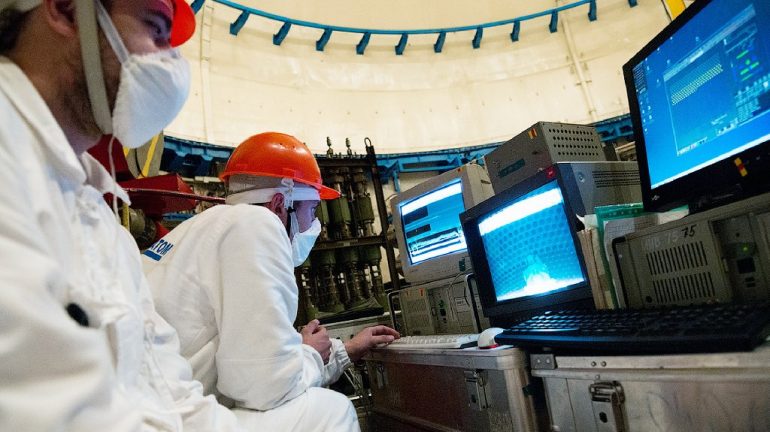
Большая тройка
Кто возглавил рейтинг лидеров ПСР по итогам 2021 года
На заседании Управляющего совета ПСР были подведены итоги системного развития Производственной системы «Росатом» в 2021 году. Из 38 ПСР-предприятий статус «Лидер ПСР» подтвердили 32. В тройку лидеров вошли Балаковская АЭС, ЦКБМ и МСЗ. Представители этих предприятий рассказали об опыте внедрения производственной системы, самых успешных проектах и секретах вовлечения сотрудников.
Балаковская АЭС
Филиал Концерна «Росэнергоатом», электроэнергетический дивизион Росатома
Антон Фяев
Начальник отдела развития Производственной системы «Росатом» филиала АО «Концерн «Росэнергоатом» «Балаковская атомная станция»
— На Балаковской АЭС развитие Производственной системы «Росатом» (ПСР) проходило в несколько этапов. Сначала инструменты ПСР внедрялись на пилотных участках: на централизованных складах атомной станции и в процессе технического обслуживания и ремонта энергоблоков. Системное развертывание бережливого производства началось с 2014 года.
Основной задачей атомной станции является производство электрической и тепловой энергии (мощности) при безусловном обеспечении безопасной, надежной, безаварийной и экономически эффективной работы энергоблоков. В какой момент энергоблок АЭС не вырабатывает электроэнергию? При проведении планово-предупредительного ремонта (ППР), в период которого выполняется ремонт тепломеханического и электротехнического оборудования, оборудования тепловой автоматики, систем безопасности и т. д.
На Балаковской АЭС четыре энергоблока, каждый в плановом порядке ремонтируется. Во время ППР обязательно открываются ПСР-проекты, благодаря которым устраняются производственные потери и сокращаются сроки проведения ремонтной кампании. При этом все запланированные ремонтно-модернизационные работы выполняются качественно и в полном объеме.
Что именно мы делаем? Во-первых, проводим картирование процесса «Техническое обслуживание и ремонт» (ТОиР). Картирование — это разработка карт текущего и целевого состояний, определение потерь в процессе. Также ведем непрерывный производственный контроль: детальное почасовое планирование работ и последующий контроль выполнения детализированных графиков. Мы применяем ПСР-инструмент «Решение проблем методом «Одна за одной»», а именно — выявляем проблемы и решаем их на рабочем месте. Применяем визуальное управление ходом выполнения работ на ремонтной площадке, а также систему 5С для эффективной организации рабочих мест. На производственной площадке организован оперативный штаб по управлению ходом ремонта, на площадке размещаются стенды с графиком и отметками об исполнении, а также всей необходимой информацией о ходе ремонта.
Применение указанных инструментов в 2021 году позволило включить энергоблоки в сеть досрочно и получить дополнительную выручку более 130 млн рублей.
Следует отметить, что инструменты Производственной системы «Росатом» на Балаковской АЭС применяются не только в ходе процесса ТОиР. На станции функционируют инфоцентры — от уровня руководителей до лидеров малых групп, реализуются ПСР-проекты, создаются ПСР-образцы.
В настоящее время с уверенностью могу сказать, что ПСР охватывает абсолютно всю деятельность атомной станции. В качестве примера приведу один из моих самых любимых ПСР-образцов — «Процесс обработки спецодежды для зоны контролируемого доступа в спецпрачечной Балаковской АЭС». Ключевой проблемой на данном производственном участке была низкая производительность, из-за чего персоналу во время плановых ремонтов приходилось задерживаться на работе. И это несмотря на то, что был задействован весь штат и все имеющееся оборудование.
>350
ПСР-проектов реализовано на Балаковской АЭС с 2015 года
~119 млн кВт⋅ч
дополнительная выработка за счет сокращения сроков ремонта энергоблока № 1 в 2021 году
Цифры
Сначала мы открыли ПСР-проекты с применением базовых инструментов бережливого производства. По итогам нам удалось повысить производительность без увеличения штатной численности персонала и количества задействованного оборудования. Кроме того, за счет достигнутых результатов непрерывного выявления и устранения проблем, подачи предложений по улучшению, а также по итогам анализа выявленных лучших практик удалось добиться еще большей производительности и создать из этого участка настоящий ПСР-образец. Опытом создания этого ПСР-образца Балаковская АЭС не раз обменивалась с другими предприятиями.
Своими положительными практиками и наработками в области ПСР мы охотно делимся не только с предприятиями отрасли, но и с организациями вне контура Росатома. Так, в апреле 2019 года в рамках изучения передовых практик внедрения и развития ПСР на нашей станции состоялся референс-визит представителей ПАО «Газпром нефть». А в апреле 2022 года к нам с аналогичным визитом приехали представители самарской компании «Транснефть — Приволга». Мы продемонстрировали коллегам итоги внедрения ПСР на АЭС в 2021 году, наши ПСР-образцы и поделились опытом развертывания ПСР. Обращались к нам и другие внеотраслевые предприятия. Например, побывали у нас и специалисты ПАО «Т Плюс», тоже сторонняя организация, занимающаяся теплоснабжением.
Очень важно внедрять инструменты бережливого производства и на предприятиях, которые являются поставщиками продукции для АЭС. Ведь мы заинтересованы в том, чтобы получать качественные изделия в договорные сроки, без задержки. Так, в конце 2021 года мы завершили трехлетний цикл развития ПСР на предприятии АО «НП «Подольсккабель», а в текущем году приступили к внедрению производственной системы на ООО «Силур» в Перми. Производственная система, которая у них внедряется, аналогична нашей, со всеми требованиями, которые предъявляются к предприятиям атомной отрасли.
АО «Центральное конструкторское бюро машиностроения»
Входит в АО «Атомэнергомаш», машиностроительный дивизион Росатома
Вадим Коренюк
Руководитель проектного офиса ЦКБМ
— Первые изменения от внедрения ПСР на нашем предприятии начались в 2013–2014 годах — тогда стартовали первые работы по выстраиванию потока изготовления выемной части ГЦНА. Параллельно с этим началось постепенное внедрение системы 5С. До 2015 года у предприятия были большие трудности со своевременной поставкой оборудования заказчику, наблюдались срывы сроков даже при небольших объемах производства. Тогда и было принято решение открыть глобальный для предприятия проект по созданию образцового ПСР-потока при производстве ГЦНА-1391. В основе работы был принцип «точно вовремя», который задал направление развития всех процессов.
Еще одним масштабным проектом стала релокация производства. Дело в том, что тогда в центре Санкт-Петербурга на реке Охта у нас была большая производственная площадка, которая занимала 20 тыс. м² и включала в себя более 300 единиц оборудования. Эту площадку в соответствии с планом по реконструкции города нам нужно было освободить. Пришлось развернуть масштабную работу по перемещению производства из центра города на производственные площадки Кировского завода и филиала «ЦКБМ 2» в Сосновом Бору. За год сотрудникам ЦКБМ удалось разработать новые планировочные решения, подготовить производственные площадки под оборудование и транспортировать его без отрыва от производственного процесса. В филиале «ЦКБМ 2» отремонтировали и заново построили лаборатории, термический участок, рентген-камеру, теплый склад ЦМС и заготовительный участок. В филиале «ЦКБМ 2» также размещены производственные цеха механической обработки, сборки, упаковки, но самое главное — уникальный испытательный стенд, имитирующий работу насоса на станции.
Сейчас в ЦКБМ генеральный директор и руководители высшего звена управления открывают и реализуют ПСР-проекты, направленные на сокращение времени протекания процессов и поддержание уже достигнутых результатов. В этом году в работе находится 30 проектов. Все чаще открытие ПСР-проектов инициируют сами сотрудники: видят проблемы в процессе и посредством реализации ПСР-проекта оптимизируют его.
Работая в должности начальника заготовительного производства, я реализовал ПСР-проект, который в 2019 году занял второе место в Росатоме в номинации «Эффективное использование ресурсов». Суть проекта — в оптимизации процесса вырезки заготовок из листового проката, в частности работы с деловыми остатками. Тематика была выбрана из-за большого количества проблем в процессе вырезки заготовок — зачастую небольшие заготовки вырезались из целого листа, оставалось много неиспользованного материала, деловых остатков, которые заполняли склад и по итогу утилизировались как лом. В стоимость изделия приходилось закладывать стоимость целого листа, из-за этого увеличивалась себестоимость заказа. После детального рассмотрения карты процесса и реализации ряда мероприятий я создал базу раскроя деловых остатков. Это позволило оператору гидроабразивной резки производить раскрой оперативно и оптимально. Также деловые остатки стали иметь адресное хранение на складе, что сократило время на поиски и идентификацию. В итоге процент материала, который уходил на металлолом, сокращался и при этом оптимизировались площади складирования. Экономический эффект проекта составил более 2 млн рублей.
Если говорить об общем влиянии внедрения Производственной системы «Росатом» на результаты работы предприятия — очевидно, что производительность значительно увеличилась. Основным производственным потоком у нас является поток изготовления выемной части главного циркуляционного насосного агрегата (ГЦНА). На момент внедрения ПСР-инструментов на этом потоке производственный цикл изготовления составлял 197 рабочих дней, сейчас выемная часть у нас изготавливается за 89 дней. Мы ежегодно сокращаем время протекания процессов, задействованных в изготовлении ГЦНА, применяя ПСР-инструменты и проектную деятельность, активно используя весь наработанный ранее опыт. Есть еще яркий пример улучшения времени протекания процесса в потоке «00-группы» (обвязка ГЦНА), которое сейчас составляет 63 дня, а на старте было 120 дней, также мы сократили на 12% незавершенное производство.
326
ПСР-проектов реализовано в ЦКБМ с 2013 года
2500
предложений по улучшениям подано на предприятии
>200
визитов прошло на предприятии в рамках обмена опытом
Цифры
На сегодняшний день в ЦКБМ действуют пять участков ПСР-образцов в производственных потоках и один участок в процессе подготовки производства. На участках внедрены такие ПСР-инструменты, как 5С, тянуще-восполняющая система, стандартизированная работа, производственный анализ, которые позволили решить на участках проблематику по сокращению незавершенного производства (НЗП), по сокращению времени протекания процесса (ВПП) изготовления деталей, по оптимизации и стандартизации технологических процессов изготовления изделий.
Развитие и внедрение производственной системы зависит от того, насколько серьезно организация подходит к решению этой задачи. Производственная система должна затрагивать работу всей хозяйственной деятельности организации, внедрение ПСР-инструментов должно оптимизировать бизнес-процессы, выявить скрытые потери и устранить их. Я считаю, что успех внедрения ПСР — в грамотном переформатировании работы и понимании процессной части, того, как все устроено. Нельзя заниматься только культурой производства, или цифровизацией, или созданием процессов, все это тесно связано между собой. Мы не должны думать, что мы сейчас все цифровизируем, купим много нового оборудования, приборов и у нас тут же улучшится работа. Далеко не факт. Пока мы не разберемся с процессом, не поймем его, не погрузимся в него, этого не будет. Так что самое важное — сесть и детально разобраться в том, как все устроено и где узкие места. Ну и, конечно, прислушиваться к сотрудникам. Никто лучше них самих не знает, как им наиболее эффективно выполнять свои рабочие функции.
АО «Машиностроительный завод»
Входит в АО «ТВЭЛ», топливный дивизион Росатома
Алексей Павлинов
Начальник отдела планирования, исследования и контроля производства МСЗ
— Внедрение ПСР у нас на производстве началось с 2009 года. Тогда было два пилотных участка: один — на базе цеха № 46, это цех изготовления твэлов, и второй — участок изготовления дистанционирующих решеток цеха № 52. Вот с той поры и началось развитие Производственной системы «Росатом». Но важно отметить, что фундамент у нас был и до этого — предприятие и раньше занималось повышением эффективности своих процессов, может, не столь системно.
На старте внедрения ПСР мы перед собой поставили цель повысить производительность труда. В частности, на линии по производству твэлов: производительность линии была повышена с 250 до 350 твэлов в смену. Если брать незавершенное производство — с более чем 2000 твэлов оно снизилось до 600. Ну а если говорить о дистанционирующих решетках, то там незавершенное производство, я имею в виду хранение изделий и деталей на складах, измерялось месяцами. После внедрения ПСР у нас незавершенное производство снизилось буквально до двухнедельной потребности. Как один из плюсов — мы перестали использовать центральный склад, незавершенное производство хранится в цехе производителя, а не вывозится куда-то. И еще один эффект — это снижение времени протекания процесса.
Я убежден, что это все стало возможным в первую очередь благодаря внедрению определенных улучшений на участках. Человеку не требуется наблюдать за работой оборудования, и он начинает осваивать несколько смежных операций. Соответственно, расширяет свои компетенции и успевает выполнить больший объем работы за то же количество времени за счет устранения потерь на рабочих местах.
Последние 10 лет мы занимались производственными процессами непосредственного изготовления, а недавно перешли к обеспечивающим процессам. В первую очередь, это процессы лабораторных исследований, процессы технического ремонта оборудования, планирования производства, материально-технического обеспечения производства. Сейчас на данном этапе перед предприятием стоит цель резко повысить объем выпускаемой продукции по всем направлениям нашей деятельности. Но, к сожалению, достижение цели осложняется нехваткой необходимых специалистов на рынке труда. Поэтому задача у нас сейчас — достигать цели имеющимся количеством специалистов, хотя объемы растут.
Сделать это только за счет модернизации оборудования и покупки нового оборудования неэффективно. На начальном этапе необходимо переформатирование процессов. Мне известен случай на одном из предприятий, когда приобрели хороший станок, а часть программного обеспечения не купили. В итоге станок работал не на полную мощность. Всегда сначала нужно проанализировать ситуацию, где нужны улучшения, которые не требуют больших вложений, оценить потребности и тогда уже принимать решения по закупке нового оборудования.
Важно отметить, что предложения по улучшению выдвигают все сотрудники: и рабочие, и генеральный директор в равной степени. Если директор заинтересован в модернизации процессов, сам является движущей силой, то все получается. В каждом подразделении есть ответственные специалисты. Мастер и сам может реализовать свои предложения. Если ему не будет хватать ресурсов, он обратится к своему непосредственному руководителю, может и в письменном виде представить предложения по улучшению. За это предусмотрено материальное поощрение.
Но кроме материальных выплат, есть сетка разрядов для рабочих. Даже размер премии зависит от активности рабочих. Так же от активности человека зависит и его продвижение по карьерной лестнице. У нас на заводе принцип такой: если ты не был мастером, директором ты не станешь. Портреты победителей конкурсов лидеров малых групп вывешиваются на центральной городской площади. Это тоже своего рода мотивация быть лучшим.
560
ПСР-проектов реализовано на МСЗ с 2009 года
45
проектов реализовано в 2021 году
3400
предложений по улучшениям подано на предприятии
Цифры
Конечно, сейчас количество предложений сократилось — самые проблемные места уже устранили, многое улучшили, и очевидных решений уже нет, нужно вглубь уходить. Но мы давно уже прошли этап изобретения вечного двигателя. Мы не за количество рацпредложений, а за их качество. Каждое предложение должно приносить экономический эффект.
Я горжусь тем, что нашему предприятию удалось сохранить человеческий капитал. И это самое главное наше достижение. Всегда, во все годы предприятие занималось техническим перевооружением. Большая часть производственных линий у нас сейчас отвечает современным требованиям и стандартам. Но самое главное — это человеческий капитал и общение с коллегами. Мы все в отрасли друг друга знаем. Созданы даже так называемые цеховые клубы. Мы состоим в двух из них. Один клуб — это номенклатурное производство, а второй — сборочное. Периодически мы встречаемся, выезжаем на другие предприятия или у себя принимаем коллег. Ну и оперативно можем созвониться или списаться. Бывают случаи, когда приходится экстренно выезжать на другое производство и помогать коллегам налаживать процессы. На одно из предприятий пришлось даже «десант» высаживать на несколько дней. Это нормальная практика. Если есть опробованная методика, которая работает на результат, почему бы не поделиться ею с коллегами. Да и самому учиться никогда не зазорно. Всегда из поездок на другие предприятия стараюсь привезти что-то полезное для своего.