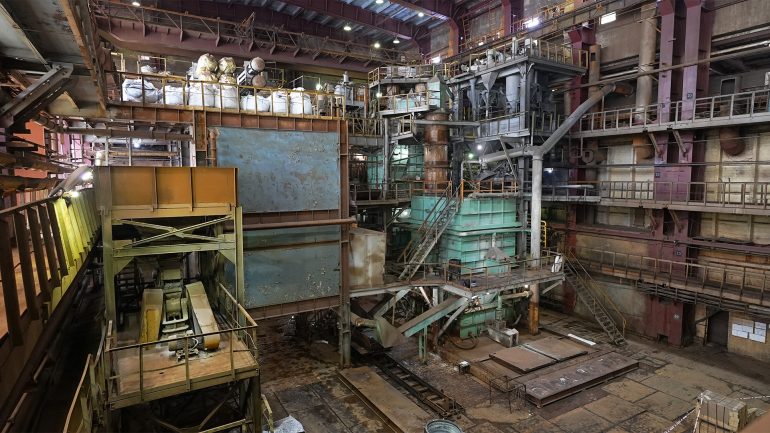
Обновления обязательны
Предприятие работает в обычном для России режиме — преодолевает санкционные ограничения, поддерживает и совершенствует существующее производство, ищет кадры и планирует развитие. Для СМЗ это создание производства по разделению коллективных концентратов РЗМ на индивидуальные металлы.
Санкции сказались разве что на поставке электродов, которые надо менять, потому что со временем они изнашиваются. Раньше их покупали в Европе. Когда поставки прекратились, срочно нашли аналоги в Челябинске, Новосибирске и Китае. «Техпроцесс сформирован таким образом, что он не требует каких-то эксклюзивных материалов и реагентов. Электроды — это самая заметная позиция в импорте, проблему мы уже решили», — комментирует Руслан Димухамедов.
Меняют не только электроды. Примерно раз в три года каждую электролизную ванну разбирают, делают новую кирпичную футеровку и вставляют новые электроды. После двух лет службы меняют реторты для получения титановой губки. Срок службы хлораторов на магниевом производстве — три года, на редкометалльном — 11 месяцев. «У нас идет постоянный процесс поддержания производственных фондов, который нельзя отменить. На предприятии строго за этим следят, предусмотрен неснижаемый объем поддерживающих инвестиций. Да, завод не выглядит как с иголочки, но мы же не двигатели собираем», — отмечает гендиректор СМЗ.
Производство постепенно модернизируется. На предприятии начали использовать новую систему сжижения хлора. Куплен новый листогиб для ремонтно-механического цеха. На нем рабочие изготавливают конусы, тигли и трубы для откачки магния и систем газоочистки. Началось строительство участка плава низших хлоридов титана — двух печей с коммуникациями. Здесь будут проводить дополнительную очистку магния, чтобы нарастить выпуск наиболее востребованной покупателями марки Мг95.
Кроме того, по запросу клиентов СМЗ выпускает партии редкометалльных соединений. Так, по заказу российского производителя микроэлектроники СМЗ произвел таблетки закаленного метаниобата лития. Его используют как основу для выращивания монокристаллов.
Развитие редкоземельной отрасли в России
Одна из ключевых задач, которая стоит перед предприятием, — создать на СМЗ разделительное производство РЗМ. Благодаря ему в России появится недостающее звено, выпавшее из-за распада Советского Союза, — индивидуальные соединения РЗМ. Это тот продукт, который уже можно использовать в качестве сырья в других отраслях.
«У нас есть четыре главных металла — лантан, церий, неодим и празеодим. Они самые востребованные, обеспечивают 98% выручки, их и будем выделять. Затем будем смотреть, как организовать выделение оставшихся элементов, относящихся к группе тяжелых РЗМ», — комментирует Руслан Димухамедов.
В 2023 году входящая в АРМЗ компания «Объединенные урановые предприятия» должна разработать технологию разделения РЗМ. В этом же году будет разрабатываться инвестиционный проект и приниматься решение о строительстве разделительного производства. На СМЗ уже подыскивают новому переделу место. На 2024 год запланировано проектирование. Для повышения экономических показателей разделительного производства необходимо увеличить поставки с Ловозерского ГОКа до 10–12 тыс. тонн лопаритового концентрата в год. Примерный объем разделенных РЗМ — 3 тыс. тонн в год.
Реалии 2022–2023 годов поставили вопрос о создании собственного производства металлического тантала. Если новое производство будет построено, вся цепочка поставок танталовой продукции от руды до изделий будет локализована в России. Объем российского рынка тантала непрерывно растет, потому вся продукция СМЗ может быть использована исключительно российскими потребителями.
Еще одна задача, которую Руслан Димухамедов решает как глава Ассоциации производителей и потребителей редких и редкоземельных металлов (Ассоциация РМ и РЗМ), — защита российских поставщиков: «Мы предлагаем установить меры таможенного и ценового регулирования поставки редких и редкоземельных металлов. Это практически не повлияет на российских потребителей, поскольку в общей структуре себестоимости затраты на РМ и РЗМ занимают относительно малую долю. Зато повышение обеспечит дополнительные поступления в казну. А главное — создаст стимул для развития российских предприятий, потому что наконец-то покупателям их продукции будет выгоднее приобретать российское сырье, а не зарубежное. Более того, это даст толчок к запуску новых редкоземельных месторождений. Крупные компании готовы рассматривать инвестиции в горные проекты, как только они удостоверятся в наличии спроса».